Fundamentele forării puțurilor de petrol și gaze. Informații generale despre forarea puțurilor de petrol și gaze
Forarea puțurilor acoperă o gamă largă de probleme, care sunt dificil de acoperit în mod cuprinzător, pe baza principiului luării în considerare secvențială a fiecărui proces tehnologic și operațiuni, principii de proiectare și principii pentru implementarea lor în producție. Ar trebui să insiste asupra principalelor metode de foraj.
Scopul, scopurile și obiectivele forării puțurilor
Forarea puțului este procesul de construire a unei mine direcționale de lucru de lungime mare și diametru mic (comparativ cu lungimea). Începutul puțului de pe suprafața pământului se numește gura, fundul se numește fund.
Scopurile și sarcinile forajului. Petrolul și gazele sunt produse prin puțuri. Principalele procese ale construcției lor sunt găurirea și fixarea. Este necesară realizarea de construcție de înaltă calitate a puțurilor în volume din ce în ce mai mari, cu o reducere multiplă a timpului de foraj al acestora, pentru a asigura economia națională cu petrol și gaze în cantități din ce în ce mai mari, reducând în același timp intensitatea forței de muncă și energie și costurile de capital. .
Forarea puțurilor este singura sursă de explorare eficientă și de creștere a rezervelor de petrol și gaze.
Întregul ciclu de construcție a puțurilor înainte de punerea lor în funcțiune include următoarele legături secvențiale principale:
1) construirea structurilor de sol;
2) adâncirea sondei, a cărei implementare este posibilă numai atunci când se efectuează două tipuri de lucrări paralele - adâncirea și spălarea efectivă a puțului;
3) separarea straturilor, constând în două tipuri de lucrări consecutive: întărirea (fixarea) sondei cu țevi coborâte conectate într-un șir și astuparea (cimentarea) spațiului inelar;
4) dezvoltarea puţurilor. Adesea, dezvoltarea puțului împreună cu alte tipuri de lucrări (deschiderea rezervorului și fixarea zonei de fund, perforarea, stimularea și stimularea fluxului de fluid etc.) se numește finalizare a puțului.
Clasificarea puțurilor după scop. Sondele conduse pentru petrol și gaze pot fi sistematizate după cum urmează:
structurale și prospective, al căror scop este stabilirea (clarificarea) tectonicii, stratigrafiei, litologiei, aprecierea productivității orizonturilor (fără construcția puțului suplimentar);
explorarea, servind la identificarea obiectelor productive, precum și 5
de asemenea, pentru delimitarea formațiunilor cu petrol și gaze deja dezvoltate;
minerit (operational) destinat extragerii petrolului si gazelor din interiorul pamantului. În această categorie sunt incluse și puțurile de injecție, de evaluare, de observare și piezometrice;
injecție, concepută pentru a pompa apă, gaz sau abur în rezervoare pentru a menține presiunea rezervorului sau a trata zona fundului găurii. Aceste măsuri vizează prelungirea perioadei modului curgător de producere a petrolului sau creșterea eficienței producției;
avansarea producției, servind pentru producția de petrol și gaze cu rafinarea simultană a structurii formațiunii productive;
evaluare, al cărei scop este de a determina saturația inițială apă-ulei și saturația reziduală cu ulei a rezervorului (și alte studii);
control și observare, concepute pentru a monitoriza obiectul de dezvoltare, a studia natura mișcării fluidelor din rezervor și modificările saturației de motorină a rezervorului;
sunt forate sonde de referință pentru a studia structura geologică a regiunilor mari, pentru a stabili modelele generale de apariție a rocilor și pentru a identifica posibilitatea formării zăcămintelor de petrol și gaze în aceste roci.
Protecția Naturii. Activitatea de producție a întreprinderilor de foraj este în mod inevitabil asociată cu un impact provocat de om asupra obiectelor de mediu. În virtutea caracteristici specifice operațiunile miniere, procesele de construcție a puțurilor afectează negativ lito-, hidro- și biosfera. Tehnogeneza în timpul forării puțurilor este de natură chimico-toxică și fizico-mecanică și se manifestă prin încălcarea echilibrului ecologic natural al ecosistemelor, o scădere a valorii economice naționale a hidrosferei, o scădere a resurselor și potențialului biogenetic al biosferei și degradarea componentelor individuale ale mediului natural. Pentru a preveni poluarea mediu inconjuratorîn timpul construcției puțurilor ar trebui elaborat un set de măsuri de mediu.
Protecția mediului în timpul construcției puțurilor include:
protecția subsolului de poluare și utilizarea rațională a resurselor minerale naturale;
protecţie suprafața pământului(pedo-, hidro- și biosferă) și bazinul aerian din impactul negativ al factorilor tehnogeni în timpul forajului și dezvoltării zăcămintelor de petrol și gaze.
Protecția subsolului este un set de măsuri pentru extracția cât mai completă a unui mineral sau reducerea maximă posibilă a pierderilor acestuia, utilizarea cât mai rațională a resurselor minerale în economie nationala excluzând pierderile nejustificate de materii prime minerale și combustibil, precum și impacturile negative asupra naturii.
Protecția suprafeței pământului și a bazinului aerian este un ansamblu de măsuri juridice, organizatorice, economice și activitati de inginerie pentru a exclude contaminarea obiectelor hidro-, lito- și biosferei cu materiale, substanțe chimice, fluide de proces utilizate în operațiunile de foraj, deșeurile generate, precum și impactul fizic și mecanic asupra componentelor mediului natural, conducând la perturbarea funcționării normale a ecosistemelor.
Conservarea mediului în industria petrolului și gazelor la un nivel (normativ) sigur din punct de vedere ecologic are propriile sale caracteristici, care trebuie luate în considerare la construcția sondelor, dezvoltarea și exploatarea zăcămintelor de petrol și gaze. Principalele includ următoarele:
1) prevenirea distrugerii acoperirii Pământului și a vegetației în timpul construcției puțurilor;
2) prevenirea pătrunderii nămolului de foraj (sau a filtratului acestuia) în pori și fracturi ale formațiunilor minerale. Mai ales periculoase sunt fracturile hidraulice cu pierderea ulterioară a fluidului de foraj;
3) prevenirea manifestărilor deschise nereglementate de gaze, petrol și apă în scopul economisirii mineralelor;
4) fixarea fiabilă, durabilă a forajelor cu separarea perfectă a straturilor și prevenirea absorbției nămolului de ciment sau a filtratului acestuia la o adâncime mai mare decât cea prevăzută de considerente tehnologice;
5) împiedicarea deplasării fluidelor între formațiuni din orice motiv;
6) astuparea fiabilă a puțurilor care s-au dovedit a fi „uscate”, epuizate sau de urgență, pentru a preveni mișcarea fluidelor de la rezervor la rezervor;
7) implementarea măsurilor, utilizarea dispozitivelor și proceselor tehnologice care prevăd separarea tuturor straturilor, și nu a unei părți din ele, în secțiune sau etanșarea numai a gurii pentru a preveni deplasarea fluidelor la suprafața de zi;
8) injectarea unor volume semnificative de diverse soluții și materiale în rezervoare în timpul forajului în condiții de pierdere;
9) impact asupra formațiunilor prin diverse metode (termice, chimice, energetice etc.) în scopul creșterii și accelerarii fluxului de fluide către puț;
10) retragerea forțată a fluidelor din rezervoare;
11) injectarea unor volume mari de apă în rezervoare pentru a restabili sau menține presiunile din rezervor;
12) prezența unui număr semnificativ de puțuri chiar și în cadrul aceluiași câmp, ceea ce face dificilă controlul tuturor obiectelor;
13) arderea gazului asociat;
14) transportul de petrol și gaze în nave-cisternă pe mare (scurgerile de petrol și gaze în acest caz, precum și în timpul forajului, producția și accidentele contribuie la poluarea mediului).
Motivele enumerate și multe alte obligă angajații întreprinderilor de petrol și gaze să ia toate măsurile stabilite și să prezinte cerințe legale pentru a preveni încălcările protecției subsolului și poluarea mediului.
Metode și tipuri de foraj. Tehnologia de construcție a puțurilor
Procesul modern de forare a unui puț este un proces tehnic și tehnologic complex, constând dintr-un lanț de verigi, defectarea uneia dintre ele poate duce la complicații, accidente sau moartea sondei.
Tabelul 1.1 Metode de foraj
Metoda de foraj
Definiție
rotativ
Rotativ
Turbină
Volum
Bormasina electrica
Diamant
Carbură
Pușcă
Coarda de soc
Tija de soc
Soc-rotație
Hidropercuția
vibrând
hidrodinamic
Termic
electrofizice
Exploziv
Chimic
cu spălare
Cu epurare
Foraj mecanic, în care forța de rupere este generată de rotația continuă a sculei de tăiere a rocii cu aplicarea unei sarcini axiale
Foraj rotativ, în care șirul de foraj este rotit de o instalație cu un rotator de tip rotativ
Foraj rotativ, în care unealta de tăiere a rocii este rotită de un turboforător
Găurire rotativă, în care unealta de tăiat rocă este rotită de un motor cu șurub (de deplasare) Găurire rotativă, în care unealta de tăiat rocă este rotită de un burghiu electric
Foraj rotativ, în care roca este spartă cu o unealtă de tăiat rocă armată cu diamant Foră rotativă, în care roca este spartă cu o unealtă de tăiat rocă armată cu metal dur
Foraj rotativ, în care roca este distrusă prin împușcătură
Foraj mecanic, în care forța de rupere este generată de impactul sculei de tăiere a rocii
Foraj cu percuție, în care mișcarea alternativă generată de mașină este transmisă instrumentului de tăiat roca prin țevi de foraj
Foraj mecanic, în care forța distructivă este creată ca urmare a impactului și rotației combinate a sculei de tăiere a rocii
Foraj rotativ cu percuție, în care șocurile sunt transmise sculei de tăiere a rocii de un ciocan hidraulic
Foraj, în care roca este distrusă de un jet de fluid de înaltă presiune
Foraj, în care roca este distrusă prin acțiunea termică
Foraj în care roca este distrusă de forțele rezultate în urma unei descărcări electrice Foraj în care roca este distrusă de forțele rezultate în urma exploziei
Foraj, în care roca este distrusă sub influența reactivilor care intră într-o reacție chimică cu aceasta Foraj, în care produsele distrugerii rocii sunt îndepărtate prin curgerea fluidului de foraj
Foraj, în care produsele de distrugere a rocilor sunt îndepărtate printr-un flux de gaz
Indiferent de metoda de distrugere a rocilor, procesul de forare a puțurilor include o serie de operațiuni:
coborârea țevilor de foraj (șiruri) cu o unealtă de tăiere a pietrei în puț;
distrugerea rocii faciale;
îndepărtarea stâncii distruse din fântână;
ridicarea țevilor de foraj din puț pentru a schimba instrumentul de prăbușire uzat și repeta operația;
întărirea (fixarea) pereților puțului atunci când se atinge o anumită adâncime prin conducte de tubaj, urmată de cimentarea spațiului dintre peretele puțului și țevile coborâte (separarea straturilor).
Există și alte operațiuni de natură tehnologică și geofizică care nu sunt implicate în forarea directă a sondei, dar sunt și obligatorii.
La forarea puțurilor se folosesc multe metode de foraj (Tabelul 1.1).
Metode de bază de foraj
Metodele obișnuite de foraj rotativ - foraj rotativ, cu turbină și foraj electric - implică rotirea unui instrument de lucru care distruge roca - un pic. Roca distrusă este îndepărtată din puț prin fluid de foraj, spumă sau gaz injectat în șirul de conducte și ieșind prin inel.
Foraj rotativ. În găurirea rotativă, burghiul se rotește cu întreaga garnitură de foraj; rotația este transmisă prin tubul de lucru de la rotorul conectat la centrala printr-un sistem de transmisie. Greutatea pe burghie este creată de o parte din greutatea țevilor de foraj.
În forajul rotativ, cuplul maxim al coardei depinde de rezistența rocii la rotația burghiei, de rezistența la frecare a șnurului și a fluidului rotativ față de peretele găurii și de efectul inerțial al vibrațiilor elastice de torsiune.
În practica mondială de foraj, metoda rotativă este cea mai comună: peste 90% din operațiunile de foraj sunt efectuate folosind această metodă. ÎN anul trecut a existat o tendință de creștere a volumului de foraj rotativ în Federația Rusă, chiar și în regiunile de est. Principalele avantaje ale metodei rotative față de metoda cu turbină sunt controlul independent al parametrilor modului de foraj, posibilitatea declanșării unor căderi mari de presiune pe burghiu, o creștere semnificativă a penetrației pe rulare de bit datorită frecvențelor mai mici de rotație a bitului etc.
Foraj cu turbina. În metoda de foraj cu turbină, bitul este conectat la arborele turbinei turboforurului, care este antrenat de mișcarea fluidului sub presiune printr-un sistem de rotoare și statori. Sarcina este creată de o parte din greutatea țevilor de foraj.
Cel mai mare cuplu se datorează rezistenței rocii la rotația bitului. Cuplul maxim în conducte, determinat de calculul turbinei (valoarea cuplului de frânare a acesteia), nu depinde de adâncimea sondei, viteza bitului, sarcina axială asupra acesteia și proprietățile mecanice ale rocile fiind forate. Coeficientul de transfer de putere de la sursa de energie la unealta distructivă în forajul cu turbină este mai mare decât în forajul rotativ.
Cu toate acestea, cu metoda de foraj cu turbină, este imposibil să controlați în mod independent parametrii modului de foraj, în timp ce costurile de energie pe 1 m de penetrare sunt mari, costurile de amortizare a turboforatoarelor și întreținerea atelierelor pentru repararea turboforatoarelor, etc.
Metoda de foraj cu turbine a devenit extrem de răspândită în Federația Rusă datorită muncii VNIIBT.
Găurire cu motoare cu șurub (de deplasare). Corpurile de lucru ale motoarelor se bazează pe un mecanism cu șuruburi cu mai multe filete, ceea ce face posibilă obținerea vitezei de rotație necesare la un cuplu crescut în comparație cu turboforatoarele. Motorul de fund este format din două secțiuni - motor și ax. Corpurile de lucru ale secțiunii motorului sunt statorul și rotorul, care sunt elicoidale
mecanism. Această secțiune include și o îmbinare dublă. Statorul este conectat la garnitura de foraj prin intermediul unui sub. Cuplul este transmis de la rotor la arborele de ieșire al arborelui prin intermediul unei conexiuni cu balamale duble. Secțiunea axului este proiectată pentru a transfera sarcina axială în fundul găurii, pentru a absorbi sarcina hidraulică care acționează asupra rotorului motorului și pentru a etanșa partea inferioară a arborelui, ceea ce contribuie la crearea unei căderi de presiune. La motoarele cu șurub, cuplul depinde de căderea de presiune pe motor. Pe măsură ce arborele este încărcat, cuplul dezvoltat de motor crește, iar căderea de presiune în motor crește și ea. Caracteristica de funcționare a unui motor cu șurub cu cerințele pentru extragerea eficientă a biților face posibilă obținerea unui motor cu o turație a arborelui de ieșire de 80-120 rpm cu un cuplu crescut. Această caracteristică a motoarelor cu șurub (de deplasare) le face promițătoare pentru implementare în practica de foraj.
Găurire cu un burghiu electric. Când se utilizează burghie electrice, rotirea burghiei este efectuată de un motor electric (trifazat). curent alternativ. Energia îi este furnizată de la suprafață printr-un cablu situat în interiorul șirului de țevi de foraj. Fluidul de foraj circulă în același mod ca în metoda de foraj rotativ. Cablul este introdus în șirul de țevi printr-un colector de curent situat deasupra pivotului. Burghiul electric este atașat la capătul inferior al garniturii de foraj, iar burghiul este atașat la axul burghiului electric. Avantajul unui motor electric față de unul hidraulic este că viteza de rotație, cuplul și alți parametri ai unui burghiu electric nu depind de cantitatea de fluid furnizată, de proprietățile fizice ale acestuia și de adâncimea sondei și de posibilitatea de control. procesul de funcționare a motorului de la suprafață. Dezavantajele includ dificultatea de a furniza energie motorului electric, mai ales când tensiune arterială crescută, și necesitatea de a sigila motorul de noroiul de foraj.
Direcții promițătoare în dezvoltarea metodelor de foraj în practica mondială
În practica națională și străină, se desfășoară activități de cercetare și dezvoltare în domeniul creării de noi metode, tehnologii și echipamente de foraj.
Acestea includ adâncirea rocilor cu ajutorul exploziilor, distrugerea rocilor cu ajutorul ultrasunetelor, eroziunea, utilizarea unui laser, vibrații etc. O analiză a diferitelor metode indică necesitatea creșterii puterii furnizate la fundul găurii.
Unele dintre aceste metode au fost dezvoltate și sunt utilizate, deși într-o mică măsură, adesea în stadiul experimental.
Metoda hidromecanică de distrugere a rocii la adâncirea puțurilor este din ce în ce mai utilizată în condiții experimentale și de teren. S.S. Shavlovsky a efectuat o clasificare a jeturilor de apă care pot fi utilizate la forarea puțurilor. Clasificarea se bazează pe presiunea dezvoltată, lungimea de lucru a jeturilor și gradul impactului acestora asupra rocilor de compoziție, cimentare și rezistență diferite, în funcție de diametrul duzei, presiunea inițială a jetului și debitul de apă. Utilizarea jeturilor de apă permite, în comparație cu metodele mecanice, creșterea indicatorilor tehnici și economici.
La cel de-al VII-lea Simpozion Internațional (Canada, 1984) au fost prezentate rezultatele lucrărilor privind utilizarea jeturilor de apă în foraj. Capacitățile sale sunt asociate cu alimentarea continuă, pulsativă sau intermitentă cu fluid, prezența sau absența materialului abraziv și caracteristicile tehnice și tehnologice ale metodei.
Forarea prin eroziune oferă rate de adâncire de 4-20 de ori mai rapide decât forarea rotativă (în condiții similare). Esența sa constă în faptul că materialul abraziv - împușcătura de oțel - este furnizat burghiului cu un design special împreună cu fluidul de foraj. Dimensiunea granulelor este de 0,42–0,48 mm, concentrația în soluție este de 6%. Prin duzele bitului, această soluție cu împușcătură este alimentată la fund cu viteză mare, iar fundul este distrus. Două filtre sunt instalate în serie în garnitura de foraj, concepute pentru a îndepărta și reține particulele a căror dimensiune nu le permite să treacă prin duzele burghiei.
Un filtru este deasupra bitului, iar celălalt este sub kelly unde se poate face curățarea. Tratamentul chimic al noroiului de foraj cu împușcătură este mai dificil decât tratarea noroiului convențional, mai ales când temperaturi ridicate, deoarece este necesar să se mențină împușcătura în suspensie în soluție și apoi să se genereze acest material abraziv.
După curățarea prealabilă a fluidului de foraj de gaz și butași cu ajutorul hidrociclonilor, împușcătura este luată și depozitată în stare umedă. Soluția este trecută prin hidrocicloni fini și un degazator și performanța pierdută este restabilită prin tratament chimic. Apoi o parte din fluidul de foraj este amestecat cu împușcătură și introdus în puț, amestecându-se cu fluidul de foraj convențional pe drum (în raportul calculat).
Lasere în foraj. Lasere - generatoare cuantice ale gamei optice - una dintre realizările remarcabile ale științei și tehnologiei. Ei au găsit o aplicare largă în multe domenii ale științei și tehnologiei. Conform datelor străine, în prezent este posibil să se organizeze producția de lasere cu gaz continuu cu o putere de ieșire de 100 kW și mai mult. Eficiența laserelor cu gaz poate ajunge la 20–60%. Puterea mare a laserelor, cu condiția să se obțină densități de radiație extrem de mari, este suficientă pentru a topi și vaporiza orice materiale, inclusiv roci, care, de asemenea, se fisurează și se descuamează.
Densitatea minimă de putere a radiației laser suficientă pentru distrugerea rocilor prin topire a fost stabilită experimental: pentru gresii, siltstone și argile, este de aproximativ 1,2–1,5 kW/cm2. Densitatea de putere a distrugerii efective a rocilor saturate cu petrol din cauza proceselor termice de ardere a uleiului, în special atunci când aerul sau oxigenul sunt suflați în zona de distrugere, este mai mică și se ridică la 0,7–0,9 kW/cm2.
S-a calculat că pentru un puț cu o adâncime de 2000 m și un diametru de 20 cm, trebuie cheltuiți aproximativ 30 de milioane de kW de energie de radiație laser. Forarea puțurilor de o asemenea adâncime nu este încă competitivă în comparație cu metodele tradiționale de foraj mecanic. Cu toate acestea, există fundații teoretice Creșterea eficienței lasere; cu o eficiență de 60%, costurile cu energia și costurile vor scădea semnificativ, iar competitivitatea acestei metode va crește. Când se folosește un laser în cazul forării puțurilor cu adâncimea de 100–200 m, costul lucrării este relativ scăzut. Dar în toate cazurile, în timpul găuririi cu laser, forma secțiunii transversale poate fi
fi programat, iar peretele găurii de foraj va fi format dintr-o topitură de rocă și va fi o masă sticloasă, care va crește coeficientul de deplasare a noroiului de foraj de către ciment. În unele cazuri, este, evident, posibil să se facă fără carcasa de bine.
Firmele străine oferă mai multe modele de burghie cu laser. Acestea se bazează pe un laser puternic plasat într-o carcasă etanșă care poate rezista la presiune ridicată. (Stabilitatea temperaturii nu a fost încă studiată.) În aceste modele, radiația laser este transmisă la fundul găurii printr-o fibră conducătoare de lumină. Pe măsură ce roca este distrusă (topită), burghiul cu laser se mișcă în jos; poate fi prevăzut cu un vibrator instalat în carcasă. Când proiectilul este presat în topirea rocii, pereții puțului pot fi compactați.
În Japonia, a început producția de lasere cu dioxid de carbon, care, atunci când sunt utilizate în foraj, vor crește semnificativ (de până la 10 ori) rata de penetrare.
Secțiunea transversală a puțului în timpul formării trunchiului prin această metodă poate avea o formă arbitrară. Calculatorul setează de la distanță modul de scanare al fasciculului laser conform programului dezvoltat, care permite programarea dimensiunii și formei sondei.
Efectuarea lucrărilor termice cu laser este posibilă în viitor în lucrările de perforare. Perforarea cu laser va oferi controlabilitatea procesului de distrugere a șirului de carcasă, a pietrei de ciment și a rocii și poate asigura pătrunderea canalelor la o adâncime considerabilă, ceea ce va crește cu siguranță gradul de perfecțiune al formațiunii. Cu toate acestea, topirea rocilor, care este oportună la adâncirea puțului, este inacceptabilă aici, ceea ce ar trebui să fie luat în considerare atunci când utilizați această metodă în viitor.
În lucrările casnice există propuneri pentru realizarea de instalații laser-plasmă pentru forarea termică a puțurilor. Cu toate acestea, transportul plasmei la fundul puțului este încă dificil. În prezent, se fac cercetări cu privire la posibilitatea dezvoltării ghidurilor de lumină („tuburi de apă luminoasă”).
Una dintre cele mai interesante metode de influențare a rocilor, care are criteriul universalității, este metoda de topire a acestora prin contact direct cu un vârf refractar - un penetrator. Progresul semnificativ în crearea materialelor rezistente la căldură a făcut posibilă transferarea problemei topirii rocilor în domeniul proiectării reale. Deja la temperaturi de ordinul 1200–1300 °C, metoda de topire este eficientă în soluri afânate, nisipuri și gresii, bazalt și alte roci din subsolul cristalin. În rocile complexului sedimentar, pătrunderea rocilor argiloase și carbonatice necesită aparent o temperatură mai ridicată.
Metoda de forare prin topire face posibilă obținerea unei cruste vitroceramice suficient de groasă, cu pereți interiori netezi pe pereții puțului. Metoda are un coeficient ridicat de intrare de energie în rocă - până la 80–90%. În acest caz, cel puțin în principiu, se poate rezolva problema eliminării topiturii de pe fund. Plecând prin canalele de evacuare sau pur și simplu curgând în jurul unui penetrator neted, topitura, solidificându-se, formează un nămol, a cărui dimensiune și formă pot fi controlate. Tăierile sunt efectuate de fluidul care circulă deasupra garniturii de foraj și răcind partea superioară a acestuia.
Primele modele și mostre de foraje termice au apărut în anii 60, iar teoria și practica topirii rocilor au început să se dezvolte cel mai activ de la mijlocul anilor 70. Eficiența procesului de topire este determinată în principal de temperatura suprafeței penetratorului și proprietăți fizice roci și depinde puțin de proprietățile lor mecanice și de rezistență. Această împrejurare determină o anumită universalitate a metodei de topire în sensul aplicabilității acesteia pentru scufundarea diferitelor roci. Intervalul de temperatură de topire al acestor diferite sisteme poliminerale multicomponente se încadrează în general în intervalul 1200-1500°C la presiunea atmosferică. Spre deosebire de metoda mecanică de distrugere a rocilor prin topire, cu creșterea adâncimii și temperaturii rocilor subiacente, aceasta crește eficiența acesteia.
După cum sa menționat deja, în paralel cu penetrarea, pereții puțului sunt fixați și izolați ca urmare a creării unui strat inelar vitros impermeabil. Nu este încă clar dacă va avea loc uzura stratului de suprafață al penetratorului, care este mecanismul și intensitatea acestuia. Este posibil, totuși, ca forarea prin fuziune, deși cu o rată redusă, să poată fi efectuată continuu în intervalul determinat de proiectarea sondei. Acest design în sine, datorită fixării continue a pereților, poate fi simplificat semnificativ, chiar și în condiții geologice dificile.
Evident, este posibil să ne imaginăm proceduri tehnologice asociate doar cu fixarea și izolarea pereților în serie cu scufundarea arborelui prin metoda forajului mecanic convențional. Aceste proceduri se pot aplica numai intervalelor care sunt periculoase din cauza posibilității diverselor complicații.
Din punct de vedere al implementării tehnice, este necesar să se asigure un fir de curent la elementele de injecție ale penetratorului, similar cu cel utilizat în forajul electric.
Tipuri de foraj
Forajul modern permite forarea puțurilor în diverse scopuri, diametru, configurație și orientare a puțului.
Forarea puţurilor verticale. Nu există puțuri strict verticale - toate au o oarecare curbură, abatere de la verticală. Nivelul modern de inginerie și tehnologie face posibilă forarea puțurilor cu o abatere a sondei de la verticală până la 2°.
V.S. Fedorov, după ce a studiat cauzele curburii puțului, a ajuns la concluzia că acestea pot fi împărțite în geologice (negestionate) și tehnice și tehnologice (gestionate).
Motivele geologice includ: unghiul de întâlnire al bitului cu planul de formare, alternanța rocilor în ceea ce privește rezistența și grosimea lor, unghiul de curbură al puțului (determinat de unghiul de scufundare al formațiunilor și nu poate fi mai mare decât acesta din urmă). ).
Motivele tehnice și tehnologice includ: tipul burghiei, modul de foraj, rigiditatea fundului garniturii de foraj, curbura elementelor instrumentului de foraj, îndoirea țevilor de foraj sub sarcină, verticalitatea și coincidența axei forului cu centrul forajului. masă rotativă și direcția acesteia, instalarea orizontală a mesei rotorului.
Impactul acestor cauze poate fi redus la aproape zero.
Înainte de a începe forarea, este necesar să se asigure centrarea forței, corespondența axelor de simetrie ale forului și direcția, instalarea orizontală a mesei rotorului, rectitudinea primelor țevi de foraj și Kelly.
La începutul forajului, kellyul și primele țevi ar trebui să intre în stâncă strict vertical, fără a se legăna.
Prevenirea curburii găurii de foraj în timpul forării se reduce la măsurarea curburii, utilizarea ansamblurilor de găuri inferioare (BHA) și selectarea modului de forare. Ansamblurile trebuie să aibă permeabilitate și stabilitate longitudinală în sondă în timpul forării sondei, să nu creeze rezistență hidraulică semnificativă în timpul deplasării fluidului de foraj etc.
KNVK este utilizat după ce se lucrează prin orificiu direct de sub sabotul coloanelor intermediare, precum și de la începutul găuririi cu acele biți, al căror diametru corespunde diametrului aspectului. Uzura permisă a calibratoarelor și centralizatoarelor nu trebuie să depășească 3 mm în diametru, iar gulerele pătrate - 2 mm. Dispozițiile fundului garniturii de foraj diferă unele de altele, elementele lor sunt reprezentate de calibratoare, centralizatoare, stabilizatoare, alezoare, volante (gulere de foraj scurte - gulere), etc.
Eficiența BHA este determinată în principal de respectarea acestora cu condițiile de lucru, rigiditate, diferența de diametre ale bitului și elementelor de asamblare, lungimea, succesiunea și numărul de instalare a elementelor de asamblare, natura configurației secțiunii transversale. a sondei.
Scopul elementelor care alcătuiesc aspectul fundului șirului de foraj nu este același.
Calibratoarele sunt proiectate pentru a calibra diametrul sondei și pentru a îmbunătăți performanța biților. Sunt produse în mai multe versiuni: KL-214 - calibrator cu lame pentru un diametru de 214 mm cu nervuri situate de-a lungul generatricei; KLS-190 - calibrator cu palete pentru un diametru de 190 mm cu nervuri dispuse in spirala; KVZ-214 - calibrator cu dinți retractabili pentru un diametru de 214 mm; calibrator monocon pentru un diametru de 214 mm. În găurirea rotativă, calibratoarele sunt instalate într-un aranjament direct deasupra burghiului.
Centralizatoarele sunt proiectate pentru a centra garnitura de foraj la locul instalării lor. Sunt produse în mai multe versiuni: metal TsM-269, cadru cauciuc TsR-214, articulat TsSh-269, intersecție TsS-295 și centralizator de arbore turboforfor TsVT-295.
Stabilizatoarele, al căror rol este jucat de gulerele de foraj, țevile ponderate cu profil poligonal sau cele spiralate, sunt proiectate pentru a centra șirul de foraj în secțiunea lungimii de stabilizare. Ele sunt împărțite în ST-uri cilindrice-245-4,5 m cu un diametru exterior de 245 mm și o lungime de 4,5 m; spirală SS-190-4,0 m; pătrat SK-190-6,5 m cu o diagonală de 190 mm și o lungime de 6,5 m etc.
Volanții, al căror rol este îndeplinit de gulerele scurte de foraj (CD), servesc la echilibrarea masei rotative a arborelui turboforurului. Sunt instalate sub arborele turboforatorului.
Expansorul este proiectat pentru a extinde sondele. Cele mai comune sunt expansoarele cu trei conuri (trei perechi de conuri sunt montate pe osii în carcasă, ele sunt situate în jurul circumferinței sub
unghi de 120° unul față de celălalt). Expansoarele triconice sunt produse în mai multe diametre - 243, 269, 295, 345, 395 și 455 mm.
De asemenea, produc alezoare cu patru și șase lame, pilot cu un singur con și alezoare.
Curbura sondei trebuie măsurată. Pentru aceasta se folosesc inclinometre discrete si continue, care permit masurarea abaterii sondei de la verticala (in plan vertical) si a curburii in azimut (unghiul dintre planul vertical in care axa sondei deviate). se află și planul vertical care trece prin capătul nordic al acului magnetic) până la 50°. Rezultatele măsurătorilor sunt introduse în tabel la anumite intervale (25–50 m) ale adâncimii sondei și pot fi înregistrate sub formă de curbe continue (inclinograme) - grafice ale proiecțiilor sondei pe plan orizontal. Graficele sunt construite pe o anumită scară, indică direcția meridianului magnetic, scara orizontală, abaterea totală, iar fiecare punct marchează adâncimea și unghiurile de înclinare.
Dispozitivul Petrosyan se bazează pe distrugerea (coroziunea) sticlei de către acidul fluorhidric (acid fluorhidric HF) la granița cu aerul. Sticla introdusă vertical în dispozitiv intră în contact cu acidul fluorhidric, lăsând o urmă, a cărei direcție a liniei indică unghiul de curbură. Colțul ăsta? măsurată direct cu un raportor sau calculată prin formula
unde a este diferența de înălțime a liniei de urmărire pe sticlă, mm; D – lungimea sticlei, mm.
Aparatul lui Petrosyan este realizat în trei versiuni. Este aruncat în țevi de foraj sau coborât pe un fir folosind un troliu manual sau mecanic special.
Foraj direct. O sondă deviată diferă de o sondă verticală printr-un decalaj dat al feței de capăt față de verticala care trece prin capul sondei.
Forarea puțurilor înclinate este posibilă prin metode cu turbină și rotative. Curbura sondei este realizată prin utilizarea unor ansambluri speciale ale fundului garniturii de foraj, care asigură o forță de deviere asupra burghiei sau eșecului asimetric al fundului de foraj, sau ambele.
Poziția spațială necesară a sondei este realizată prin orientarea ansamblurilor de deviere ale fundului garniturii de foraj înainte și în timpul forării. Ca deflector pentru găurirea turbinei, se folosesc scheme care includ unul sau mai multe centralizatoare, două centralizatoare amplasate excentric, un niplu excentric, un sub curbat, deflectoare speciale precum OT, OTS, OTSH. Ansamblurile centralizatoare simple sau multiple pot controla doar unghiul zenit al puțului. Toate celelalte vă permit să schimbați și azimutul puțului.
Un subconsum curbat este o conductă de ramificație cu pereți groși cu axe longitudinale care se intersectează ale conexiunilor filetate de conectare. Unghiurile dintre axele de intersectare sunt 1,5–3,5°. Creșterea unghiului menționat peste 3,5°, în general, nu crește rata de curbură. Un subconsum curbat este inclus în aspect, de obicei între o secțiune
turbodrill ei sau un turbodrill și guler de foraj scurtat. În mod evident, rata de modificare a curburii depinde de unghiul subconjuncturii îndoite, precum și de unghiul zenital curent al sondei. În conformitate cu instrucțiunile pentru forarea puțurilor înclinate din pernițele puțurilor din câmpurile petroliere Vestul Siberiei(RD 39-2-171-79) la găurire, este prevăzut următorul aspect: un burghiu cu un diametru de 295 mm, un turboforghiu ZTSSh-240-1 secțiune sau T12MZB-240, un sub curbat, un guler de foraj cu un diametrul de 178 mm și o lungime de 12 m. ) din unghiul zenital curent poate fi reprezentat ca
Da = k + ba2,
unde k și b sunt coeficienți empirici.
În tabel. 1.2 arată valorile lui k și b pentru diferite unghiuri de oblice și tipuri de motoare de fund.
Forța de deviere în aranjamentul cu un niplu excentric apare din cauza instalării unei căptușeli elastice (cauciuc) pe niplul turbodrill.
La foraj cu turboforatoare secționale, arborii și corpurile secțiunilor superioare și inferioare ale turboforumului sunt conectate la un unghi de 1-2°, ceea ce asigură un set de curbură la forarea sondei; Deflectoarele OT și OTS sunt sub formă curbată instalată între mamelon și corpul turboforghiului. În acest caz, arborele este despicat, mamelonul servește ca suport radial pentru partea inferioară a arborelui.
Dispozitivele de deviere utilizate în forajul rotativ și tehnologia forării puțurilor direcționale au propriile caracteristici. În acest caz, deflectoarele sunt folosite doar în momentul inițial pentru a da portbagajului direcția dorită. Numărul de deviere care sunt necesare pentru a asigura o curbură dată a sondei determină capacitatea rocilor traversabile și a straturilor lor intermediare de a devia sonda de foraj de la direcția de proiectare. Curbura artificială a sondei se realizează prin selectarea dispozițiilor adecvate ale fundului șirului de foraj în anumite condiții de foraj. Deviatorii (Fig. 1.1) sunt, de asemenea, specifici și sunt dispozitive în formă de pană cu o direcție înclinată pentru bit. Au o secțiune semicirculară sau în formă de V cu dispozitive pentru montare într-un orificiu deschis sau cu carcasă. Prin proiectare, acestea sunt nedemontabile, nedemontabile (lungime 2,5–4,5 m), lăsate în puț și recuperate după ce procesul de foraj a fost efectuat în direcția stabilită (aproximativ 15 m dintr-un puț nou).
T a b l e 1.2
Coeficienți empirici și valori limită ale unghiului zenital pentru diferite tipuri de turboforatoare
Unghi de înclinare
sub strâmb
ZTSSH-240 (1 secțiune)
T12MZB-240
coeficientul k
coeficientul k
Unghiul zenital maxim? n, grad
3° 45" 3° 00 2° 30" 2° 00
1,60 1,35 1,20 1,00
57,0 52,6 48,0 45,0
1,56 1,38 1,20
55,8 52,6 48,0
N o t e. Coeficientul b = 0,0005.
Orez. 1.1. Tipuri de dispozitive de deviere în găurirea rotativă:
a - lucru cu o pană deflectorală: 1 - instalarea unei pane, 2 - forarea sondei, 3 - îndepărtarea panei, 4 - extinderea sondei; a - lucrul cu un whipstock: 1 - instalare whipstock, 2, 3 - forare găuri, 4 - extindere găuri
S.U.A). Deviatoarele nerecuperabile sunt utilizate în puțurile tubate. Deasupra au o priză pentru ghidarea bitului și un dispozitiv de prindere în puț.
În biciurile recuperabile, în partea superioară există un cuplaj (pentru ridicarea acestora) cu diametrul egal cu diametrul părții inferioare a bitului, iar în partea inferioară există o proeminență ascuțită care pătrunde în stâncă la nivelul fundul orificiului și împiedică rotirea biciului.
Pentru a stabiliza scăderea unghiului zenit al sondei, atât în forajul rotativ, cât și în cazul forajului cu turbină (electrică), se folosesc scheme cu un număr diferit de centralizatoare și amplasarea acestora.
Proiectarea puțurilor direcționale se reduce la alegerea tipului de profil (proiecții verticale și orizontale), la calculul traiectoriei poziției axei sondei în spațiu, la alegerea layout-urilor pentru implementarea profilului calculat și modul de forare.
Profilele puțurilor pot fi proiectate într-un singur plan (acesta este tipul obișnuit de profil) și ținând cont de curbura spațială (profilul de tip spațial). Acestea din urmă sunt utilizate, din păcate, mai rar, iar utilizarea lor este asociată cu condiții geologice complexe de foraj, a căror influență asupra curburii spontane este mare.
Găurire cu plăcuțe. Forarea cu tampon este înțeleasă ca o metodă în care capurile de sondă sunt grupate pe un loc comun, iar fețele de capăt sunt situate în punctele corespunzătoare proiectelor de dezvoltare a rezervoarelor.
Odată cu forarea în cluster a puțurilor, lucrările de construcție și instalare în foraj se reduc semnificativ, se reduce volumul de construcție a drumurilor, liniilor electrice, conductelor de apă etc. Cel mai mare efect al forajului în cluster este asigurat atunci când se forează în condiții de mare, în zone mlăștinoase etc. Pentru prima dată în b. În URSS, forajul în cluster a fost efectuat sub conducerea lui N.S. Timofeeva despre despre. Artem în Azerbaidjan. În prezent, 8-24 de puțuri și mai multe sunt forate din platformă.
Principala activitate pregătitoare este pregătirea șantierului pentru construcția de instalații terestre și amenajarea comunicațiilor. Într-o zonă mlaștină sau inundată sunt posibile din punct de vedere tehnic următoarele metode de dezvoltare a acestora: construirea de baraje care înconjoară amplasamentul; construirea de insule artificiale; la un nivel ridicat al apei - construirea de ponturi.
Se folosesc diferite tipuri și variante de bucșă în funcție de condițiile naturale.
Tufișurile sunt împărțite în locale, adică nelegat prin drumuri permanente cu baza; tufișuri situate de-a lungul autostrăzii și tufișuri situate în centrul autostrăzii. În primul caz, puțurile, de regulă, sunt direcționate în toate direcțiile (ventilator), ceea ce vă permite să colectați numărul maxim de capete de sondă într-un grup. Când se forează depozite multistrat, numărul puțurilor dintr-un tampon crește. În cazul clusterelor situate de-a lungul magistralei de transport (Azerbaidjan-Marea, Siberia de Vest), numărul de sonde din cluster este redus în comparație cu numărul de sonde din clusterul local.
În funcție de condițiile geologice și climatice, de tehnologie și topografie, pot fi propuse și utilizate multe scheme de amplasare a puțurilor.
Una dintre principalele caracteristici ale forării puțurilor cu clustere este necesitatea de a respecta condițiile de neintersecție a puțurilor de sondă. Experiența arată că din punctul de vedere al traversării puțurilor adiacente, secțiunile verticale superioare sunt periculoase.
De asemenea, este important să se stabilească diferența minimă în adâncimile verticale ale punctelor de foraj ale sondelor din pereți. Se crede că diferența minimă maximă admisibilă în adâncimea punctelor de foraj ale trunchiurilor puțurilor adiacente ar trebui să fie de 50 m, ceea ce este recomandat ca toleranță atunci când adâncimea sondei nu depășește 1000 m. Conform rezultatelor din poziția reală a trunchiurilor, ajustările corespunzătoare ar trebui făcute la proiectele de foraj puțuri ulterioare.
Forajul cu tampon este utilizat pe scară largă în practica străină și internă de foraj în Siberia de Vest, pe mare etc.
Dezavantajele metodei de foraj direcțional cluster includ: conservarea forțată a puțurilor deja forate până la finalizarea unei sonde din acest cluster pentru a Siguranța privind incendiile, care încetinește rata de dezvoltare a zăcământului; risc crescut de traversare a puțurilor de sondă; dificultăți în efectuarea lucrărilor de capital și a lucrărilor subterane ale puțurilor, precum și în eliminarea grifonilor în condiții de foraj offshore etc.
Foraj multilateral. Esența metodei de foraj multilateral este că unul sau mai mulți puțuri sunt forați din puțul principal de la o anumită adâncime, de exemplu. se foloseste trunchiul principal
repetat. Lungimea utilă a puțurilor din rezervor și, în consecință, zona de drenaj (suprafața de filtrare) crește (Fig. 1.2). Trunchiurile suplimentare pot merge orizontal.
Primele puțuri au fost forate prin această metodă în 1947 pe câmpurile Krasnokamenskoye și Ishimbayevsky. În combinație cu un turbodrill, forajul multilateral s-a dezvoltat cu mai mult succes.
La câmpul Borislavskoye, unghiul maxim de curbură zenital a fost de 53 ° la o lungime de 446 m. În teritoriul Krasnodar, numărul de sonde suplimentare din puțuri multilaterale a fost crescut la cinci sau șase cu o lungime de 50-150 m. și o distanță între cele mai exterioare sonde de până la 300 m. Numărul puțurilor laterale poate ajunge la 10, iar lungimea lor este de 400 m sau mai mult.
Dirijată de A.G. Kalinin, un studiu de fezabilitate pentru unul dintre domenii a arătat că costul unui puț multilateral este de 2-4 ori mai mare decât costul unui puț cu un singur lateral, dar debitul în primul caz este de 18 ori mai mare decât în al doilea. .
Avantajele metodei de foraj multilateral se rezumă la faptul că este posibil să se obțină puțuri cu un debit crescut, să crească recuperarea totală de petrol a câmpului, să reducă numărul de sonde, să implice câmpuri cu viteză redusă, cu permeabilitate scăzută a rocii în dezvoltarea industrială și creșterea capacității de absorbție a puțurilor de injecție.
Foraj orizontal. Până în prezent, în practica mondială, zona de posibilă aplicare pentru deschiderea straturilor productive ale puțurilor orizontale și multilaterale este destul de clar conturată. Deși volumul de foraj nu depășește 1,0–1,5% din volumul total de foraj, cel mai mare efect asupra creșterii producției de curent și a recuperării petrolului se obține la deschiderea rezervoarelor cu fracturare verticală, variabilitate mare a faciesului de-a lungul loviturii, scăzută.
Orez. 1.2. Schema unui puț multilateral
porozitate și permeabilitate, precum și care conțin uleiuri cu vâscozitate ridicată și mobilitate redusă. De asemenea, puțurile orizontale pot fi folosite cu mare succes atunci când pătrund în formațiuni foarte permeabile.
Datorită deschiderii straturilor prin puțuri orizontale, se realizează următoarele:
intensificarea producției de petrol și creșterea valorificării petrolului;
creșterea perioadei de funcționare efectivă a puțurilor datorită reducerii semnificative a formațiunilor apă-gaz-con;
poluarea minimă a mediului și conservarea unor suprafețe mari prietenoase cu mediul la suprafață;
reducerea numărului de puțuri necesare pentru dezvoltarea și dezvoltarea suplimentară a zăcămintelor;
implicarea în exploatarea unor domenii care anterior erau considerate neprofitabile din punct de vedere industrial (în afara bilanţului).
Unele limitări sunt cauzate de stadiul actual al tehnicii și tehnologiei pentru forarea puțurilor orizontale, precum și de numărul nerezolvat de probleme de planificare, finanțare, stimulente și organizare a muncii.
Primul puț orizontal, care trece direct 130 m printr-o cusătură cu o grosime de aproximativ 30 m, a fost realizat în 1957 la câmpul Yablonovskoye din regiunea Kuibyshev. În ciuda faptului că puțul a fost forat într-o formațiune puternic drenată, debitul său zilnic a fost de 40 de tone, ceea ce era de multe ori mai mare decât debitul puțurilor verticale.
În VNIIBT, ca urmare a lucrărilor de foraj multilateral și orizontal, în primii ani au fost dezvoltate turboforatoare speciale scurtate T12M2K, în care pentru prima dată a fost folosit un talon de curgere, tehnologia de lovire fără erori în foraje suplimentare a fost dezvoltat, a fost dezvoltat un sistem de livrare a instrumentelor geofizice în forajele orizontale, care este utilizat cu unele modificări față de prezent atât în Federația Rusă, cât și în străinătate (sistemul Simfor).
Specialiștii VNIIBT au dezvoltat mijloace și metode tehnice care fac posibilă găurirea fiabilă a arborilor orizontale într-o direcție dată.
Atunci când se utilizează burghie electrice ca motor de foraj, setul disponibil de mijloace tehnice disponibile în comerț face posibilă efectuarea unei curburi intense a sondei pe o rază de 120 m sau mai mult și efectuarea de foraje orizontale cu control constant asupra parametrilor spațiali ai puțului. sondă.
Experiența acumulată arată că bormașina electrică este instrument eficient fântâni orizontale și trebuie utilizat acolo unde se dezvoltă baza forajului electric.
Majoritatea puțurilor orizontale din țară sunt forate cu motoare hidraulice de fund. Principala direcție de lucru în acest domeniu în ultimii ani a fost crearea de mijloace tehnice și dezvoltarea tehnologiei pentru forarea puțurilor orizontale cu abateri minime de la traiectoria calculată.
VNIIBT a creat eșantioane prototip ale complexului hardware Horizon-1 (Fig. 1.3), inclusiv un deflector bazat pe un motor cu deplasare pozitivă scurtat în fond de foră, cu un diametru de 172 mm și instrumente speciale pentru livrarea instrumentelor geofizice la sondă în general.
Orez. 1.3. Complex de mijloace tehnice „Orizont-1”: 1, 2 - țevi de foraj; 3 - dalta; 4 – cablu geofizic; 5 - dispozitiv pentru deplasarea instrumentelor geofizice; 6 - articulatie pivotanta; 7 - motor
unghiurile de înclinare ale trunchiului (Fig. 1.4). Conform rezultatelor lucrărilor de teren, proiectarea barei de foraj a fost îmbunătățită și a fost creat șurubul universal OSH-172 (Fig. 1.5), care este utilizat atât la devierea sondei, cât și la forarea secțiunilor orizontale ale sondei, care este realizat prin înlocuirea pieselor înlocuibile ale whipstock-ului sub atelier mecanic sau instalație de foraj. Este prevăzută raza de curbură a sondei cu un bit de 275,9 mm, egală cu 40 m sau mai mult.
A fost dezvoltată tehnologia de atingere a direcției orizontale și de forare a unui sondă orizontală de 150–200 m lungime cu o abatere de la marcajul vertical în 4 m. Acest lucru necesită un grad ridicat de coincidență a intensității calculate și reale a curburii sondei atunci când se lucrează. cu whipstock OSH-172, monitorizarea continuă a poziției whipstock-ului folosind un dispozitiv cu linie de cablu conexiuni, utilizarea unor ansambluri articulate speciale la forarea unui sondă orizontală, precum și măsurători clinometrice periodice. Carcasa sondei este realizată cu o carcasă de producție cu un diametru de 140–146 mm, echipată în zona de producție cu un filtru de același diametru. Snurul de producție este cimentat deasupra pantofului șnurului intermediar de 245 mm folosind un pacher PDM-140 (PDM-146). Studiile geofizice ale sondei orizontale sunt efectuate folosind metode de radiație.
Pe măsură ce adâncimile cresc, eficiența forajului orizontal crește brusc, dar cresc și dificultățile asociate cu controlul sondei, pentru a elimina care este necesar să se creeze un instrument special și metode de management operațional.
În practica străină, această metodă și, cel mai important, nodul pentru controlul, colectarea informațiilor și reglarea sondei și, în plus, țevi speciale și alte instrumente, au fost dezvoltate în mai multe versiuni și asigură forarea puțului printr-un rezervor cu o grosime de doar cativa metri. Sistemul de măsurare a forajului permite efectuarea automată a procesului.
Foraj în zone de apă. Organizarea forajului, lucrările pregătitoare pentru foraj, echipamentele capului de sondă și alte lucrări pe mare au propriile lor caracteristici.
Până la 17% din petrolul consumat în lume este extras din mare. Potrivit experților, există perspective mari pentru producția de petrol și gaze pe rafturile CSI, SUA și alte țări.
În prezent, se desfășoară mai multe tipuri de lucrări organizatorice și pregătitoare, în urma cărora se creează un loc pentru instalarea echipamentelor de foraj:
construirea de structuri artificiale sub formă de baraje și pasaje supraterane care separă o parte a zonei de apă cu rambleul ulterioar (în diverse moduri și materiale);
Orez. 1.4. Dispozitiv de călătorie Fig. 1.5. Deflector universal
instrumente de înregistrare: OSH-172:
1 – corpul aparatului; 2 - mecanism cu role; 1 - secțiunea superioară a turboburătorului (inferioară; 3 - fereastră pentru spălare; 4 - etanșare arbore); 2 – secțiunea inferioară a turboforghiului (top-wireline; 5 – ferestre pentru arborele forestier); 3 - deflector cablu articulat
aluviuni și întărirea insulelor individuale;
construirea de pasaje supraterane cu amplasarea de sate întregi pe acestea;
construirea de platforme submersibile, semisubmersibile și alte tipuri;
utilizarea de nave speciale cu dispozitive ancorate;
înghețarea pe învelișuri de gheață dintr-un strat gros de gheață durabil etc.
Pe aceste insule sau fundații artificiale se montează echipamente de foraj pentru forarea puțurilor de diferite adâncimi și scopuri. Având în vedere costul semnificativ al structurilor artificiale, se efectuează foraje în cluster. Tipul de fundație este determinat de adâncimea mării și natura modificării acesteia, condițiile meteorologice, adâncimea obiectului productiv etc. La forarea puțurilor în larg, condițiile meteorologice (în special în mările nordice) și adâncimea marea joacă un rol important.
CSI este un pionier în producția offshore de petrol și gaze. Deja în anii 40, producția de petrol și gaze a început pe raftul Mării Caspice din artificial-22
ny insule în vrac. Astăzi, pe Marea Caspică a fost construit un întreg oraș. Lungimea pasajelor a ajuns la 350 km, iar numărul platformelor staționare care stau separat în mare este mai mare de 250.
Lucrările lui Rustambekov (1935) ar trebui considerate prima lucrare științifică și de inginerie în foraj și producție de petrol în mare.
Foraj offshore în zona de cca. Artem (Azerbaidjan) a devenit posibilă după implementarea conform metodei N.S. Timofeev lucrează la instalarea și cimentarea piloților metalici tubulari în locul celor din lemn, care nu puteau fi înglobați într-un fund solid de var. Metoda a fost să forați găuri adânci de câțiva metri, să le introduceți tevi metalice apoi pompați mortarul de ciment în țevi și ridicați-l în inelul gropii. N.S. Timofeev a sugerat forarea puțurilor înclinate de la baze.
Mai târziu B.A. Raginsky a propus un sistem de fundație cu piloți cu blocuri mari, lucrările de achiziție și sudare pentru care au fost efectuate pe uscat; pe mare s-a efectuat doar instalarea structurilor. Aceste modele au devenit larg răspândite în Azerbaidjan și Daghestan.
O mare contribuție la dezvoltarea construcției de sonde în condiții offshore a avut-o L.A. Mezhlumov, S.M. Kuliev, Yu.A. Safarov, R.I. Shishchenko, S.A. Orudjev, A.A. Movsumov, I.I. Kuliev, R.K. Seid-Rza, M.P. Gulizade.
Dezvoltarea resurselor marine în b. URSS a început cu umplerea golfului Bibi-Heybat și forarea ulterioară din zona umplută. Începând cu anii 40, dezvoltarea mării a început folosind piloți și fundații metalice la o adâncime a mării de 4 până la 10 m. Pentru prima dată, forarea de pe nave în b. URSS a început în 1935 în Azerbaidjan în scopuri de cartografiere structurală și pentru studiul caracteristicilor inginerie-geologice ale solurilor marine (adâncimea mării până la 25 m, adâncimea forajului până la 100 m). Experiența forajului de pe nave ușoare în Marea Caspică a arătat că atunci când marea este mai mare de 2-3 puncte și puterea vântului este peste 4 puncte, munca este dificilă sau imposibilă.
Din 1978, platformele de foraj staționare au fost puse în funcțiune la o adâncime a apei de 110–120 m.
Ulterior, în locul platformelor fixe, practic în toate zonele de apă, se folosesc FDR-uri - instalații de foraj plutitoare (Sivash, Okha, Khakuri, Shelf, Kaspmoreneft etc.). În Marea Barents din 1981 au început forajele de explorare de la navele de foraj. Primele astfel de nave au fost „Valentin Shashin”, „Viktor Muravlenko” și „Mikhail Mirchink”.
În practica mondială a operațiunilor de foraj pe mare, s-au determinat direcții în domeniul creării PVS, care iau în considerare factori precum adâncimea mării, starea solului, condițiile de gheață, scopul forajului etc.
În prezent, instalațiile de foraj plutitoare sunt clasificate în funcție de modul în care sunt instalate deasupra puțului în timpul forajului, distingându-se două grupe (clase) principale: cele bazate pe fundul mării în timpul forajului și forarea în stare flotantă.
Prima grupă include instalații de foraj plutitoare de tip jack-up și submersibile (SPBU), iar a doua grupă include instalații de foraj semi-submersibile (SSDR) și nave de foraj (BS).
Instalațiile de ridicare cu cric sunt utilizate în principal în forajele de explorare la zăcămintele offshore și de petrol și gaze în zone de apă cu adâncimi de apă de 30-120 m.
T a b l e 1.3
Scurte caracteristici tehnice ale PBU
Tip nave de forat
„1-NS”, „Valentin
Tip PBU „Raft”,
Indicatori
Shashin", „Victor
"Raft-4",
Skye"
Muravlenko"
"Raft-8"
Tipul de vas (instalare)
Nava diesel-electrică
Semi-submersibil
auto-elevator non-
Mohodnaya
autopropulsat
Adâncimea mării, m
60-300
90-200
20-100
Adâncimea maximă bu-
6500
6000
6500
Autonomia de funcționare
100
30
30
Derrick:
tip
VBP53-320
VBP53-320
VBP54-320
capacitatea de ridicare la
320
320
320
snap 6x7, t
înălțime utilă (de la
53
53
54
la rig la partea de jos sub-
coroană bloc grindă), m
inaltime totala, m
57,2
57,2
58,5
masa, t
180,5
180,5
134,1
tip
Oilwell E-3000
LBU-2000P
Oilwell E-3000
sarcina nominala
600
320
600
capacitate, t
tensiune de rulare
414
341
414
capătul cablului de sârmă
la sarcina nominală
capacitate de ridicare, kN
diametrul canalului de deplasare
38
35
38
diametrul tamburului, mm
893
835
893
lungime tambur, mm
1575
1445
1575
numărul de viteze
4
4
4
frecventa medie
I–58; II-108;
I–83; II-97;
I–58; II-108;
arborele de ridicare le-
III–191; IV-351
III–133; IV-264
III-191; IV-351
paturi, rpm
Sistemul de plasare în-
ASP
KMSP
ASP
instrument
Lungimea suporturilor de foraj, m
27
27
27
sunt remorcate împreună cu echipamente, unelte și materiale până la punctul de foraj. La remorcare, suporturile sunt ridicate, iar la punctul de foraj, suporturile sunt coborâte în jos și presate în pământ, carena se ridică de-a lungul suporturilor și se fixează la înălțimea calculată deasupra nivelului mării.
SPBU tip submersibil folosit în principal în ape de mică adâncime. Ca urmare a umplerii cu apă a clădirilor inferioare ale instalației, acestea se scufundă pe fundul mării. Platforma de lucru este deasupra suprafeței apei.
SSDR este utilizat în principal pentru forarea puțurilor de prospectare și explorare în zone de apă la adâncimi mari de la 100 la 300 m sau mai mult.
BS au manevrabilitate mare și viteză de mișcare, autonomie mai mare în comparație cu SSDR și, prin urmare, sunt utilizate pentru forarea puțurilor de prospectare și explorare în zone îndepărtate la adâncimi mari de 1500 m sau mai mult.
Principalele stări ale PBS depind de clasă și scop: transferul într-un punct nou, instalarea la punctul de foraj, forarea și îndepărtarea din forajul finalizat al sondei.
Există două tipuri de remorcare cu cric: scurtă (tranziție) de la un punct la altul în cadrul structurii explorate și remorcare pe termen lung pe distanțe lungi în afara zonei explorate.
MODU este distilat și remorcat cu restricții din cauza condițiilor meteorologice. La finalizarea transportului, SSDR este direcționat către punctul de foraj și, în conformitate cu schema, ancorele și lanțurile de ancorare sunt transportate.
Principalele caracteristici tehnice ale unor PBU sunt prezentate în tabel. 1.3.
Funcțiile de foraj în condiții offshore și onshore sunt echivalente. Cu toate acestea, există o serie de diferențe, care sunt legate în principal de proiectarea părții superioare (submarine) a puțurilor, forarea din foraje de sondă, echiparea capului sondei cu dispozitive de prevenire a erupțiilor, conservarea puțurilor etc.
Înainte de forare, un puț este justificat și este selectat designul său. Conceptul de proiectare include un aranjament concentric al șirurilor de tubaj coborâte în puț, cu indicarea diametrelor acestora, adâncimea de coborâre, înălțimea nămolului de ciment pompat în puț după ele, diametrul biților care sunt forați sub fiecare coloană. .
Strict vorbind, proiectarea unei sonde este un ansamblu de elemente ale unui suport de lucru minier cu dimensiuni transversale disproporționat de mici cu adâncimea și lungimea sa, care, cu echipamente tehnice și tehnologice moderne, asigură lipsa de accidente, ținând cont de protecția a subsolului, construcția economică a unui canal ermetic stabil spațial între formațiunile saturate de fluid și restul secțiunii geologice expuse, precum și suprafața de zi, care se operează în modurile și timpul dat în funcție de scop (studiu de secția geologică, explorarea și evaluarea capacității portante de gaze și petrol a zăcămintelor, producerea produselor, menținerea presiunilor de rezervor, monitorizarea modului de funcționare a câmpului etc.). Pe fig. 1.6, este prezentat un profil de sondă, iar în fig. 1.6, b prezintă grafic schema de lucru a proiectării sale. Deasupra fiecărui rând de șiruri de carcasă, este dat diametrul lor (în mm), iar dedesubt - adâncimea de instalare (în m) și creșterea suspensiei de ciment sunt indicate prin lovituri, deasupra cărora este marcată înălțimea ridicării acestuia; uneori este dat numărul de biți.
Fiecare șir coborât în fântână are propriul nume. Prima, cea mai scurtă, se numește direcția. Este instalat înainte de foraj și protejează capul sondei de eroziunea solului prin circulația noroiului de foraj. A doua coloană, care servește la acoperirea stâncilor superioare instabile și acvifere, se numește conductor. Fundul conductorului, ca și fundul tuturor coloanelor coborâte după el, se termină cu o țeavă scurtă îngroșată numită pantof. Când forați puțuri în condiții de permafrost,
Orez. 1.6. Bine design
placa si conductorul se selecteaza tinand cont de prevenirea dezghetarii rocilor. Pentru a preveni sau elimina complicațiile apărute sau posibile în timpul forajului, se coboară un șir intermediar. Pot fi mai multe. Ultima coloană destinată exploatării orizontului productiv se numește șir de producție. La calcularea numărului de șiruri coborâte în puț, direcția și conductorul nu sunt luate în considerare.
Un șir care se întinde pe un anumit interval fără acces la capul sondei se numește liner (șir secret). Garniturile sunt adesea folosite la fixarea puțurilor adânci (Fig. 1.7).
Uneori, șirurile de carcasă sunt coborâte în părți - secțiuni. Procesul de coborâre a șnurului de carcasă în acest caz se numește secțional, iar șnurul se numește secțional.
La forarea puțurilor adânci în condiții geologice dificile, se folosesc structuri cu mai multe coloane. Destul de des, ieșirea bitului de sub coloanele intermediare ajunge la 1500 m sau mai mult. În aceste condiții, se efectuează o cantitate mare de lucrări de foraj într-un puț cu carcasă, tuburile de tub și de foraj se uzează semnificativ, iar durata lor de viață scade. Inelele de uzură sunt folosite pentru a reduce uzura. Protectorul (Fig. 1.8) constă din două carcase de cauciuc interschimbabile 2, întărite cu un cadru metalic, conectate între ele folosind știfturi de legătură 1. O garnitură flexibilă 3 este fixată în interiorul cadrului, ale cărei margini sunt înfășurate spre interior. Cadrul metalic 4 este acoperit la suprafață cu adeziv special în timpul cauciucării. Designul protectorului asigură autoblocarea acestuia pe țeava de foraj. Protecțiile se instalează cu ușurință pe țeava de foraj atât deasupra rotorului în timpul operațiunilor de declanșare, cât și pe puntea de foraj.
Protectorul cu diametrul de 114 mm se instaleaza pe orice sectiune a conductei si se autobloca atunci cand protectorul se misca in sus si in jos pe garnitura de foraj; protectorul cu diametrul de 140 mm este instalat sub încuietoarea țevii de foraj și se autoblochează atunci când protectorul se mișcă în sus de-a lungul șirului de foraj.
Pentru cimentarea uleiului și puţuri de gaze se folosește mortar de ciment - un amestec de lianți (cimenturi) amestecați cu o anumită cantitate de apă, adesea cu adaos de reactivi chimici. Datorită faptului că au apărut soluții, a căror fază solidă este reprezentată nu doar de cimentul Portland (și uneori nu îl include pe acesta din urmă), este mai corect să le numim șlamuri de ciment. Nămolurile de chituire pot primi o formulare mai generală: aceasta este o soluție obținută după amestecarea cimentului cu apă (sau alt lichid) tratată cu aditivi chimici (sau fără aceștia)
527 425 295 219 146
Orez. 1.7. Design bine cu căptușeală de 219 mm
Orez. 1.8. Protector cu autoblocare:
a - pentru țevi de foraj cu diametrul de 114 mm; b - pentru tevi de foraj cu diametrul de 140 mm
pentru a îmbunătăți calitatea mortarului și a pietrei sau pentru a facilita procesul.
Cimentul de puț este un produs format din unul sau mai mulți lianți (ciment Portland, zgură, var, materiale organice etc.), minerali (nisip de cuarț, azbest, argilă, zgură etc.) sau organici (linters de bumbac, deșeuri de producție de celuloză etc.). .) aditivi care permit, după amestecarea cu apă sau alt lichid, să se obțină o soluție, iar apoi o piatră de calitate condiționată.
Succesul operațiunilor de cimentare este determinat de tehnica și tehnologia proceselor de cimentare, de calitatea lucrărilor pregătitoare, de materialul de rambleu și de caracterul complet al înlocuirii fluidului de foraj cu rambleu.
Există mai multe moduri de găurire, dar găurirea mecanică și-a găsit aplicație industrială. Forajul mecanic este împărțit în percuţieȘi rotativ.
În găurirea cu percuție (Fig. 31), unealta de foraj constă dintr-un bit 1, o tijă de șoc 2, un dispozitiv de blocare a cablului 3. Pe puțul de foraj este instalat un catarg 12, care are un bloc 5 în partea superioară, o tragere. rolă a balansierului 6, o rolă auxiliară 8 și un tambur al mașinii de găurit 11. Coarda este înfășurată pe tamburul 11 al mașinii de găurit. Instrumentul de foraj este suspendat pe o frânghie 4, care este aruncată peste blocul 5 al catargului 12. Când roțile dințate 10 se rotesc, biela 9, alternativ, ridică și coboară cadrul de echilibrare 6. Când cadrul este coborât, rola de tragere 7 trage frânghia și ridică instrumentul de foraj deasupra fundului puțului . Când cadrul este ridicat, frânghia este coborâtă, bitul cade pe față Fig. 31. Schema de șoc-frânghie și distruge stânca. Cilindricitatea celui de-al --lea foraj al sondei este asigurată prin rotirea burghiului
atunci când se ridică deasupra găurii de fund, datorită dezvoltării în timpul ridicării și răsucirii în timpul impactului bitului asupra stâncii. Pentru a curăța fundul de roca distrusă (nămol), se ridică o instalație de foraj
se coboară o unealtă din fântână și se coboară în el (un cilindru de tip găleată alungită cu o supapă în partea de jos). Când dispozitivul de evacuare este scufundat într-un amestec constând din rocă distrusă și lichid, supapa de la baler se deschide și dispozitivul de evacuare este umplut cu acest amestec, apoi se ridică. Când se ridică boilerul, supapa din partea inferioară se închide și amestecul se ridică la suprafață. Bailer-ul este coborât în puț până când gaura de fund este complet curățată de roca forată. După curățarea găurii de fund de butași, instrumentul de foraj este din nou coborât în puț și forarea puțului continuă. Pentru a preveni prăbușirea pereților puțului în timpul forajului, în el este coborât un șir de tubulare, constând din țevi metalice de carcasa conectate între ele prin filetare sau sudură. În procesul de adâncire a puțului, conducta de tubaj este construită și coborâtă, astfel încât procesul de foraj continuă până când șirul de tubaj devine imposibil de coborât. În acest caz, puțul este adâncit cu un pic de diametru mai mic, coborât prin prima șiră de tubaj. Și poate veni un moment în care al 2-lea sau al 3-lea șir de tubaj nu este coborât, apoi un alt diametru, mai mic, etc., este coborât până când se ajunge la adâncimea de proiectare a puțului. Metoda de foraj cu impact este utilizată la adâncimi mici la forarea puțurilor de apă, în industria cărbunelui și minier etc. În prezent, metoda impactului pentru forarea puțurilor de petrol și gaze nu este utilizată.
Performanța găuririi cu percuție depinde în mare măsură de alegerea potrivita pentru un bit de tip rocă dat. Pentru găurirea rocilor moi și medii dure, se folosesc biți I (Fig. 32). Au o lamă largă și relativ subțire, cu o suprafață laterală în formă de I a lamei de daltă (Fig. 32). A). Pentru găurirea în roci dure, se folosesc dalte grele (Fig. 32 b). La foraj în roci dure fracturate se folosesc bucăți încrucișați (Fig. 32 c).
O creștere a înălțimii căderii sculei duce la o creștere a eficienței impactului, dar în acest caz numărul de impacturi pe unitatea de timp scade. Practica a arătat că lungimea optimă a cursei rolei de retragere este de 350-1000 mm, iar numărul de curse pe minut este de 40-50.
Orez. 32. Bite pentru gaurire cu impact: 1 - lama; 2 - gat; 3 - cap filetat; 4 - lama; 5 - fir; A- unghiul vârfului lamei
Pentru a crește eficiența forării cu percuție, este necesar să curățați imediat fundul puțului de tăieturi de foraj.
Foraj rotativ. Sondele de petrol și gaze sunt forate în prezent folosind metoda de foraj rotativ. În forajul rotativ, distrugerea rocii are loc datorită burghiului rotativ. Sub greutatea sculei, bitul intră în rocă și, sub influența cuplului, distruge roca. Cuplul este transmis bitului prin intermediul unui rotor montat pe capul sondei prin garnitura de foraj. Această metodă de găurire se numește găurire rotativă. Dacă cuplul este transmis burghiului de la un motor de foraj (turboburghiu, burghiu electric), atunci această metodă se numește foraj cu turbină.
Turbodrill - este o turbină hidraulică antrenată de un fluid de foraj pompat în puț de pompe.
Bormasina electrica este un motor etanș electricitate este alimentat prin cablu de la suprafata.
Forarea puțurilor se realizează cu ajutorul unei instalații de foraj (Fig. 33).
Distrugerea rocilor se realizeaza cu ajutorul unui burit (1) coborat pe tevi de foraj (20) pana in jos. Mișcarea de rotație a burghiului este transmisă de un motor de foraj (22) sau de un rotor (13) prin garnitura de foraj (foraj rotativ). Rotorul este montat pe capul sondei. Garnitura de țevi de foraj constă dintr-o secțiune pătrată kelly (11) (numită pătrat în practică) și țevi de foraj (20) conectate la acesta printr-un sub (19). Coarda de țevi de foraj trece prin rotor și este atârnată de cârligul (9) al instalației de foraj. Mișcarea de rotație a șirului țevii de foraj cu burghiul se realizează prin rotor (Fig. 41). Rotor reprezintă angrenaj conic lanț acționat de motor diesel sau electric. În cavitatea interioară a patului (1) al rotorului, pe un rulment este montată o masă (2) cu roată conică, care se cuplează cu o roată conică montată pe arborele (6). La celălalt capăt al arborelui este montată o roată de lanț (neprezentată în figură), prin care se transmite rotația mesei de la motor. Masa rotorului are o gaură în centru, al cărei diametru depinde de dimensiunea maximă a burghiului care este trecut prin ea la coborârea sau ridicarea garniturii de foraj. După coborârea țevilor de foraj cu un burghiu, în orificiul mesei rotorului sunt introduse două inserții (4) și în interiorul lor sunt introduse două cleme (3), care formează o gaură cu secțiune pătrată. În această gaură se află o conductă de conducere, tot de secțiune pătrată.
Acesta percepe cuplul de pe masa rotorului și se mișcă liber de-a lungul axei rotorului. Masa rotativă este protejată de o carcasă (5). Împiedică și ținere
Orez. 33. Instalatie pentru forarea unui put
asupra greutății șirurilor de țevi de foraj se realizează printr-un mecanism de ridicare. Mecanismul de ridicare constă dintr-un dispozitiv de tracțiune 4 (vezi fig. 33), un motor electric sau diesel (acționare) (5), un sistem de echipare (7), un bloc de mișcare (8), un bloc coroană (bloc superior), un pivotant (6) și cârlig (9). Un bascul de foraj (12) servește drept cadru pentru palanul mecanismului de ridicare. Pentru a reduce forța asupra cablului de oțel (7) al sistemului de deplasare, se utilizează un sistem de ridicare cu lanț.
Polyspast - este un sistem de blocuri mobile și fixe prin care se trece o frânghie de oțel. Un capăt al frânghiei este fixat la capul sondei, în timp ce celălalt capăt este înfășurat pe tamburul troliului (frânghie de rulare). Pe partea superioară de susținere a instalației de foraj este instalat un bloc de role fixe, care se numește blocul coroanei(Fig. 34).
Orez. 34. Bloc coroana: 1 - scripete; 2 - axa; 3 - cadru; 4 - capac de siguranta; 5 - scripete auxiliare
Blocul în mișcare este numit abordat bloc (Fig. 35). Cel mai adesea, blocul de coroană este format din șase role cu caneluri pentru cablul de sârmă, iar blocul de călătorie este format din cinci role cu caneluri. În acest fel, puțul ajunge la suprafață, unde intră în sistem prin jgheaburi (14) facilitati de tratament. În sistemul instalațiilor de tratare, fluidul de foraj este curățat de particule de rocă, reintră în rezervorul de recepție (18), iar procesul de foraj continuă.
Cu metoda de forare cu turbină, fluidul de foraj este fluidul de lucru pentru antrenarea motorului hidraulic de foraj - turboforator.
Fluidul de foraj îndeplinește o serie de funcții importante atunci când forează un puț. Cu circulație constantă în timpul forajului, fluidul de foraj răcește conurile burghiului, aduce particulele de rocă distrusă de la fundul puțului la suprafață, previne posibilele emisii de petrol și gaze în timpul procesului de foraj și previne prăbușirea și distrugerea pereților. a sondei în timpul forajului. Pentru fiecare câmp, în funcție de condițiile miniere și geologice, structura și compoziția rocilor, presiunea lacului de acumulare etc. se prepară fluidul de foraj corespunzător. Formularea și compoziția fluidului de foraj trebuie specificate în proiectul tehnic pentru forarea sondei. Fluidul de foraj trebuie să fie suficient de mobil, să rețină bine particulele de rocă distrusă, să nu fie filtrat în roci etc. Practic, ca fluid de foraj se folosește o soluție de noroi, care se prepară după o rețetă specială, adică. o soluție de argilă în apă cu aditivi corespunzători. Uneori se folosesc soluții pe bază de ulei.
În timpul forajului, când kellyul (pătratul) intră în soluție pe toată lungimea sa, unealta de foraj este ridicată din puț pe lungimea pătratului cu ajutorul unui troliu și suspendată cu un lift sau pene pe arborele rotorului.Țeava de conducere (pătrată) se deșurubează împreună cu pivotul și se coboară în țeava de carcasă instalată în prealabil într-un puț înclinat, numit groapă. Lungimea gropii trebuie să fie egală cu lungimea conductei de conducere. Groapa este forată înainte de începerea forării puțului din colțul din dreapta al forței. Apoi garnitura de foraj este construită prin înșurubarea unei două țevi pe ea (două înșurubate între carcasă, forța asupra funiei de rulare va fi de zece ori mai mică decât greutatea reală a garniturii de foraj ridicată.
În timpul procesului de foraj, este necesar să rotiți șirul țevii de foraj cu un pic și, în același timp, să introduceți fluid de foraj în aceste țevi pentru a efectua roca forată. În acest scop, între cârligul (9) și pătratul (11) este montat (suspendat) un dispozitiv special care se numește pivotant(6). Pentru a aduce roca distrusă în gaura de jos la suprafață, răciți burghia, acționați motoare de fond (turboforatoare) într-un puț de foraj, circulă constant argilos soluţie. Nămolul de foraj, pregătit la suprafață, este preluat din rezervor (18) de o pompă de foraj cu piston (16) cu un motor (17) și prin conducta de injecție (15) printr-un furtun flexibil special de înaltă presiune (10) sub presiunea este introdusă printr-un pivot în țevile de foraj.
Rotire constă dintr-un corp gol, în interiorul căruia se află o platformă de sprijin orizontală cu un rulment axial, pe care se sprijină partea rotativă - rotorul, de care se atașează șirul țevii de foraj cu ajutorul racordurilor filetate. În partea superioară a corpului pivotului, fluidul de foraj este pompat prin duză, care trece prin rotorul tubular în garnitura de foraj. Ieșind prin orificiile bitului, fluidul de foraj, amestecându-se cu particulele de rocă distrusă, se ridică prin inelare.
Orez. 35. Bloc de deplasare: 1 - traversare; 2 - scripete; 3 - axa; 4 - huse de siguranță; 5 - obraji; 6 - cercel
țevi de foraj), scoateți-l din lift sau pene, coborâți-l în puț până la lungimea unei două țevi, agățați-l cu elevatoare sau pene pe masa rotorului, ridicați kellyul cu un pivot din gaură, înșurubați-l la garnitura de foraj, eliberați garnitura de foraj din pene sau elevator, coborâți burghia la fundul gaurii și forarea puțului continuă.
Pentru a înlocui un burghiu uzat cu altul, se ridică unealta de foraj, se înlocuiește burghiul, se coboară unealta cu burghiu și se continuă forarea puțului. Când tamburul troliului se rotește, frânghia de deplasare este înfășurată sau desfășurată din tambur și, din această cauză, blocul de deplasare cu cârligul este ridicat sau coborât. La cârlig, cu ajutorul chingilor și a unui lift, se suspendă un șir de foraj care urmează să fie ridicat sau coborât. La ridicare, instrumentul de foraj este înșurubat în secțiuni, care sunt numite lumanari,și așezat în felinarul turnului pe un sfeșnic. Secțiunile, sau lumânările, au o lungime în funcție de înălțimea instalației de foraj. Deci, cu o înălțime a turnului de 41 de metri, lungimea lumânărilor este de 25-36 de metri. Coborârea instrumentului de foraj (snur de foraj) în puț se efectuează în ordine inversă. Instalație de foraj - aceasta este o structură metalică deasupra puțului pentru coborârea și recuperarea unei unealte de foraj cu un burghiu, motoare de fund, țevi de tubaj, plasarea suporturilor de foraj după ce sunt scoase din puț etc.
Eliberarea turnurilor turn(Fig. 36) și catarg(Fig. 37).
Turnul turn BM-41 (Fig. 37) este o piramidă metalică tetraedrică trunchiată obișnuită. Este alcătuit din patru picioare (1), o poartă (2), un balcon (3) al lucrătorului superior (călărit), o platformă bloc coroană (4), capre (5), curele transversale (6), cuple (7). ) și o scară de zbor (8 ).
Turnurile de catarg sunt produse cu un singur suport și cu două suporturi în formă de A. Cele mai utilizate turnuri în formă de A.
Turnul catargului în formă de A (Fig. 37) constă dintr-un suport de ridicare (1), secțiuni de catarg (2,3,4,6), o scăpare de incendiu (5), montaj capre (7), un cadru bloc coroană ( 8), vergeturi (9,10,14), băieți (11), scări de tunel (12), balcon (13)
Orez. 36. Turnul VM-41: 1 - picior; 2 - poarta; 3 - balcon; 4 - platforma bloc subcorona; 5 - montare capre; 6 - curele transversale; 7 - cuple; 8 - scările de marș
Orez. 37. Turn catarg tip A: 1 - suport de ridicare; 2, 3, 4, 6 - secțiuni de catarg; 5 - evacuare de incendiu; 7 - montaj capre pentru repararea blocului coroanei; 8 - cadru bloc sub-coroană; 9, 10, 14 - vergeturi; 11 - bretele; 12 - scari de tunel; 13 - balcon; 15 - centura de siguranta; 16 - scari la mijlocul zborului; 17 - balama
de lucru, centură de siguranță (15), scări la mijlocul zborului (16), balama (17).
Turnurile sunt produse în mai multe modificări. Principalele caracteristici ale mașinii de foraj sunt capacitatea de transport, înălțimea, capacitatea „magazinelor” (un loc pentru standurile pentru țevi de foraj), dimensiunile bazelor inferioare și superioare și greutatea (masa turnului).
Capacitatea de ridicare a forei este sarcina maximă, maximă admisă pe foră în procesul de forare a unui puț. Înălțimea turnului determină lungimea lumânării care poate fi scoasă din puț, a cărei dimensiune determină durata operațiunilor de declanșare.
Pentru forarea puțurilor la o adâncime de 400-600 m, se folosește un derrick de 16-18 m înălțime, la o adâncime de 2000-3000 m - o înălțime de 42 m și la o adâncime de la 4000 la 6500 m - 53 m.
Capacitatea „magazinului” arată ce lungime totală a țevilor de foraj cu diametrul de 114-168 mm poate fi plasată în ele. Dimensiunile bazelor superioare și inferioare caracterizează condițiile echipajului de foraj, ținând cont de amplasarea echipamentelor de foraj, a sculelor de foraj și a mijloacelor de mecanizare a operațiunilor de declanșare. Dimensiunile bazei superioare a turnurilor sunt 2x2 sau 2,6x2,6 m, iar cele inferioare 8x8 sau 10x10 m.
Masa totală a instalațiilor de foraj este de zeci de tone.
Pentru mecanizarea operațiunilor de declanșare se utilizează un sistem de deplasare și o tragere. Sistemul de deplasare constă dintr-un bloc de coroană staționar (Fig. 34), care este instalat în partea superioară a instalației de foraj, un bloc de călătorie (Fig. 35), conectat la blocul de coroană cu o frânghie de călătorie, al cărui capăt este atașat de tamburul troliului, iar celălalt capăt este fixat fix la cârligul de foraj. Sistemul de fixare este un palan cu lanț (sistem bloc) conceput pentru a reduce tensiunea cablului de fixare și pentru a reduce viteza de coborâre a instrumentului de foraj, a carcasei și a țevilor de foraj.
O unealtă de foraj este suspendată de cârlig: la găurire, cu ajutorul unui pivot, și în timpul operațiunilor de declanșare, cu ajutorul chingilor și a unui elevator (Fig. 38). Desenul este folosit pentru:
"*%" 1) țineți greutatea instrumentului de găurit; *" " 2) coborârea și ridicarea țevilor de foraj și tubaj.
Orez. 38. Schema suspendării țevii de foraj în timpul operațiunilor de declanșare: A - sistem; b - lift: 1 - teava de foraj; 2 - lift; 3 - link
Instalația de foraj este echipată cu un dispozitiv de tracțiune de o anumită capacitate. Pentru mecanizarea înșurubarii și deșurubarii rosturilor de scule ale țevilor de foraj se folosesc clești de foraj automat AKB-ZM și clești de suspendare PKB-1, mâner pneumatic cu pană PKR-560 pentru prinderea și eliberarea mecanizată a țevilor de foraj. Cheia AKB-ZM (Fig. 39) este instalată între troliu și rotorul 4 pe fundație.
Principalele părți ale cheii sunt blocul de chei 1, căruciorul cu cilindri pneumatici 2, suportul 3 și panoul de comandă 4.
Înșurubarea și deșurubarea țevilor de foraj se efectuează cu ajutorul unui bloc cheie montat pe un cărucior, care se deplasează cu ajutorul a doi cilindri pneumatici de-a lungul ghidajelor: fie spre țeava de foraj instalată în rotor, fie departe de aceasta. Dispozitivele de prindere, precum și mecanismul de deplasare a blocului de chei, sunt alimentate de cilindri pneumatici activați de la panoul de comandă 4. În acest scop, aer comprimat este furnizat sistemului de la receptor.
Orez. 39. Cheie de gaurire AKB-ZM: 1 - bloc de chei; 2 - cărucior cu cilindri pneumatici; 3 - rack; 4 - panou de control
Recent, au fost produse chei AKB-ZM2, al căror design se bazează pe chei AKB-ZM. Pe baza cleștelui de foraj AKB-ZM2, cleștele AKB-ZM2-E2 cu o acționare electrică cu două fețe a rotatorului a fost dezvoltat și produs în serie la uzina Izhneftemash (Izhevsk).
Caracteristică | AKB-ZM2 | AKB-ZM2-E2 |
Diametrul nominal al țevilor înșurubate (deșurubate), mm: carcasă de găurire | 108-216 114-194 | 108-216 114-194 |
Acționare rotativă | motor pneumatic | e-mail motor |
Frecvența de rotație a dispozitivului de prindere a țevii, rpm: la prima turație la a doua turație | 60-105 | |
Cuplu de aprovizionare (kNm): la prima turație, nu mai puțin de: la a doua turație, nu mai puțin de: maxim (cu două sau trei reatașări) | 1,2 30 | 1,25 2,5 |
Putere de antrenare, kW | 15/7,5 | |
Presiunea aerului în rețea, MPa | 0,7-0,9 | 0,7-0,9 |
Dimensiuni totale, mm Bloc cheie cu cărucior și coloană Panou de comandă Stație de comandă | 1730x1013x2380 870x430x1320 | 1730x1020x2700 790x430x1320 700x650x1600 |
Masa cheii, kg |
Mecanismul principal care efectuează operațiunile de înșurubare și deșurubare a țevilor este un bloc cheie.
Pe patinele de ghidare, blocul cheie se deplasează de-a lungul căruciorului sub acțiunea a doi cilindri pneumatici cu dublă acțiune, asigurând alimentarea dispozitivului de strângere a țevii de foraj și îndepărtarea din acesta. Rotirea dispozitivului de prindere a țevii blocului de chei - de la motorul de aer prin cutia de viteze. Căruciorul se rotește liber în partea superioară a coloanei, iar poziția sa în timpul funcționării este fixă. Căruciorul cu blocul de chei se poate deplasa de-a lungul coloanei în înălțime. Cheia este atașată rigid de baza instalației de foraj prin partea inferioară a șirului. Panoul de control oferă control de la distanță al operațiunii tastei.
Domeniul de aplicare al cheii AKB-ZM2-E2 și gama de înșurubare-deșurubare a conexiunilor sunt similare cu cheia AKB-ZM2.
Cheia PKB-1 este suspendată în instalația de foraj pe o frânghie. Înălțimea suspensiei sale este reglată de un cilindru pneumatic de la panoul de control.
În ultimii ani, pentru mecanizarea proceselor de alcătuire și spargere a țevilor de foraj și a țevilor de tub în timpul forării puțurilor de petrol și gaze, a fost dezvoltat și utilizat un clește de foraj automat cu două viteze cu o antrenare pneumatică AKB-4, care este dezvoltat pe baza cleștii AKB-ZM2 folosit și are un coeficient ridicat de unificare cu acesta. Cheia este ușor de operat și întreținut, fiabilă în funcționare.
Avantajele bateriei cheie-4:
Cuplu mare - 70 kNm - vă permite să faceți fără utilizarea cheilor mașinii;
Cuplul este aplicat îmbinării pentru a fi înșurubat fără șoc, datorită căruia uzura țevilor de foraj și a spargerilor cheii în sine este redusă semnificativ;
Limitatorul de cuplu instalat pe cheie vă permite să faceți conexiuni cu un cuplu prestabilit, la atingerea căruia motorul de aer este oprit.
Caracteristicile tehnice ale bateriei-4:
1. Diametrul nominal al țevilor care se înșurubează sau se deșurubează, mm
foraj - 108-216; carcasă - 114-194;
2. Acționare rotativă - motor pneumatic cu piston;
3. Putere de antrenare, kW-13;
4. Presiunea aerului în rețea, MPa - 0,7-1,0; ,sh5. Cuplu, kNm: i "i la prima turație (rapidă) - 5,0;
% la a doua viteză (lentă) - 70,0;
6. Dimensiuni de gabarit, mm
bloc cheie cu cărucior și coloană 1780x1230x2575; "panou de control 870x430x 1320;
greutatea cheii, kg - 2700.
; Mânerul pneumatic cu pană PKR-560 este utilizat pentru prinderea și eliberarea mecanică a țevilor de foraj și tubaj. Este montat în rotor și are patru pene controlate de la telecomandă cu ajutorul unui cilindru pneumatic. , La forarea puțurilor, se mai folosesc un pivot, pompe de noroi, un furtun de presiune și un rotor.
Rotire(Fig. 40) este utilizat pentru a conecta sistemul de deplasare nerotativ și cârligul de foraj la țevile de foraj rotative și pentru a introduce fluid de spălare la presiune înaltă în acestea.
pompe de noroi sunt folosite pentru a injecta fluid de foraj în puț. La forarea puțurilor, se folosesc pompe cu două cilindri cu piston cu dublă acțiune.
În prezent, uzina Izhneftemash a stăpânit producția de pompe de noroi NB 32, NB-50, NB-80, NB 125Izh (pompe orizontale cu două cilindri cu dublă acțiune, acționate cu un reductor integrat).
Pompele NB32, NB50, NB80 sunt folosite pentru pomparea fluidului de spălare (apă, noroi) în puțuri.
orez. 40. Rotativ: 1 - rulmenti; 2 - corp; 3 - garnituri de ulei; 4 - link; 5 - conducta de presiune; 6 - capac carcasa; 7 - portbagaj
bine, în timpul forajelor de explorare geologică și de explorare structurală pe
ulei si gaz.
Pompa NB 125Izh este utilizată:
Pentru injectarea fluidului de spălare la forarea puțurilor de petrol și gaze;
pentru injectarea de mediu lichid atunci când se efectuează operațiuni de spălare și stoarcere în procesul de reparare a puțului;
pentru injectarea apei, soluții polimerice într-o formațiune productivă pentru intensificarea producției de petrol; pentru pomparea diferitelor lichide neagresive, inclusiv ulei inundat.
Specificații pompe.
Numele pompei | Cursa pistonului, mm | Înălțimea de aspirație, m |
NB32 | ||
NB50 | ||
NB80 | ||
NB125 |
Pompe de presiune și alimentare.
Numele pompei | putere, kWt | Diametru bucșe înlocuibile, mm | Alimentare volumetrică, m 3 / oră | Presiune maximă, MPa | Numărul de curse duble pe minut |
NB32 | 15,8 | 4,0 | |||
20,9 | 4,0 | ||||
26,3 | 3,2 | ||||
32,4 | 2,6 | ||||
NB50 | 20,9 | 6,3 | |||
26,3 | 5,0 | ||||
32,0 | 4,1 | ||||
39,6 | 3,4 | ||||
NB80 | 19,8 | 10,0 | |||
26,0 | 8,0 | ||||
32,7 | 6,3 | ||||
40,3 | 5,2 | ||||
50,4 | 4,3 | ||||
NB 125IZH | 25,2 | 17,0 | |||
32,0 | 13,0 | ||||
43,5 | 10,0 | ||||
54,0 | 8,8 | ||||
NB 125IZH WT. | 33,0 | 13,0 | |||
42,0 | 10,0 | ||||
57,0 | 7,5 | ||||
71,0 | 6,0 |
Pe baza pompelor de noroi, fabrica produce unități de pompare ANB 22, AN-50 și AN-125.
Unitățile de pompare constau dintr-un cadru pe care sunt instalate o pompă de noroi, un motor electric și o transmisie cu curele trapezoidale.
Unitatea ANB 22 are o cutie de viteze cu trei trepte care vă permite să modificați debitul pompei într-o gamă largă.
În plus față de pompele enumerate, instalația a stăpânit și produce o pompă de cimentare NTs 320. NTs 320 este o dublă orizontală. Pompă cu piston dubla actiune cu integrat unelte melcate, concepute pentru injectarea de medii lichide (argilă, ciment, soluții de sare) în timpul operațiunilor de spălare și stoarcere și cimentarea puțurilor de petrol și gaze în timpul forării și reviziei acestora.
Designul pompei este dezvoltat pe baza pompei 9T.
Puterea utila a pompei este de 108 kW.
Raport de transmisie pereche de vierme - 22.
Presiunea și debitul volumic al pompei.
Furtun de presiune(furtun de foraj) este utilizat pentru a furniza fluid de spălare sub presiune către pivot.
Rotor(Fig. 41) servește la rotirea garniturii de foraj la o frecvență de 30-300 rpm în timpul forajului, la perceperea cuplului de reacție al șirului, la menținerea greutății țevilor de foraj sau tubaj instalate pe masa acestuia, pe elevator sau pene. la alcătuirea lumânărilor în timpul operațiunilor dus-întors, pescuit și alte lucrări.
Orez. 41. Rotor: 1 - cadru; 2 - o masă cu o roată dințată întărită; 3 - cleme; 4 - garnituri; 5 - carcasă; 6 - arbore
Rotorul constă dintr-un cadru 1, în cavitatea interioară a căruia este montată pe un rulment o masă 2 cu o roată dinţată inelară întărită, un arbore 6 pe o parte şi o roată dinţată conică pe cealaltă parte, o carcasă 5 cu o suprafaţă ondulată exterioară. suprafață, căptușeli 4 și cleme 3 pentru conducta de conducere. În timpul funcționării, mișcarea de rotație de la troliu este transmisă arborelui prin intermediul unei transmisii cu lanț și este transformată într-o mișcare verticală de translație a țevii de conducere prinse în masa rotativă prin cleme.
Actuator furnizează putere troliului, pompelor de noroi și rotorului. Motorul de foraj al instalației de foraj este diesel, electric, diesel-electric și diesel-hidraulic.
Acționare diesel Se aplică în locurile de foraj unde nu există putere electrică de puterea necesară.
Acționare electrică ușor de instalat și de operat, fiabilitate ridicată și rentabilitate.
Diesel-electric un motor diesel care rotește un generator care, la rândul său, alimentează un motor electric.
Diesel-hidraulic antrenarea constă dintr-un motor cu ardere internă și o transmisie turbo. Puterea totală de antrenare a instalațiilor de foraj este de la 1000 la 4500 kW, care este distribuită antrenării pompelor de foraj și rotorului.
Sistemul de circulație servește la colectarea și purificarea nămolului de foraj uzat, pregătirea porțiunilor noi și pomparea nămolului curățat în puț.
Capete de burghiu
Dalta este un instrument de foraj pentru distrugerea mecanică a rocilor în procesul de forare a puțului. Utilizări de găurire rotativă cu lameȘi con biți.
Biții cu lame sunt biți de tăiere și forfecare concepute pentru găurirea rocilor vâscoase și plastice de duritate redusă (argile vâscoase, șisturi fragile etc.) și abrazivitate scăzută, cel mai des utilizate în forajul rotativ.
Biții conici sunt bucăți de tăiere și acțiune abrazivă cu duze de tăiere cu diamant sau aliaje dure. Cei mai des folosiți biți tricon.
Biții conici sunt utilizați în forajul rotativ pentru găurirea rocilor cu proprietăți fizice și mecanice diferite, inclusiv atunci când se alternează roci cu vâscozitate scăzută extrem de plastice cu roci de duritate medie.
Biții conici sunt fabricați din oțeluri de înaltă calitate cu tratament chimico-termic ulterior al pieselor cu uzură ridicată, iar dinții sunt fabricați din aliaje dure.
Dălți cu diamante. Biți de diamant sunt folosiți pentru găurirea rocilor dure. Muchiile tăietoare ale acestor biți sunt echipate cu diamante artificiale. Daltele cu diamante sunt spirală, radialăȘi călcat.În biți de diamant spiralat, partea de lucru are spirale echipate cu diamante artificiale și găuri de spălare. Biți de diamant în spirală sunt utilizați în forajul cu turbine pentru distrugerea rocilor cu abrazive redusă și mediu abrazive.
La biți radiali de diamant, suprafața de lucru este formată din margini radiale sub formă de sector, dotate cu diamante, iar între ele există găuri de spălare.
Acești biți sunt utilizați în forajele rotative și cu turbină pentru distrugerea rocilor dure și a rocilor slab abrazive de duritate medie.
Biți de diamant în trepte au o suprafață de lucru sub forma unei forme trepte. Biți în trepte sunt utilizați în metodele de foraj rotativ și cu turbină atunci când se forează roci moi și medii cu abrazive redusă.
Durata de viață și penetrarea pe bit a biților de diamant este mult mai lungă decât a altor bucăți. Datorită acestui fapt, numărul operațiunilor de declanșare în timpul forării puțului este redus.
Rezultate bune în producția de burghie, burghie armate cu diamante sintetice pentru forarea puțurilor verticale, direcționale, orizontale și puțurilor orizontale laterale au fost obținute la întreprinderea comună ruso-americană din Udmurtia JV „UDOL” („Bițe Udmurt”). Aici sunt produse peste 50 de dimensiuni standard de diferite biți, capete de miez și calibratoare:
a) dălți cu diamante diverse modele;
b) biți palete RDS cu dimensiuni de la 119 la 259 mm;
c) biţi cu freze din carbură PC;
d) biți bicentrici SR pentru foraj cu alezarea simultană a sondei de la 120,6x141,9 la 215,9xx250 mm;
D și e) capete de foraj pentru carotare, precum și prelevarea carotelor;> . proiectile pentru carotare în puțuri orizontale; o "e) calibratori.
Biții decentrați (bicentrici) sunt extrem de eficienți și de încredere. Rata de penetrare cu utilizarea lor crește de 3-5 ori.
Biți pentru carotare. Pentru întocmirea unei secțiuni stratigrafice, studierea caracteristicilor litologice ale rocilor productive, determinarea conținutului de petrol sau gaze în roci etc. în puțuri în timpul forajului sunt selectați stâlpi de rocă nedistrusă ai orizontului productiv (miez). Pentru prelevare și ridicare la suprafața miezului se folosesc bucăți speciale de carotare (Fig. 42). Un astfel de burghiu constă dintr-un cap de foraj (1) și un set de miez atașat de corpul capului de foraj prin intermediul unei conexiuni filetate. Capetele de foraj sunt conice, diamantate
și carbură. Frezele din capul de foraj sunt montate astfel încât roca din centrul fundului puțului de foraj să nu fie distrusă, datorită căreia se formează un miez (2). Capetele de foraj pentru forarea puțurilor cu carotare sunt produse în principal cu patru și șase conuri, deși există și opt conuri. În capetele de foraj cu diamant și aliaje dure, elementele de tăiere a rocii sunt amplasate astfel încât să permită acționarea rocilor distruse numai de-a lungul periferiei găurii de jos, lăsând un stâlp de rocă nedistrus în centru. Stâlpul de rocă în timpul forării ulterioare a puțului intră în setul de miez, care constă dintr-un corp (4) și un miez. 42. Schema aparatului ^ numit bit lonkovy: 1 - foraj purtător de sol. Gruntonoska obes-cap; 2 - miez; 3 - purtător de sol; păstrează siguranța miezului 4 - corpul setului de miez; 5 - în timpul forării unei puțuri, a unui robinet cu bilă și la ridicarea instrumentului de foraj
unealta la suprafata. În partea inferioară a dragului sunt instalate spărgătoare de miez și suporturi de miez, iar în partea superioară este montată o supapă cu bilă (5), care asigură trecerea fluidului din dragă atunci când acesta este umplut cu miez. Pentru eșantionarea carotelor se folosesc bucăți de miez cu un suport de sol amovibil și nedemontabil. Când se folosește un burghiu cu cap detașabil, suportul de pământ cu miezul este ridicat coborând în gaura de foraj.
șuviță de frânghie de oțel cu prindere. După ridicarea colectorului, se scoate un miez din dragă, se instalează o dragă eliberată de miez în jgheabul setului de miez și, după ce a coborât instrumentul de foraj, forarea se continuă cu prelevarea de miez în intervalul următor. Capetele de foraj pentru eșantionarea carotelor, produse de JV „UDOL”, asigură îndepărtarea miezului de 85-100%.
Țevi de foraj
Țevile de foraj la forarea puțurilor sunt utilizate pentru a transfera rotația burghiului în timpul forării rotative, pentru a furniza fluid de spălare turboforătorului în timpul forării cu turbine, pentru a crea o sarcină asupra burghiului, pentru a furniza fluid de foraj la fundul puțului pentru a răci burghiul, pentru a crește la suprafața rocii distruse, ridicați și coborâți burghiul, turboforghiul, burghiul electric, transportatorii de sol etc.
La forarea puțurilor se folosesc țevi de foraj din oțel (SBT) cu capete plantate în interior și în exterior, cu capete de legătură sudate, cu coliere de blocare, cu coliere de stabilizare, precum și țevi de foraj din aliaj ușor (LBT).
Țevile de foraj din oțel sunt fabricate din oțeluri carbon și aliate. Țevile de foraj cu capetele răsturnate în interior și în exterior cu un diametru de până la 102 mm și mai mult sunt produse în lungimi mai mari de 11,5 m. Țevile cu lungimea de 6 m sunt furnizate complet cu racorduri și țevi cu lungimea de 8 și 11,5 m. m sunt furnizate fără cuplaje. Pentru conectarea țevilor de foraj se folosesc încuietori de foraj: ZN - încuietori cu orificiu normal; ЗШ - încuietori cu un orificiu lat; ZU - încuietori cu un orificiu traversant mărit. Încuietorile ЗН și ЗШ sunt folosite pentru a conecta țevile de foraj cu capete răsturnate în interior, iar zăvoarele ZU sunt folosite pentru a conecta țevile de foraj cu capete răsturnate în exterior.
Țevile de foraj sunt produse cu un diametru exterior de 60, 73, 89, 102, 114, 127,140 și 169 mm și o grosime a peretelui de 7 până la 11 mm. Pentru a reduce numărul de înșurubare și deșurubare a țevilor în timpul operațiunilor dus-întors, țevile care utilizează cuplaje filetate
lupta se leagă pe secțiuni (lumânări). Secțiunile țevilor de foraj sunt interconectate la coborârea în puț folosind încuietori filetate speciale, care constau dintr-un niplu cu filet conic exterior și un cuplaj cu un filet conic intern.
Secțiunile interconectate ale țevii de foraj se numesc șir de foraj. Prima țeavă superioară dintr-un șir de foraj se numește kelly (profil pătrat). Ultima țeavă de foraj din partea inferioară se numește guler de foraj (DC), care este instalat deasupra burghiului. Gulerul de foraj este proiectat pentru a crește greutatea burghiului și a crește stabilitatea fundului garniturii de foraj. Este realizat dintr-o țeavă cu pereți groși. Utilizarea gulerelor de foraj vă permite să creați o sarcină pe gaura de jos cu un set de mai multe țevi cu pereți groși interconectate, îmbunătățind astfel condițiile de funcționare ale șirului de foraj. Pentru a reduce greutatea întregului șir de foraj la forarea puțurilor adânci, în loc de țevi de foraj din oțel, țevi de foraj din aliaje de aluminiu (un aliaj de aluminiu cu cupru și magneziu), care se numesc țevi de foraj din aliaj ușor (LBT), sunt folosite. Țevile de foraj din aliaj ușor sunt produse cu capete răsturnate la interior cu diametrul de 73, 93, 114, 129 și 147 mm. La capetele acestor conducte se taie un fir standard. Ele sunt conectate între ele cu ajutorul unor încuietori speciale din oțel. Utilizarea țevilor de foraj din aliaj ușor face posibilă reducerea greutății garniturii de foraj de aproape două sau mai multe ori. Țevile de foraj sunt produse la fabrici cu lungimea de 6,8 și 11,5 m. Lumânările sunt asamblate cu o lungime de 25-36 m.
Motoare de fund
Turbodrilluri. În forajul cu turbină, burghia este antrenată de un motor de foraj numit turboforator. Turbodrill - este un motor de fund care transformă energia fluxului de noroi în mișcare în mișcare mecanică- rotirea arborelui turboforatorului conectat la burghiu.
Orez. 43. Etapa turbinei
Turboforurul este o turbină cu mai multe trepte cu un număr de trepte de la 25 la 350. Fiecare treaptă de turbină (Fig. 43) constă dintr-un stator (1) conectat rigid la corpul turboforurului și un rotor (2) montat pe arborele turboforghiului. În stator și rotor, fluxul fluidului de foraj își schimbă direcția și, curgând de la o etapă la alta, eliberează o parte din puterea hidraulică a fiecărei etape. Puterea generată pe arborele turboforurului de către toate etapele este însumată pe arborele turboforurului și transferată la burghiu.
Se crede că pentru funcționarea eficientă a unui turboforator, este necesar să existe aproximativ o sută de turbine. În fiecare turbină, palele rotorului sunt plasate uniform de-a lungul perimetrului. Înainte de fiecare turbină-rotor din carcasa turboforurului, sunt instalate turbine-statoare similare ca design. Fiecare pereche de turbine cu rotor și stator formează o treaptă de turboforfor. În turboforatoarele moderne, numărul acestor etape ajunge la trei sute. Fluxul fluidului de foraj lovește mai întâi paletele turbinei statorului, schimbă direcția și lovește paletele rotorului, apoi schimbă din nou direcția, iar forța radială rezultată prin turbinele rotorului antrenează arborele turboforajului. Industria produce un turboforator cu o singură secțiune și mai multe trepte. Se mai produc turboforatoare cu două, trei și patru secțiuni, având, respectiv, până la 230, 270 și respectiv 280 de turbine. Turboforatoarele cu secțiuni multiple sunt folosite la forarea puțurilor adânci.
Pentru eșantionarea carotelor la forarea puțurilor prin metoda cu turbină, se folosesc turboforatoare (turbobiți) cu un suport de sol amovibil. Turboburatoarele sunt produse în principal cu un diametru exterior de 102 până la 235 mm, adică. pot fi folosite la forarea puţurilor cu bucăţi de diferite diametre.
De asemenea, sunt utilizate motoare hidraulice de joasă frecvență - acestea sunt motoare cu șurub (de deplasare) cu o viteză a arborelui de 90 până la 300 rpm. Motorul cu șuruburi de fund este format din două secțiuni: motor și ax.
Secțiunea motorului este formată dintr-un rotor elicoidal (șurub intern) și un stator cu șurub intern. La rotor, șurubul este mai scurt cu un dinte, iar axa rotorului este decalată față de axa statorului. Fluidul de foraj, care trece prin golul mecanismului șurubului, rotește șurubul rotorului.
Șurubul rotorului este conectat la un arbore, la capătul căruia se află un filet pentru înșurubarea bitului.
Burghie electrice. Un burghiu electric este un motor electric de fund, cu ajutorul căruia bitul este rotit în fundul puțului. Un motor de curent alternativ trifazat este plasat în corpul mașinii de găurit electric. Electricitatea este furnizată motorului electric de la suprafață printr-un cablu special situat în interiorul țevilor de foraj.Sub pivotant există un colector de curent inelar, căruia îi este furnizat curent electric prin cablu.Întregul cablu este împărțit în secțiuni separate.Fiecare secțiunea are o lungime egală cu lungimea suportului de foraj.Conectarea și deconectarea secțiunilor de cablu în timpul înșurubarii și deșurubarea lumânărilor în timpul operațiunilor de declanșare se efectuează folosind încuietori (contacte) speciale pe fiecare lumânare pentru conducte.La înșurubarea țevilor verticale, tija intră în manșon și închide contactul electric, iar atunci când este deșurubat, contactul se deschide.În procesul de foraj, garnitura de foraj este staționară și fluidul de foraj este furnizat prin ea la fundul puțului. în același timp, rotația viteza rotorului nu depinde de cantitatea de fluid de foraj furnizată la fundul puțului.
Dezavantajul forajului electric este inconvenientul furnizării de energie electrică a burghiului electric și dificultatea de a asigura fiabilitatea etanșării burghiului electric de la pătrunderea noroiului de foraj în acesta. La găurirea electrică se folosesc burghie electrice cu diametrul de 170, 215 și 250 mm și biți de 190,5; 244,5; 295,3 mm.
eu . Partea tehnica. Caracteristică și scurta descriere dispozitive.
Instalații și structuri de foraj……………………………………………………………………………..4
Sistemul de călătorie……………………………………………………………………………….………..5
Desenele…………………………………………………………………..……………………...6
Rotoare…………………………………………………………………………………………………….7
Pompe de noroi și echipamente ale sistemului de circulație…………..……………………8
Pivoare……………………………………………………………..………………………………9
Acționări de putere ale instalațiilor de foraj………………………………………………………………….9
Echipament de etanșare a capului de puț…………..…………………10
II . Partea tehnologica.
1. Forarea sondelor de petrol și gaze…………………………….……..14
Familiarizarea cu metodele de alimentare manuală a biților, găurire
cu controler de bit, învățând să găurim cu un rotor…………………………………………………………..14
Familiarizarea cu metodologia dezvoltării raționale a
Lot……………………………………………………………………………………………………………15
Efectuarea de lucrări de bază în software open source cu ajutorul special
toate echipamentele……………………………………………………………………………….16
Pregătirea țevii pentru târât, montarea liftului
pe rotor, scoaterea acestuia de pe rotor, plantarea țevilor pe pene………………………………………………17
Verificarea filetului de blocare, înșurubarea BT cu o cheie
a cărui baterie, reatașarea și deblocarea conexiunilor de blocare cu
folosind cheile UMK……………………………………………………………………………………………………………………… …………………………………………………………………………………………………………………………………… …………………………………………………………………………………………………………………………………… ………………………………………………………………………………………………
Inspecția și măsurarea BT și UBT, instalarea BT pe un sfeșnic, pe-
strunjirea și răsucirea biților………………………………………………………………………19
Spălarea puțului………………………………………………………………………………….20
BHA și reglementarea regimului de foraj pentru combaterea autopro-
curbura arbitrară a sondei………………………………………………………………………...…….22
2. Familiarizarea cu forarea sondei cu clustere……………………………………….23
3. Executarea și cimentarea șirurilor de carcasă………………………………………..24
4. Deschiderea și testarea orizonturilor petroliere…….………..26
5. Lucrări de urgență în fântână…………………………………………….………..27
6. Eliminarea emisiilor de motorină și gaze……………….…….…….28
eu . Partea tehnica
Caracteristici și scurtă descriere a dispozitivelor
Instalații și instalații de foraj
Procesul de foraj este însoțit de coborârea și ridicarea șirului de foraj în puț, precum și de menținerea acesteia în greutate. Masa instrumentului cu care este necesar să se opereze în acest caz ajunge la multe sute de kilonewtoni. Pentru a reduce sarcina pe frânghie și a reduce puterea instalată a motoarelor, se utilizează echipamente de ridicare (Fig. 2.2), constând dintr-un turn, un dispozitiv de tragere și un sistem de tackle (polispast). Sistemul de deplasare, la rândul său, constă dintr-o parte fixă - un bloc de coroană (blocuri de scripete fixe) instalat în partea de sus a felinarului turnului și o parte mobilă - un bloc de călătorie (bloc de scripete mobil), frânghie de călătorie, cârlig și chingi. . Echipamentul de ridicare este o parte integrantă a oricărei instalații de foraj, indiferent de metoda de foraj.
Instalația de foraj este proiectată să ridice și să coboare garnitura de foraj și țevile de tubaj în puț, să mențină garnitura de foraj suspendată în timpul forajului, precum și să plaseze în el sistemul de deplasare, țevile de foraj și unele dintre echipamentele necesare procesului de foraj. . Cel mai grav pericol atunci când se lucrează la instalațiile de foraj este distrugerea lor parțială sau completă. Principalul motiv care duce la căderea sau distrugerea turnurilor este supravegherea insuficientă a stării acestora în timpul funcționării pe termen lung. Din aceste motive, au fost introduse modificări în normele de siguranță care prevăd verificări periodice obligatorii ale turnurilor, inclusiv demontarea completă și revizuirea pieselor acestora, precum și încercări cu încărcarea turnurilor asamblate.
În plus, derrick-ul trebuie inspectat și verificat cu atenție de fiecare dată înainte de forare, înainte de a rula șirurile de tubaj, de eliberarea unui burghiu blocat sau a unui coard de tubaj, în caz de accidente și după vânturi puternice (15 m/s pentru zone deschise, 21 m/s). pentru zonele de pădure și taiga, precum și atunci când turnul este construit într-o groapă). Turnurile de tip catarg sunt montate în poziție orizontală și apoi ridicate în poziție verticală folosind dispozitive speciale. Transportul turnului se realizează în formă asamblată împreună cu platforma lucrătorului călăreț în poziție orizontală pe un dispozitiv special de transport. În același timp, sistemul de deplasare nu este demontat împreună cu turnul. Dacă din cauza condițiilor terenului este imposibil să se transporte turnul în ansamblu, acesta este dezasamblat în secțiuni și transportat pe părți prin transport universal.În practica de foraj, pe lângă turnurile de tip catarg, turnurile de tip turn sunt încă utilizate, care sunt asamblate folosind metoda de sus în jos. Înainte de a începe instalarea, pe baza turnului este montat un lift. După finalizarea asamblarii turnului, liftul este demontat.
Concomitent cu instalarea instalației de foraj și instalarea derrickului, se realizează construcția de structuri de lângă puț. Acestea includ următoarele structuri: 1) Reducere (agregate), magazie, concepută pentru a adăposti motoarele și mecanismele de transmisie ale troliului. Este atașat la turn din partea laterală a panoului său din spate în direcția opusă alei. Dimensiunile magaziei de viteze sunt determinate de tipul de instalare. 2) Magazin de pompe pentru a găzdui pompele de foraj și echipamentele de alimentare. Este construit fie ca prelungire pe partea laterală a felinarului turnului magaziei de viteze, fie separat pe partea laterală a turnului. Pereții și acoperișul mașinilor de transmisie și pompe, în funcție de condițiile specifice, sunt acoperiți cu plăci, tablă ondulată, scuturi din stuf, țesături de cauciuc sau folie de polietilenă. Utilizarea unor instalații de foraj necesită o combinație de unelte și hale de pompare. 3) O punte de recepție concepută pentru așezarea carcasei de foraj și a altor țevi și pentru a muta echipamente, unelte, materiale și piese de schimb de-a lungul acestuia. Podurile de recepție sunt orizontale și înclinate. Înălțimea de instalare a podurilor de recepție este reglată de înălțimea de instalare a cadrului instalației de foraj. Lățimea podurilor de recepție este de până la 1,5...2 m, lungimea de până la 18 m. 4) Un sistem de dispozitive pentru curățarea noroiului de foraj, precum și depozite pentru produse chimice și materiale vrac. 5) O serie de structuri auxiliare în timpul forajului: pe acționarea electrică - platforme de transformare, pe motoarele cu ardere internă (ICE) - platforme pe care se află containere pentru combustibili și lubrifianți etc.
Sistem de călătorie
În procesul de forare a unui puț, sistemul de ridicare efectuează diverse operații. Într-un caz, este folosit pentru deplasare pentru a înlocui un burghiu uzat, coborârea, ridicarea și ținerea coardelor de foraj la greutate în timpul carotării, pescuitului sau a altor lucrări în puț, precum și pentru coborârea țevilor de tubaj. În alte cazuri, asigură crearea forței necesare asupra cârligului pentru a extrage o garnitură de foraj blocată din puț sau în caz de accidente cu acesta. Pentru a asigura o eficiență ridicată în aceste diverse lucrări, sistemul de ridicare are două tipuri de viteze ale cârligului de ridicare: tehnice pentru declanșare și tehnologice pentru alte operațiuni.
![]() |
Datorită modificării greutății garniturii de foraj în timpul ridicării, pentru a menține timpul la minimum, sistemul de ridicare trebuie să poată modifica vitezele de ridicare în funcție de sarcină. De asemenea, servește pentru a ține șirul de foraj coborât în puț în timpul forajului.
Sistemul de ridicare al instalației (Fig. III.1) este un mecanism de ridicare cu lanț, format dintr-un bloc de coroană. 4, bloc de călătorie (în mișcare). 2, frânghie de oțel 3, care este o conexiune flexibilă între desene 6 şi un mecanism 7 pentru fixarea capătului fix al frânghiei. blocul coroanei 4 instalat pe platforma superioară a instalației de foraj 5. capăt mobil A frânghie 3 atașat la tamburul troliului 6, iar capătul fix B- prin dispozitivul de fixare 7 la baza turnului. Un cârlig este atașat de blocul de călătorie 1 , pe care este suspendat pe verigi un lift pentru tevi sau un pivotant. În prezent, blocul de deplasare și cârligul de ridicare sunt în multe cazuri combinate într-un singur mecanism - blocul de cârlig.
Desenele
Troliul este mecanismul principal al sistemului de ridicare al instalației de foraj. Este destinat efectuării următoarelor operațiuni: coborârea și ridicarea țevilor de foraj și tubaj; menținerea șirului de țevi pe greutate în timpul forării sau spălarea puțului; ridicarea șirului de foraj și a țevilor în timpul extinderii ; transmiterea rotației la rotor; alcătuirea și desfacerea țevilor; lucrări auxiliare la tragerea de instrumente, echipamente, țevi etc. în instalația de foraj; ridicând turnul asamblat în poziție verticală.
Structura este formată dintr-un cadru sudat pe care sunt instalate arborii de ridicare și transmisie, o cutie de viteze, un sistem de frânare, inclusiv frânele principale (cu bandă) și auxiliare (de reglare), și un panou de comandă. Toate mecanismele sunt acoperite cu scuturi de siguranță. Arborele de ridicare al troliului, care primește rotația de la cutia de viteze, transformă mișcarea de rotație a motorului de antrenare în mișcarea de translație a cablului de deplasare, al cărui capăt mobil este fixat pe tamburul arborelui de ridicare. Cârligul încărcat se ridică odată cu consumul de energie, în funcție de greutatea țevilor ridicate, și coboară sub acțiunea greutății proprii a țevilor sau a blocului de călătorie, cârlig și lift, când liftul coboară pentru următoarea lumânare.
Troliurile sunt echipate cu dispozitive de alimentare cu energie la ridicarea sforii și dispozitive de frânare pentru absorbția energiei degajate la coborârea acesteia. Pentru a crește eficiența în timpul ridicării cârligului cu un lift sau o coloană fără sarcină de greutate variabilă, troliurile sau mecanismele lor sunt cu mai multe viteze. Trecerea de la viteză mare la viteză mică și invers este efectuată de ambreiaje operaționale cu frecare, oferind pornire lină și timp minim petrecut în aceste operațiuni. În timpul ridicării coloanelor de diferite greutăți, vitezele din cutiile de viteze sunt comutate periodic. Controlul vitezei de funcționare a cutiei nu este necesar.
Puterea transmisă troliului îi caracterizează principalele proprietăți operaționale și tehnice și este un parametru de clasificare.
Rotoarele sunt proiectate pentru a roti o garnitură de foraj suspendată vertical sau pentru a absorbi cuplul reactiv atunci când se forează cu motoare de foraj. Ele servesc, de asemenea, pentru a susține greutatea șirurilor de foraj sau de tubaj montate pe masa acestuia, pe un lift sau pene. Rotoarele sunt, de asemenea, folosite la spargerea și refacerea țevilor în operațiuni de împiedicare, pescuit și de urgență. Rotorul este, parcă, un reductor cu roți conice, a cărui roată conică antrenată este montată pe o bucșă conectată la masă. Axa verticală a mesei este situată de-a lungul axei puțului.
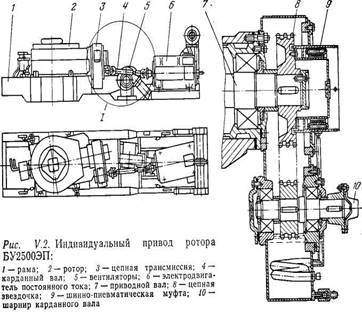
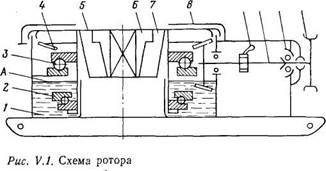
pe principal 3 și auxiliar 2 suporturi montate în carcasă 1, care formează simultan o baie de ulei pentru lubrifierea transmisiei şi a rulmenţilor.
Partea superioară a mesei este protejată de un gard. 8. arbore de transmisie de mare viteză 10 situat orizontal pe rulmenti 11, perceperea sarcinilor radiale și orizontale. Arbore 10 antrenat: în rotație de la un pinion cu lanț 12 sau prin intermediul unui jug cardanic situat la capătul arborelui. Rotorul este echipat cu un opritor 9, când este activată, rotirea mesei devine imposibilă. Fixarea mesei rotorului este necesară în timpul declanșării și găuririi cu motoare de fund pentru perceperea cuplului reactiv.
Pompe de noroi și echipamente pentru sisteme de circulație
Pompele de noroi și sistemul de circulație îndeplinesc următoarele funcții:
Injectarea fluidului de foraj în garnitura de foraj pentru a asigura circulația în puț în timpul forajului și curățarea eficientă a găurii de fund și a burghiei de tăieturi, spălare, lichidare a accidentelor, creând o rată de creștere a fluidului în interior suficient pentru a aduce roca la suprafata;
Alimentarea cu energie hidraulică a bitului, oferind un debit mare (până la 180 m / s) de soluție din duzele sale pentru distrugerea parțială a rocii și curățarea găurii de fund de particulele forate;
Alimentarea cu energie electrică a motorului hidraulic de fund.
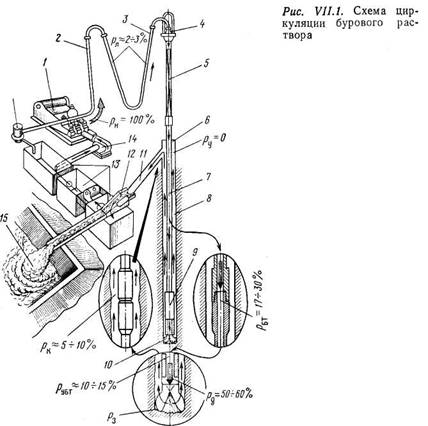
În timpul procesului de foraj, în cele mai multe cazuri, soluția circulă într-un circuit închis. Din tancuri 13 soluția curățată și preparată intră în pompele de rapel 14, care îl alimentează la pompele de foraj /. Acesta din urmă pompează soluția la presiune înaltă (până la 30 MPa) prin conducta de refulare, prin conductă 2, manșon flexibil 3, pivotant 4, Kelly 5 k cap de fântână 6. O parte din presiunea pompelor este utilizată pentru a depăși rezistența în sistemul de pământ. Apoi, fluidul de foraj trece prin garnitura de foraj 7 (țevi de foraj, guler de foraj și motor de foraj 9) la bit 10. Pe această cale, presiunea soluției scade din cauza consumului de energie pentru a depăși rezistența hidraulică.
Apoi fluidul de foraj, din cauza diferenței de presiune din interiorul țevilor de foraj și din fundul puțului, iese din duzele burghiului cu viteză mare, curățând fundul și burghiul de butași. Restul energiei fluidului este cheltuită pentru ridicarea tăierilor și depășirea rezistenței în inelarul inelar 8.
Ridicat la suprafață până la gură 6 soluția uzată trece prin jgheaburi 11 la unitatea de curățare 12, de unde sunt scoase la hambar 15 butașii, nisipul, nămolul, gazul și alte impurități intră în rezervoare 13 cu dispozitive 16 pentru a-și restabili parametrii și este din nou trimis la pompele de rapel.Linia de injecție este alcătuită dintr-o conductă de înaltă presiune care transportă soluția de la pompe/la conductă 2 și manșon flexibil 3, conectarea ridicătorului 2 cu pivotant 4. Linia de presiune este echipată cu supape și instrumente. Pentru lucrul în zone cu un climat rece, este prevăzut un sistem de încălzire prin conducte.
Sistemul de scurgere este echipat cu dispozitive pentru curatarea si pregatirea fluidului de foraj, rezervoare, linie de aspiratie, filtre, injectie Pompe centrifuge, supape și recipiente pentru depozitarea soluției.
pivotează
Un pivot este o legătură intermediară între un bloc de călătorie care se mișcă progresiv, cu un cârlig, un manșon de foraj și o garnitură de foraj rotativă, care este conectat printr-o țeavă de conducere la arborele pivotant prin intermediul unui filet de blocare. Pentru a asigura alimentarea cu fluid de foraj sau gaz, pivotul mobil este conectat la linia de presiune folosind un furtun flexibil de foraj, al cărui capăt este atașat la ieșirea pivotantă, iar celălalt la ridicător.
Pivoarele au dispozitive pentru umplerea, scurgerea uleiului și controlul nivelului acestuia, precum și un ventilator pentru echilibrarea cu presiune atmosferică vapori din interiorul carcasei, formați în timpul încălzirii în timpul funcționării. Acest dispozitiv nu scurge ulei atunci când transportați pivotul în poziție orizontală.
Mărimea pivotului este determinată de sarcina dinamică pe care o poate suporta în timpul rotației garniturii de foraj, sarcina statică și viteza de rotație admisă, presiunea maximă de funcționare a fluidului de foraj pompat, greutatea și dimensiunile totale. Fiecare pivot are un filet standard de blocare conic pe partea stângă pentru conectarea la o țeavă principală în două până la trei dimensiuni. Corpul pivotului este realizat într-o formă aerodinamică, astfel încât să nu se agațe de părțile turnului atunci când se mișcă. Pivotele sunt adaptate pentru transport cu orice mijloc de transport fara ambalaj.
Acționări electrice ale instalațiilor de foraj
O unitate de foraj este un set de motoare și transmisii care le reglează funcționarea și dispozitive care convertesc energia termică sau electrică în energie mecanică, controlează energia mecanică și o transferă către echipamente de acționare - pompe, un rotor, un troliu etc. Puterea de antrenare (la intrarea în transmisie) își caracterizează principalul consumator și proprietățile tehnice și este un parametru (principal) de clasificare.
În funcție de sursa de energie primară utilizată, acționările se împart în autonome, independente de sistemul de alimentare cu energie, și neautonome, dependente de sistemul de alimentare cu energie, alimentate de rețelele electrice industriale. Acționările autonome includ motoarele cu ardere internă (ICE) cu transmisie mecanică, hidraulică sau electrică. Acționările neautonome includ: motoare electrice curent continuu alimentat de rețele industriale de curent alternativ.
În conformitate cu cinematica instalației, unitatea poate avea trei versiuni principale: individuală, de grup și combinată sau mixtă.
Conducere individuală- fiecare actuator (troliu, pompa sau rotor) este actionat de motoare electrice sau motoare cu ardere interna independent unul de altul. Acest tip de acționare este utilizat mai pe scară largă cu motoarele electrice. La utilizarea acestuia, se obține o manevrabilitate ridicată în amenajarea și plasarea echipamentului de foraj pe baze în timpul instalării.
Conducere în grup- mai multe motoare sunt conectate printr-o transmisie însumată și antrenează mai multe actuatoare. Este folosit la motoarele cu ardere internă.
Unitate combinată- utilizarea unităților individuale și de grup într-o singură instalație. De exemplu, pompele sunt acționate de motoare individuale, în timp ce troliul și rotorul sunt acționate de un motor comun. În toate cazurile, caracteristicile sistemului de acţionare trebuie să satisfacă cel mai pe deplin caracteristicile cerute ale actuatoarelor.
Consumatorii de energie pentru instalațiile de foraj sunt:
în procesul de foraj - pompe de noroi, un rotor (în cazul forajului rotativ), dispozitive pentru pregătirea și curățarea fluidului de foraj din butași; compresor, pompă de apă etc.;
la coborârea și ridicarea șirului de țeavă - un troliu, un compresor, o pompă de apă și o cheie mecanizată.
Acționările sunt, de asemenea, împărțite în acționări principale (acționări ale troliului, pompe și rotor) și acționări auxiliare (acționări ale altor dispozitive și mecanisme ale instalației). Puterea consumata de dispozitivele auxiliare nu depaseste 10-15% din puterea consumata de echipamentul principal.
Caracteristici de flexibilitate- capacitatea motorului de acționare automată sau cu participarea operatorului în procesul de adaptare rapidă la modificările sarcinilor și vitezei de rotație ale actuatoarelor. Flexibilitatea caracteristicii depinde de coeficientul de adaptabilitate, de domeniul de reglare a frecvenței de rotație a arborilor de propulsie și de răspunsul la accelerație al motorului.
Factorul de flexibilitate caracteristicile este determinată de raportul dintre modificarea vitezei și abaterea cuplului de sarcină cauzată de aceasta. Este proporțional cu raportul de transmisie și invers proporțional cu factorul de suprasarcină.
ridica numită intensitatea implementării tranzitorii, adică timpul în care motorul și puterea de acționare răspund la schimbările de sarcină și modifică viteza.
Adaptabilitate- proprietatea propulsorului de a modifica cuplul si viteza in functie de momentul rezistentei. Autoadaptabilitate - proprietatea motorului de a se adapta la o sarcină externă. Adaptabilitate artificială - proprietatea transmisiilor de a adapta caracteristicile motorului la o modificare a sarcinii externe.
Echipament de etanșare a capului puțului
În prezent, la forarea puțurilor nu numai de explorare, ci și de producție, echipamentele de etanșare a capului de sondă sunt utilizate pe scară largă. Anterior, acest echipament era folosit în principal pentru controlul emisiilor de lichide și gaze în timpul AHRP. În legătură cu utilizarea fluidelor de foraj mai ușoare, presiunea din sondă în timpul procesului de foraj este reglată cu ajutorul unor dispozitive de prevenire. Cerințele pentru protecția mediului și a măruntaielor pământului s-au schimbat.
Pentru etanșarea capului sondei se folosesc trei tipuri de dispozitive de prevenire: berbec - surd sau traversant pentru a bloca complet orificiul sau spațiul inelar, dacă în puț există un șir de conducte; universal - pentru a închide gaura din puț, dacă conține vreo parte a șirului de foraj: încuietoare, țeavă, Kelly; rotativ - pentru etanșarea capului sondei cu o țeavă care se rotește în el sau o țeavă de conducere. Nici ram, nici dispozitivele universale de prevenire nu sunt proiectate pentru a roti sfoara dacă sunt complet închise.
BOP-uri Ram
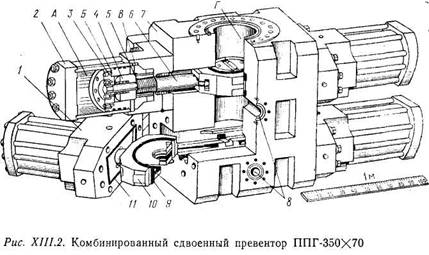
Piston auxiliar 4 se deplasează de asemenea spre dreapta, iar în poziția finală apasă inelul de blocare 5 și astfel fixează matrițele 10 în stare închisă, ceea ce exclude deschiderea lor spontană. Pentru a deschide o gaură G butoi, trebuie să mutați matrițele spre stânga. Pentru a face acest lucru, fluidul de control trebuie să fie furnizat sub presiune în cavitatea B, care mișcă pistonul auxiliar. 4 prin stoc 6 spre stânga și deschide zăvorul 5. Acest piston, ajungând la oprirea din pistonul principal 3, îl mută spre stânga, dezvăluind astfel zarurile. În acest caz, fluidul de control, situat în cavitatea £, este strecurat în sistemul de control.
Moare 10 prevenitoarele pot fi înlocuite în funcție de diametrul țevilor de etanșat. Capătul matrițelor din jurul circumferinței este sigilat cu o manșetă de cauciuc 9, un capac 1 - garnitura //. Fiecare dintre dispozitivele de prevenire este controlată independent, dar ambii berbeci ale fiecărui dispozitiv de prevenire funcționează simultan. găuri 8 în carcasa 7 sunt utilizate pentru a conecta dispozitivul de prevenire la colector. Capătul inferior al carcasei este atașat de flanșa capului sondei, iar la capătul superior este atașat un dispozitiv de prevenire universal.
După cum puteți vedea, un berbec BOP controlat hidraulic ar trebui să aibă două linii de control: una pentru a controla fixarea poziției berbecilor, a doua pentru a le muta. BOP-urile controlate hidraulic sunt utilizate în principal în forajele offshore. În unele cazuri, dispozitivul de prevenire inferior este echipat cu berbeci cu cuțite de forfecare pentru a tăia șirul țevii în puț.
Prevenitori universali
Preventorul universal este proiectat pentru a îmbunătăți fiabilitatea etanșării capului puțului. Elementul său principal de lucru este o etanșare elastică inelară puternică, care, atunci când dispozitivul de prevenire este deschis, permite trecerea șirului de foraj, iar atunci când dispozitivul de prevenire este închis, acesta este comprimat, drept urmare garnitura de cauciuc comprimă țeava (kelly). , blocare) și etanșează spațiul inelar dintre garnitura de foraj și carcasă . Elasticitatea garniturii de cauciuc face posibilă închiderea dispozitivului de prevenire pe țevi de diferite diametre, pe încuietori și gulere de foraj. Utilizarea dispozitivelor de prevenire universale face posibilă rotirea și plimbarea firului cu un spațiu inelar etanș.
Inelul O este comprimat fie prin forța hidraulică directă care acționează asupra elementului de etanșare, fie prin această forță care acționează asupra etanșării printr-un piston inelar special.
Prevenitoarele universale cu element de etanșare sferic și cu etanșare conică sunt fabricate de VZBT.
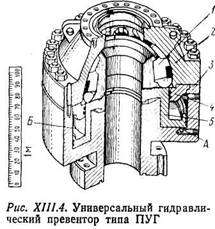
Când fluidul de lucru este alimentat sub pistonul 5 prin orificiul din corpul dispozitivului de prevenire, pistonul se mișcă în sus și comprimă etanșarea / în jurul sferei, astfel încât să se extindă spre centru și comprimă țeava în interiorul etanșării inelare. În acest caz, presiunea fluidului de foraj din puț va acționa asupra pistonului și va comprima etanșarea. Dacă nu există nicio coloană în puț, etanșarea acoperă complet gaura. Camera superioară B servește la deschiderea dispozitivului de prevenire. Când uleiul este injectat în el, pistonul se mișcă în jos, deplasând fluidul din camera A în conducta de scurgere.
Prevenitoare rotative
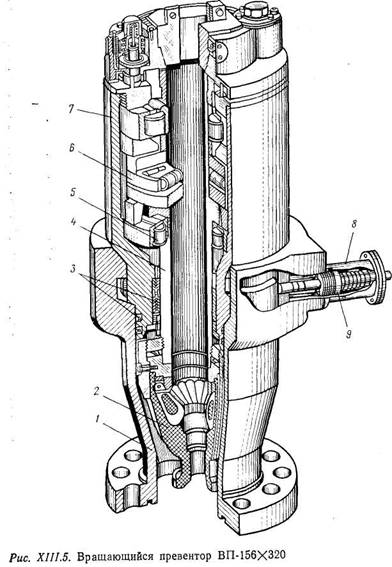
Un dispozitiv de prevenire rotativ este utilizat pentru a etanșa capul sondei în timpul forajului în timpul rotației și inversării garniturii de foraj, precum și în timpul declanșării și presiunii crescute în puț. Acest preventor etanșează țevile kelly, lock sau foraj, vă permite să ridicați, să coborâți sau să rotiți garnitura de foraj, foraj cu spălare inversă, cu nămoluri aerate, cu purjare cu agent gazos, cu un sistem de echilibru al presiunii hidrostatice pe formațiune, testarea formațiunilor în procesul de gaze arată.
II . Partea tehnologica
1. Forarea sondelor de petrol și gaze
Familiarizarea cu metodele de alimentare manuală a biților, găurire cu regulatorul de avans a biților, instruire în găurirea cu rotor.
Când bitul este alimentat în partea de jos, este necesar să se creeze o anumită sarcină asupra acestuia. Această operațiune se efectuează de pe consola perforatorului. Găuritorul, folosind așa-numitul poker, coboară unealta și apoi, treptat, foarte încet, descarcă greutatea din cârlig pe burghiu. Sarcina pe fir este determinată de indicatorul de greutate. Pe indicator, prețul diviziunii poate fi diferit. Când sistemul de deplasare este suspendat, dar cârligul nu este încărcat, indicatorul de greutate va afișa o valoare corespunzătoare greutății sistemului de deplasare.
WOB trebuie să fie egal cu cel mult 75% din greutatea șirului de foraj. De exemplu, există un aspect: 100 m de guler de foraj și 1000 m de țevi de foraj. Fie greutatea șirului UBT de 150 kN, iar greutatea șirului BT de 300 kN. Greutatea totală a BC în acest caz va fi de 450 kN. Aproximativ 2/3 din greutatea gulerului de foraj trebuie alimentată la sacrificare, adică. în acest caz 100 kN. Pentru a face acest lucru, sfoara este coborâtă fără probleme cu 9 m (lungimea țevii stivuitoare) până în jos. Momentul de contact al bitului cu fundul este determinat de indicatorul de greutate: săgeata arată scăderea greutății pe cârlig. După aceea, este necesar să eliberați troliul foarte încet și să încărcați treptat bitul până când săgeata de pe indicatorul de greutate arată 35 de tone. pe indicatorul de masă, oscilația săgeții poate să nu fie întotdeauna vizibilă. Acesta arată câte diviziuni a trecut săgeata de pe indicatorul de greutate, adică. 3 diviziuni Werner sunt egale cu 1 diviziune indicator de masă.
Rotoarele sunt folosite pentru a transfera rotația șirului de țevi de foraj în timpul forajului, pentru a-l menține în greutate în timpul operațiunilor de declanșare și a lucrărilor auxiliare.
Rotorul este o cutie de viteze care transmite rotația unei coloane suspendate vertical de la un arbore de transmisie orizontal. Cadrul rotorului primește și transmite la bază toate sarcinile care apar în timpul operațiunilor de forare și declanșare. Cavitatea internă a patului este o baie de ulei. La capătul exterior al arborelui rotorului, pe cheie, poate exista un pinion sau un semicuplaj al arborelui cardanic. La deșurubarea burghiei sau pentru a preveni rotirea garniturii de foraj din acțiunea unui moment inactiv, rotorul este blocat cu un zăvor sau un mecanism de blocare.Când rotația este transmisă rotorului de la motor prin troliu, rotorul turația se modifică cu ajutorul mecanismelor de transmisie ale troliului sau prin schimbarea roților dințate. Pentru a nu conecta munca troliului cu munca rotorului, în unele cazuri, la găurirea rotativă, se folosește o acționare individuală la rotor, adică nu este conectată cu troliul.
2 inserții sunt introduse în orificiul traversant al rotorului. Apoi, în funcție de diametrul țevilor, pe rotor sunt așezate pene corespunzătoare, care sunt atașate la patru paralele. Paralele, la rândul lor, sunt puse în mișcare cu ajutorul RCC (pene pneumatice ale rotorului), care sunt montate pe partea opusă arborelui rotorului. Folosind pedala, care se află pe consolă, găuritorul ridică sau coboară pene.
Când începe găurirea, penele sunt îndepărtate din rotor, eliberând astfel orificiul pătrat al căptușelilor. Apoi, așa-numitul kelbush este fixat în această gaură - o piuliță fixată mobil pe țeava principală, care se mișcă în sus și în jos de-a lungul ei. Mai departe, cu ajutorul transmisiei, se stabilesc turațiile necesare ale rotorului, iar acesta este condus de la consola mașinii de găurit.
Familiarizarea cu metodologia dezvoltării raționale a biților.
Pentru a lucra rațional bitul, este necesar să se îndeplinească rata de penetrare. Pe măsură ce gaura de fund se adâncește, unealta de tăiere a rocii se uzează și, pentru a preveni uzura din timp, este necesar să se respecte modul de forare.
Modul de foraj include rotorul sau motorul de foraj RPM, WOB și presiunea pompei (pe verticală). Deci, pentru dezvoltarea corectă a burghiului, sarcina pe acesta ar trebui să fie mai mare de 75% din greutatea șirului gulerului de foraj. Supraîncărcarea bitului poate duce la uzura prematură a acestuia sau ruperea conului, iar subîncărcarea poate duce la o scădere a pătrunderii. Viteza rotorului și presiunea pe verticală sunt stabilite în funcție de linia geologică și tehnică.
Pentru dezvoltarea rațională a bitului, este necesar să-l alimentați la fund fără rotație și să porniți rotațiile numai după contactul cu fundul. Dar înainte de a începe găurirea, este necesar să „introduceți” burghiul timp de 30-40 de minute pentru ca acesta să ruleze. În același timp, greutatea burghiului ar trebui să fie mică - aproximativ 3-5 tone. Când găuriți cu un turboburător sau cu un motor cu șurub, burghiul este alimentat în gaura de fund deja în rotație. În acest caz, puteți fie să opriți spălarea și să coborâți bitul în jos, fie, fără a opri spălarea, să încărcați treptat bitul la valoarea necesară.
Codarea uzurii bitului conic:
B - uzura armelor (cel puțin o coroană)
B1 - reducerea înălțimii dintelui cu 0,25%
B2 - reducerea înălțimii dinților cu 0,5%
B3 - reducerea înălțimii dinților cu 0,75%
B4 - uzura completa a dintilor
C - cip dentar în%
P - uzura suportului (cel putin o freza)
P1 - jocul radial al frezei față de axa trunionului pentru biți
diametru mai mic de 216 mm 0-2 mm; pentru biți mai mari decât
216 mm 0-4 mm
P2 - jocul radial al frezei față de axa trunionului pentru biți
diametru mai mic de 216 mm 2-5 mm; pentru biți mai mari decât
216 mm 4-8 mm
P3 - jocul radial al frezei față de axa trunionului pentru biți
diametru mai mic de 216 mm mai mult de 5 mm; pentru biți mai mari decât
216 mm peste 8 mm
P4 - distrugerea elementelor de rulare
K - blocarea tăietorilor (numărul acestora este indicat între paranteze)
D - reducerea diametrului bitului (mm)
A - uzură de urgență (numărul de tăietori și labe rămase este indicat între paranteze)
AB (A1) - rupere și lăsând partea superioară a conului în partea de jos
ASh (A2) - în defalcare și lăsând conul în partea de jos
AC (A3) - lăsând laba în jos
Cauzele uzurii anormale a conurilor:
1) Un număr mare de dinți rupti:
Alegere greșită a bitului
Intrare greșită
Viteză excesivă
Lucrări metalice
2) Uzură puternică a diametrului:
De mare viteză
Strângerea conurilor ca urmare a coborârii în trunchi cu un diametru redus
3) Eroziunea corpului conului:
Consum mare de lichid de spălare
4) Uzură excesivă a rulmenților:
Lipsa stabilizatorului deasupra burghiului sau între gulerele de foraj
De mare viteză
Timp de foraj mecanic semnificativ
5) Blocarea spatiilor inter-coroane in freze cu roca forata si faza solida:
Consum insuficient de pancreas
Dalta este concepută pentru formațiuni mai dure
Bitul a fost coborât în zona găurii de jos plină cu butași
6) Număr mare de dinți pierduți:
Eroziunea corpului conic
Timp de foraj mecanic semnificativ
Efectuarea lucrărilor de bază în timpul software-ului open source cu ajutorul echipamentelor speciale
Unitatea principală în implementarea deplasării este un drawwork, care este condus de o unitate de putere. Pentru o utilizare optimă a puterii în timpul ridicării cârligului cu sarcină variabilă, transmisiile de antrenare a troliului sau acționarea troliului trebuie să fie cu mai multe viteze. Troliul trebuie să treacă rapid de la viteze mari de ridicare la viteze mici și înapoi, asigurând pornirea planificată cu un timp minim petrecut în aceste operațiuni. În cazurile de lipire și strângere a firului, forța de tragere în timpul ridicării ar trebui să crească rapid. Vitezele de comutare pentru ridicarea coloanelor de diferite mase se efectuează periodic.
Troliurile și pneumobrancherele auxiliare sunt utilizate pentru a efectua lucrări de tragere a sarcinilor și de înșurubare-pe-înșurubare a țevilor în timpul SPO.
Spărgătoarele pneumatice sunt proiectate pentru a desface îmbinările sculelor ale țevilor de foraj. Pneumobrancherul este format dintr-un cilindru în care se mișcă un piston cu tijă. Cilindrul este închis la ambele capete cu capace, dintre care unul are o etanșare a tijei. Un cablu metalic este atașat de tijă pe partea opusă a pistonului, celălalt capăt al căruia este pus pe cheia mașinii. Sub acțiunea aerului comprimat, pistonul se mișcă și rotește cheia mașinii prin cablu. Forța maximă dezvoltată de cilindrul pneumatic la o presiune a aerului comprimat de 0,6 MPa este de 50...70 kN. Cursa pistonului (tijei) cilindrului pneumatic este de 740 ... 800 mm.
Complexul de mecanisme ASP este conceput pentru mecanizarea și automatizarea parțială a operațiunilor de declanșare. Oferă:
- combinarea în timp a ridicării și coborârii șirului de țevi și a liftului descărcat cu operațiunile de montare a suportului pe suport, scoaterea acestuia de pe suport, precum și înșurubarea sau înșurubarea suportului cu șirul de foraj;
- mecanizarea instalării lumânărilor pe sfeșnic și scoaterea lor în centru, precum și captarea sau eliberarea șirului de țevi de foraj de către un ascensor automat.
Mecanismele ASP includ: mecanism de ridicare (ridicarea și coborârea unei lumânări rotite separat); mecanism de prindere (capturarea și ținerea unei lumânări deșurubate în timpul ridicării, coborârii, transferarea acesteia de la rotor la sfeșnic și invers); mecanism de plasare (deplasarea lumânării din centrul puțului și înapoi); centralizator (ținând partea superioară a lumânării în centrul turnului în timpul înșurubarii și înșurubarii); ascensor automat (captarea și eliberarea automată a coloanei BT în timpul coborârii și ascensiunii); revistă și sfeșnic (ținând lumânările deșurubate în poziție verticală).
În activitatea unui complex de mecanisme precum ASP-ZM1, ASP-ZM4. ASP-ZM5 și ASP-ZM6 folosesc cheia AKB-ZM2 și mânerul pneumatic BO-700 (cu excepția ASP-ZM6, pentru care se folosește mânerul PKRBO-700).
Pregătirea țevii pentru târare, instalarea liftului pe rotor, scoaterea acesteia de pe rotor, așezarea țevilor pe pene
Înainte de a trage țevile către instalație, este necesar să se efectueze o inspecție vizuală a corpului țevii și a fileturilor. Pentru o analiză precisă, este chemată o echipă de detectori de defecte, care, folosind instrumente, determină adecvarea țevilor pentru utilizarea pe o instalație de foraj. În plus, este necesar, după caz, să curățați racordurile filetate ale țevilor și apoi să le lubrifiați cu unsoare sau unsoare de grafit. După aceea, conductele sunt livrate către podurile de recepție.
În timpul forajului, țevile de foraj sunt târâte una câte una de pe pasarele către rotor cu ajutorul unui troliu auxiliar. Apoi țeava livrată este înșurubată pe șnur, iar gaura de fund este adâncită și mai mult de lungimea țevii extinse.
Ridicarea și coborârea țevilor de foraj pentru a înlocui un burghiu uzat constă în aceleași operații repetate. Mai mult, utilajele includ operațiunile de ridicare a lumânării din puțuri și liftul gol. Toate celelalte operațiuni sunt manuale sau manuale care necesită un efort fizic mare. Acestea includ:
· la ridicare: aterizarea coloanei pe lift; deșurubarea conexiunii filetate; instalarea unei lumânări pe un sfeșnic; coborâre lift gol; transferul legăturilor la liftul încărcat și ridicarea coloanei la înălțimea lumânării;
· la coborâre: retragerea unei lumânări din spatele unui deget și dintr-un sfeșnic; înșurubarea unei lumânări pe o coloană; coborând sfoara în puț; aterizarea coloanei pe lift; transferul legăturilor către un lift gratuit. Dispozitivele de prindere și suspendare a coloanelor variază ca dimensiune și capacitatea de încărcare.
De obicei, acest echipament este produs pentru țevi de foraj cu dimensiunile de 60, 73, 89, 114, 127, 141, 169 mm cu o capacitate nominală de încărcare de 75, 125, 140, 170, 200, 250, 320 de tone. țevi cu diametrul de 194 până la 426 mm, pene în patru dimensiuni: 210, 273, 375 și 476 mm, concepute pentru capacități de ridicare de la 125 la 300 de tone.
Elevatorul este folosit pentru a capta și menține greutatea țevilor șirului de foraj (carcasa) în timpul operațiunilor de declanșare și a altor lucrări în instalația de foraj. Se folosesc diverse tipuri de ascensoare, care diferă ca mărime în funcție de diametrul țevilor de foraj sau tubaj, capacitatea de încărcare, utilizarea constructivă și materialul pentru fabricarea acestora. Liftul este suspendat de cârligul de ridicare cu ajutorul unor chingi.
Penele pentru țevi de foraj sunt folosite pentru a atârna unealta de foraj în masa rotorului. Ele sunt introduse în alezajul conic al rotorului. Utilizarea penelor accelerează lucrul la operațiunile de declanșare. Recent s-au folosit pe scară largă mânerele de pană automate cu antrenare pneumatică de tip PKR (în acest caz, penele sunt introduse în rotor nu manual, ci cu ajutorul unui antrenament special, care este controlat de consola găuritorului).
Pentru a coborî șirurile grele ale carcasei, se folosesc pene cu un corp nedespicat. Acestea sunt instalate pe plăcuțe speciale deasupra capului sondei. Pena constă dintr-un corp masiv care primește greutatea țevilor de carcasă. În interiorul corpului există matrițe concepute pentru a capta țevile de carcasă și a le menține în stare suspendată. Ridicarea și coborârea matrițelor se realizează prin rotirea mânerului într-o direcție sau alta în jurul panei, ceea ce se realizează prin prezența în corp a unor decupaje de corectare înclinate, de-a lungul cărora rolele matrițelor se rulează cu ajutorul unei pârghii.
Verificarea filetului de blocare, înșurubarea BT cu ajutorul cheilor bateriei, reatașarea și desfacerea conexiunilor de blocare cu ajutorul cheilor UMK
În procesul de SPO, este necesar să înșurubați și să deșurubați în mod repetat țevile. Pentru a simplifica aceste operațiuni, instalația de foraj este echipată cu echipamente speciale. Un instrument special este folosit pentru a alcătui și deșuruba țevile de foraj și țevile de carcasă. Diferite chei sunt folosite ca un astfel de instrument. Unele dintre ele sunt destinate înșurubarii, iar altele - pentru fixarea și detașarea conexiunilor filetate ale coloanei. În mod obișnuit, cheile ușoare de pre-machiaj sunt proiectate pentru încuietori cu un diametru, iar cheile de mașină grele pentru fixare și conexiuni fără filet sunt proiectate pentru două și uneori mai multe dimensiuni de țevi de foraj și încuietori.
O cheie cu lanț este folosită pentru a întoarce țevile manual. Se compune dintr-un maner si un lant cu dispozitiv de fixare. Pentru a captura țeava, lanțul se înfășoară în jurul ei și este fixat pe partea superioară a mânerului. Lucrul cu o cheie cu lanț necesită foarte mult timp, așa că se folosesc alte echipamente.
Clestul de foraj automat al bateriei este proiectat pentru insurubarea mecanizata si insurubarea tevilor. Panoul de comandă este situat la stația de foraj și este echipat cu două pârghii: unul dintre ele controlează mișcarea cheii în sine spre rotor și înapoi și mecanismul de prindere a țevilor, iar cu ajutorul celuilalt, țevile sunt înșurubate împreună. . AKB simplifică foarte mult procesul de software open source.
Operațiunile de fixare și desfacere a îmbinărilor filetate ale șirurilor de foraj și carcase se realizează cu două chei de mașină UMK; în timp ce o cheie (întârziere) este fixă, iar a doua (înșurubare) este mobilă. Cheile sunt suspendate în poziție orizontală. Pentru a face acest lucru, rolele metalice sunt întărite pe „degete” speciale lângă punți și prin ele se aruncă o frânghie de oțel sau un fir de frânghie. Un capăt al acestei frânghii este atașat de suportul pentru chei, iar celălalt capăt este atașat de o contragreutate care echilibrează cheia și facilitează deplasarea cheii în sus sau în jos.
La coborârea țevilor de foraj și a colțurilor de foraj în puț, conexiunile filetate trebuie strânse cu mașină și chei automate, controlând spațiul dintre elementele de legătură și observând, conform indicatorului de cuplu, valoarea cuplului admisibil stabilită de instrucțiunea curentă.
Inspecția și măsurarea BT și a gulerului, instalarea BT pe un sfeșnic, înșurubarea și deșurubarea dalților
Înainte de a începe forarea, este necesar să inspectați toate țevile situate pe instalația de foraj. O atenție deosebită trebuie acordată verificării conexiunilor filetate. Filetul de pe țevile de foraj se uzează în timpul funcționării, astfel încât lungimea filetului și diametrul acestuia trebuie măsurate periodic. Acest lucru se face cu ajutorul unei benzi de măsurare. Abaterile admise ale dimensiunilor filetului sunt de 3-4 mm. Se folosesc șabloane speciale pentru a verifica dimensiunea țevilor. Diametrul fiecărui șablon corespunde unui diametru specific de țeavă.
În procesul de adâncire a fundului găurii, șirul de foraj crește constant. Pentru a face acest lucru, țeava de foraj este târâtă de pe poduri cu ajutorul unui troliu auxiliar la rotor, este agățată de elevator și apoi înșurubată pe filetul țevii montate pe pene.
Când este necesar să ridicați sfoara, țevile sunt deșurubate cu lumânări pentru a reduce timpul de deplasare. În acest caz, este necesar să ridicați capătul superior al țevii deasupra mesei rotorului, să îl puneți pe pene și să îl fixați pe lift. Apoi coloana se ridică la înălțimea lumânării, se așează pe pene, lumânarea este deșurubată cu cheia bateriei, înfășurată cu degetul muncitorului călăreț și semimontat și așezată pe sfeșnic. După ce s-au efectuat operațiunile necesare (schimbarea biților, BHA), sforul este coborât cu lumânări până la adâncimea forată.
Înșurubarea și deșurubarea bitului con se face cu ajutorul unei cotiere. Dalta se instaleaza manual sau cu ajutorul unui troliu auxiliar in cotiera. În interiorul acestuia sunt 3 proeminențe care merg între freze. Apoi mandrina este plasată pe căptușelile rotorului, iar buricul este înșurubat pe gulerul de foraj sau sub. Bitul cu palete este montat pe rotor folosind un suport special, astfel încât să rămână un singur filet deasupra mesei, apoi este înșurubat pe țeavă.
Înroșirea bine
Spălarea puțurilor este partea principală a forajului. Cât de bine va fi adus puțul la adâncimea de proiectare depinde de formularea soluției corect selectate.
În practica forării puțurilor se folosesc diverse metode tehnologice pentru prepararea fluidelor de foraj.
Cea mai simplă diagramă de flux (Fig. 7.2) include un recipient pentru amestecarea componentelor fluidului de foraj 1, echipat cu agitatoare mecanice si hidraulice 9, mixer cu jet hidro 4, echipat cu o pâlnie de încărcare 5 si poarta glisanta 8, pompa centrifugă sau cu piston 2 (de obicei una dintre pompele de amplificare) și colectoare.
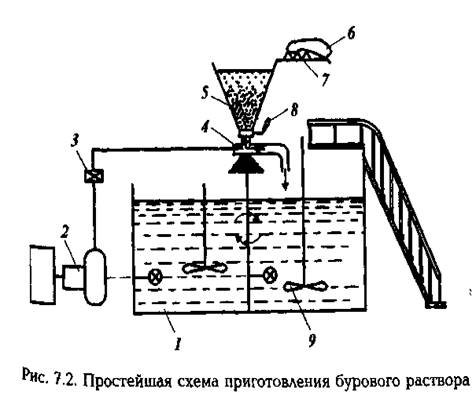
Conform acestei scheme, prepararea soluției se efectuează după cum urmează. În recipient 1 completați cantitatea calculată de mediu de dispersie (de obicei 20-30 m 3) și folosind pompa 2 prin conducta de refulare cu o supapă 3 este alimentat printr-un mixer hidro-ejector 4 într-o buclă închisă. Sac 6 s materialul pulverulent este transportat cu un lift sau transportor mobil la platforma rezervorului, de unde este alimentat la platforma 7 cu ajutorul a doi muncitori și mutat manual în pâlnia 5. mediu. Suspensia este drenată într-un recipient, unde este bine amestecată cu un amestecător mecanic sau hidraulic 9. Viteza de alimentare a materialului în camera de amestecare ejectoră este controlată de o poartă glisantă 8, iar vidul din cameră este controlat de un dispozitiv înlocuibil. duze din aliaj dur.
Principalul dezavantaj al tehnologiei descrise este mecanizarea slabă a muncii, furnizarea neuniformă a componentelor în zona de amestecare și controlul slab asupra procesului. Conform schemei descrise, viteza maximă de preparare a soluției nu depășește 40 m 3 /h.
În prezent, în practica casnică, tehnologia progresivă pentru prepararea soluțiilor de foraj din materiale sub formă de pulbere este utilizată pe scară largă. Tehnologia se bazează pe utilizarea echipamentelor disponibile comercial: o unitate de preparare a soluției (BPR), un mixer extern cu hidro-ejector, un dispersor hidraulic, un rezervor CS, mixere mecanice și hidraulice și o pompă cu piston.
Pentru curățarea fluidului de foraj de butași, se utilizează un complex de diverse dispozitive mecanice: site vibrante, separatoare de nămol cu hidrociclon (separatoare de nisip și nămol), separatoare, centrifuge. În plus, în cele mai nefavorabile condiții, înainte de curățarea de butași, noroiul de foraj este tratat cu reactivi floculanti, care fac posibilă creșterea eficienței dispozitivelor de curățare.
În ciuda faptului că sistemul de curățare este complex și costisitor, în majoritatea cazurilor utilizarea sa este rentabilă datorită creșterii semnificative a vitezei de foraj, reducerii costurilor de reglare a proprietăților fluidului de foraj, scăderii gradului de foraj. complicația sondei și satisfacerea cerințelor de protecție a mediului.
Ca parte a sistemului de circulație, dispozitivele trebuie instalate într-o secvență strictă. În acest caz, schema de trecere a soluției trebuie să corespundă următoarei lanțuri tehnologice: puț - separator de gaze - unitate de curățare a nămolului grosier (site vibratoare) - degazor - unitate de curățare a nămolului fin (separatoare de nisip și nămol, separator) - conținut și compoziție în fază solidă unitate de control (centrifugă, separator de argilă hidrociclon).
Desigur, în absența gazului în fluidul de foraj, etapele de degazare sunt excluse; atunci când se utilizează o soluție neponderată, de regulă, nu se folosesc separatoare de argilă și centrifuge; la curățarea fluidului greu de foraj, separatoarele de nămol cu hidrociclon (separatoare de nisip și nămol) sunt de obicei excluse. Cu alte cuvinte, fiecare echipament este proiectat pentru a îndeplini funcții destul de specifice și nu este universal pentru toate condițiile geologice și tehnice de foraj. Prin urmare, alegerea echipamentului și a tehnologiei pentru curățarea fluidului de foraj din butași se bazează pe condițiile specifice de forare a unui puț. Și pentru a face alegerea corectă, trebuie să cunoașteți capacitățile tehnologice și funcțiile de bază ale echipamentului.
BHA si controlul regimului de foraj pentru combaterea curburii spontane a sondei
Motive tehnice și tehnologice duc la curbura spontană a sondei datorită faptului că provoacă îndoirea părții inferioare a garniturii de foraj și nealinierea axei bitului față de centrul sondei. Pentru a exclude aceste procese sau pentru a reduce probabilitatea apariției lor, este necesar:
1. crește rigiditatea fundului garniturii de foraj;
2. exclude golurile dintre centralizatoare și peretele forajului;
3. reduce WOB;
4. în cazul forajului cu motoare de fund rotiţi periodic garnitura de foraj.
Pentru a îndeplini primele două condiții, este necesar să instalați cel puțin două centralizatoare de dimensiune completă: deasupra burghiului și pe corpul gulerului de foraj apropiat (sau pe RD). Instalarea a 2 - 3 centralizatoare de dimensiune completă permite creșterea rigidității BHA și reducerea șanselor de îndoire chiar și fără a reduce WOB.
În unele cazuri, ansamblurile pilot sunt utilizate atunci când puțul este forat în trepte: pilot - burghie cu diametru mic - prelungire - burghie - aleză - guler de foraj - garnitură de foraj. Este de dorit să se utilizeze gulere cu un diametru cât mai mare posibil. Acest lucru crește rigiditatea BHA și reduce golurile dintre țeavă și peretele găurii de foraj.
2. Familiarizarea cu găurirea cu tampon
Un grup de puțuri este un astfel de aranjament atunci când gurile sunt aproape una de alta pe aceeași platformă tehnologică, iar fundul puțurilor se află în nodurile rețelei de dezvoltare a rezervorului.
În prezent, majoritatea puțurilor de producție sunt forate în clustere. Acest lucru se explică prin faptul că forarea în cluster a zăcămintelor poate reduce semnificativ dimensiunea suprafețelor ocupate de foraj și apoi de producție de puțuri, drumuri, linii electrice și conducte.
Acest avantaj are o importanță deosebită în timpul construcției și exploatării puțurilor pe terenuri fertile, în rezervații, în tundra, unde stratul de suprafață perturbat al pământului este restabilit după câteva decenii, în zonele mlăștinoase, ceea ce complică și mărește foarte mult costul lucrări de construcție și instalare a instalațiilor de foraj și exploatare. Forarea cu pad este necesară și atunci când este necesară deschiderea zăcămintelor de petrol sub structuri industriale și civile, sub fundul râurilor și lacurilor, sub zona de raft de la țărm și pasaje supraterane. Un loc special îl ocupă construcția grupurilor de puțuri pe teritoriul Tyumen, Tomsk și alte regiuni din Siberia de Vest, ceea ce a făcut posibilă realizarea cu succes a construcției de puțuri de petrol și gaze pe insulele de rambleu într-o zonă îndepărtată, mlaștină și populată. regiune.
Amplasarea puțurilor în platforma sondei depinde de condițiile terenului și de mijloacele de comunicare propuse între platforma de puț și bază. Tufișurile care nu sunt conectate prin drumuri permanente de bază sunt considerate locale. În unele cazuri, tufișurile pot fi de bază atunci când sunt amplasate pe autostrăzi. Pe plăcuțele de puțuri locale, de regulă, acestea sunt aranjate sub formă de ventilator în toate direcțiile, ceea ce face posibilă existența unui număr maxim de puțuri pe un tampon de puț.
Echipamentele de foraj și auxiliare sunt montate astfel încât atunci când instalația de foraj este mutată de la o sondă la alta, pompele de foraj, gropile de recepție și o parte din echipamentul de curățare, tratare chimică și preparare a fluidului de spălare să rămână staționare până la finalizarea construcția tuturor (sau a unei părți) a puțurilor de pe această platformă de sondă.
Numărul de puțuri dintr-un grup poate varia de la 2 la 20-30 sau mai mult. Mai mult, cu cât sunt mai multe puțuri în pad, cu atât este mai mare abaterea fundurilor de la capete de sondă, lungimea sondei crește, lungimea sondei crește, ceea ce duce la o creștere a costului forării puțului. În plus, există pericolul de a întâlni trunchiuri. Prin urmare, devine necesar să se calculeze numărul necesar de puțuri dintr-un cluster.
În practica forajului cu platformă, principalul criteriu pentru determinarea numărului de puțuri dintr-un tampon este debitul total al sondei și factorul de gaz al petrolului. Acești indicatori determină pericolul de incendiu al unei puțuri în timpul curgerii deschise și depind de nivelul tehnic al echipamentului de stingere a incendiilor.
Cunoscând numărul aproximativ de puțuri din pad, aceștia procedează la construirea unui plan de pad. Un plan al sondei de sondă este o reprezentare schematică a proiecțiilor orizontale ale puțurilor tuturor puțurilor forate dintr-o zonă de sondă dată. Planul padului include un aspect al capetelor de sondă, secvența forării acestora, direcția de mișcare a mașinii, azimuturile de proiectare și decalajele găurilor de fund. Sarcina este finalizată prin construirea unei scheme de stup.
3. Rularea și cimentarea șirurilor de carcasă
După ce intervalul necesar de roci a fost forat, este necesar să coborâți șirul de tubaj în puț. Coarda de tubaj este folosită pentru a întări pereții puțului, pentru a izola straturile absorbante și acviferele.
Coarda de tub este alcătuită din țevi pe mufă, îmbinări filetate sau sudate fără mâneci și coborâte în puț secțiune cu secțiune sau într-o singură treaptă de la gura până la fund. Într-o singură etapă, sfoara este coborâtă în cazul unei stabilități suficiente a pereților puțului și al capacității de ridicare a sistemului de deplasare. La fixarea puțurilor adânci, trebuie utilizate conexiuni filetate sau sudate fără îmbinări OK.
OK intermediar sunt de mai multe tipuri:
1) solid - suprapunerea întregului sondă de la fund până la capul sondei, indiferent de suportul intervalului anterior;
2) garnituri - pentru fixarea doar a intervalului deschis al puțului cu suprapunerea fundului OK-ului anterior cu o anumită cantitate;
3) coloane secrete - QAP special, care servesc doar pentru a acoperi intervalul de complicații și nu au nicio legătură cu coloanele anterioare.
Executarea în secțiune a șirurilor de tubaj și fixarea puțurilor cu căptușeli au apărut, în primul rând, ca o soluție practică la problema rulării șirurilor de tubaj grele și, în al doilea rând, ca o soluție la problema simplificării proiectării puțurilor, reducerea diametrelor tubului, precum și ca goluri între sfori și pereții puțului, reducând consumul de metal și materiale de astupare.
Echipamentul tehnologic este folosit pentru cimentarea cu succes și pentru o coborâre mai eficientă a OK. Echipamentul include următoarele dispozitive: capete de cimentare, dopuri separatoare de cimentare, supape de reținere, saboți de coloană, duze de ghidare, centralizatoare, răzuitoare, turbulizatoare, duze de încălțăminte de 1,2-1,5 m lungime cu orificii de 20-30 mm în diametru în spirală, packere hidraulice inelare. de tip PDM, manșoane de cimentare în etape etc.
CAP DE CIMENTARE
Capetele de cimentare sunt proiectate pentru a crea o legătură strânsă între șirul de carcasă și liniile de injecție ale unităților de cimentare. Înălțimea capetelor de cimentare trebuie să permită amplasarea acestora în verigile de ridicare ale sistemului de rulare și, cu echipamente adecvate, utilizate pentru cimentare cu alezarea șirului de carcasă.
BUPURI DE CIMENTARE DE SEPARARE
Dopurile de stoarcere sunt concepute pentru a separa suspensia de ciment de fluidul de stoarcere atunci când este forțat în inelul puțurilor.Există modificări ale dopurilor, în care un filet pentru un dop este realizat în partea superioară a corpului pe partea interioară. de suprafață, fără de care acești dopuri pot fi utilizați ca dopuri de secțiune. Dop inferior este introdus în carcasă coloana chiar înainte de pomparea nămolului de ciment pentru a preveni amestecarea acestuia cu fluidul de foraj, iar dopul superior după întregul volum al nămolul de ciment a fost pompat. Canalul central din dopul inferior este blocat de o diafragmă de cauciuc, care se rupe la aterizarea pe „inelul de oprire” și deschide un canal pentru împingerea mortarului de ciment.
SUPPAPE DE CONTROL
Supapele de reținere TsKOD sunt proiectate pentru auto-umplerea continuă a șirului de tubaj cu fluid de foraj atunci când acesta este coborât în puț, precum și pentru a preveni returul nămolului de ciment din interior și pentru a opri dopul de cimentare de separare. Supapele de tip TsKOD sunt coborâte în puț cu un șir de carcasă fără o bilă de închidere, care este pompat în șir după ce este coborât la o adâncime predeterminată. Bila, care trece prin șaibe despicate și o diafragmă, ocupă o pozitia de lucru. diametrul interior care este mai mic decât diametrul bilei, aceasta din urmă este aruncată în șir înainte de a conecta țevile de foraj la secțiune. În acest caz, auto-umplerea șirului cu lichid este exclusă, iar atunci când coborâți șirul, este necesar să adăugați fluid de foraj la acesta în conformitate cu cerințele planului de lucru. Partea superioară a supapei are o suprafață internă de capăt de susținere care acționează ca un „inel de oprire” pentru a opri dopul de separare de ciment. În acest caz, nu este necesară instalarea inelelor de împingere.
PANTOFI DE COLONA
Pantofii de coloană sunt utilizați pentru a echipa partea inferioară a șirurilor de tubaj realizate din țevi cu un diametru de 114-508 mm și sunt proiectate pentru a ghida șirurile de-a lungul sondei și pentru a le proteja de deteriorarea în timpul coborârii în procesul de tubare a puțurilor de petrol și gaz la fundul găurii. temperaturi de până la 250 °C.
CENTRATORI
Centralizatoarele sunt proiectate pentru a asigura plasarea concentrică a șirului de tubaj în puț pentru a obține izolarea de înaltă calitate a formațiunilor în timpul cimentării. În plus, facilitează mersul șirului de tubaj prin reducerea forțelor de frecare dintre șir și pereții sondei, contribuie la creșterea gradului de deplasare a fluidului de foraj de către noroiul de ciment din cauza unor turbulențe a fluxurilor în zona de instalare a acestora, facilitează lucrul de agățare a corzilor ascunse și de andocare a secțiunilor datorită concentrării capetelor lor superioare în puț.
- RĂZUITOR
Racletele sunt folosite pentru spargerea turtei de argilă de pe pereții puțului pentru a îmbunătăți aderența nămolului de ciment la rocă, mai ales la cimentarea puțurilor cu alezare.
În timpul coborârii puțului, poate fi necesară spălarea puțului. În acest caz, un sub înșurubat este înșurubat pe kelly cu un filet de blocare în partea de sus și un filet trapezoidal în partea de jos. Apoi, când operațiunile necesare sunt finalizate, un cap de cimentare este înșurubat pe carcasă.
După rularea sondei, fluidul de foraj rămâne încă în puț. Pentru a-l scoate din butoi, se folosește un lichid tampon. Este pompat prin capul de cimentare. Apoi cantitatea estimată de ciment este pompată în coloană. După aceea, un fluid de deplasare este furnizat în spațiul din interiorul conductei pentru ca cimentul să se ridice la înălțimea de proiectare. În același timp, dopul este scos din dispozitivul de reținere și este transportat în jos de fluidul de deplasare. Aterizarea unui dop pe inelul de oprire al supapei de reținere, provocând o creștere a presiunii asupra pompei, semnalează sfârșitul procesului de cimentare.
Durata de întărire a mortarelor de ciment pentru conductoare este stabilită la 16 ore, iar pentru șirurile intermediare și de producție - 24 ore.Durata de întărire a diferitelor amestecuri de ciment (bentonită, zgură etc.) este stabilită în funcție de datele preliminare ale acestora. test, ținând cont de temperatura din sondă.
Procesul de cimentare a puțurilor este realizat de un complex de echipamente speciale, care este plasat în conformitate cu o schemă dezvoltată anterior.
Unitățile de cimentare sunt proiectate pentru a injecta suspensia de ciment și fluidul de deplasare în puț, precum și pentru a furniza fluidul de închidere dispozitivului de amestecare în timpul preparării soluției. În plus, sunt folosite pentru spălarea și stoarcerea dopurilor de nisip, testarea presiunii țevilor, coloanelor, colectoarelor, amestecării hidraulice a șlamului etc.
Mașinile de amestecare a cimentului sunt concepute pentru prepararea mortarelor de ciment pentru cimentarea puțurilor, diverse amestecuri de astupare; pot fi folosite pentru prepararea fluidelor de foraj normale și ponderate din pulberi de argilă.
În conformitate cu scopul și natura lucrării, mașinile de amestecare sunt montate pe mașini sau remorci.Componentele principale ale mașinilor de amestecare sunt un buncăr, un mecanism de încărcare și descărcare și un dispozitiv de amestecare pentru prepararea soluțiilor.
4. Deschiderea și testarea orizonturilor petroliere
Forarea sondei se termină cu deschiderea rezervorului de petrol, adică. comunicarea rezervorului de petrol cu sonda. Această etapă este foarte responsabilă din mai multe motive. Amestecul de petrol și gaz din rezervor este sub presiune ridicată, a cărui valoare poate fi necunoscută în prealabil. La o presiune care depășește presiunea coloanei de lichid care umple puțul, lichidul poate fi ejectat din sondă și are loc o curgere deschisă. Pătrunderea fluidului de spălare (în cele mai multe cazuri este o soluție de argilă) în rezervorul de ulei își înfundă canalele, afectând fluxul de petrol în puț.
Erupțiile pot fi evitate prin instalarea de dispozitive de prevenire la capul sondei sau prin utilizarea unui fluid de spălare cu densitate mare. Prevenirea pătrunderii soluției în rezervorul de ulei se realizează prin introducerea diferitelor componente în soluție, care sunt similare ca proprietăți cu fluidul din rezervor, de exemplu, emulsii pe bază de ulei.
Deoarece după deschiderea rezervorului de ulei, șirul de tub este coborât în puț și cimentat, blocând astfel și rezervorul de petrol, devine necesară redeschiderea rezervorului. Acest lucru se realizează prin tragerea prin coloană în intervalul de formare cu perforatoare. Ele sunt coborâte în fântână pe o frânghie de către un serviciu geofizic.
În prezent, mai multe metode de perforare a puțurilor au fost stăpânite și sunt utilizate:
1) Perforarea glonțului
Perforarea cu glonț a puțurilor constă în coborârea în puț pe un cablu de dispozitive speciale - perforatoare, în corpul cărora sunt construite încărcături de pulbere cu gloanțe. Primind un impuls electric de la suprafață, încărcăturile explodează, dând gloanțelor viteză mare și putere mare de penetrare. Provoacă distrugerea metalului coloanei și a inelului de ciment. Numărul de găuri din coloană și locația lor de-a lungul grosimii formațiunii sunt calculate în avans, prin urmare, uneori, o ghirlandă de perforatoare este coborâtă.
2) Perforarea torpilelor
Perforarea torpilelor este similară în principiu cu perforarea glonțului, doar greutatea încărcăturii este crescută și butoaiele orizontale sunt utilizate în perforator.
3) Perforarea cumulativă
Perforarea cumulativă - formarea de găuri datorită mișcării direcționate a unui jet de sarcini fierbinți care iese din perforator cu o viteză de 6 ... 8 km/s sub o presiune de 20 ... 30 GPa. În acest caz, se formează un canal cu o adâncime de până la 350 mm și un diametru de 8 ... 14 mm. Grosimea maximă a formațiunii, deschisă de un perforator cumulativ pentru coborâre este de până la 30 m, cu o torpilă - până la 1 m, cu un glonț - până la 2,5 m. Cantitatea de încărcare de pulbere - până la 50 g.
4) Perforare hidro-sablare
La folosirea perforarii cu jet de nisip hidro, se formeaza gauri in coloana datorita actiunii abrazive a amestecului nisip-lichid care curge cu o viteza de pana la 300 m/s din duzele calibrate la o presiune de 15...30 MPa. .
Dezvoltarea sondelor de petrol este un ansamblu de lucrari efectuate dupa forare, cu scopul de a provoca curgerea petrolului din rezervor in put. Faptul este că în procesul de deschidere, așa cum am menționat mai devreme, este posibil ca fluidul de foraj și apa să pătrundă în rezervor, care înfundă porii rezervorului și împinge uleiul departe de puț. Prin urmare, afluxul spontan de petrol în puț nu este întotdeauna posibil. În astfel de cazuri, ei recurg la un apel de aflux artificial, care constă în efectuarea de lucrări speciale.
Afluxul poate fi cauzat de înlocuirea unui fluid cu densitate mai mare în sondă cu un fluid cu densitate mai mică. În acest caz, presiunea exercitată de coloana de lichid asupra formațiunii scade și astfel se produce afluxul de petrol din puț. Această metodă este simplă și economică, dar eficientă în cazul contaminării slabe a formațiunii.
Dacă înlocuirea soluției cu apă nu aduce rezultate, atunci afluxul este cauzat folosind un compresor. Aerul comprimat de un compresor este introdus în butoi. În același timp, este posibilă împingerea coloanei de lichid departe de sabotul tubulaturii, reducând astfel contrapresiunea asupra formațiunii la valori semnificative. În unele cazuri, poate fi eficient să se furnizeze periodic aer printr-un compresor și lichid printr-o unitate de pompă, creând explozii succesive de aer. Numărul de astfel de porțiuni de gaz poate fi de mai multe, iar acestea, extinzându-se, aruncă lichidul din butoi. Pentru a crește eficiența deplasării de-a lungul lungimii șirului de țevi, sunt instalate supape de pornire-găuri prin care aerul comprimat, atunci când se deplasează prin spațiul țevilor, intră în KZP și începe să ridice lichid atât în inel, cât și în tubulatura .
Fluxul de intrare poate fi cauzat și de metoda de tamponare. Metoda constă în introducerea unui tampon cu piston special echipat cu o supapă de reținere în tub. Deplasându-se în jos, pistonul trece fluidul prin el însuși, atunci când se ridică, supapa se închide și întreaga coloană de fluid care se află deasupra este forțată să se ridice cu pistonul și apoi ejectată din puț. Deoarece coloana de lichid ridicată poate fi mare (până la 1000 m), căderea de presiune asupra formațiunii poate fi semnificativă. Procesul de tamponare poate fi repetat de multe ori, ceea ce permite o reducere semnificativa a presiunii.
Când tubulatura nu a fost încă introdusă în puț, fluxul de intrare poate fi cauzat de metoda imploziei. Dacă un vas umplut cu aer sub presiune este coborât în puț, atunci comunicați instantaneu acest vas cu sonda, atunci aerul eliberat se va muta din zona de înaltă presiune în zona de joasă presiune, antrenând lichidul și creând astfel o presiune redusă asupra formare. Un efect similar poate fi obținut dacă lucrările de pompare și compresoare golite anterior de lichid sunt coborâte în puț și fluidul de sondă este trecut instantaneu în ele. În acest caz, contrapresiunea asupra formațiunii va scădea și fluxul de fluid din formațiune va crește. Stimularea influxului este însoțită de îndepărtarea impurităților mecanice aduse acolo din rezervor, adică. curatarea formatiilor.
5. Lucrări de urgență în fântână
Pentru lucrări de urgență, se folosește un instrument de pescuit. Designul instrumentului de pescuit este foarte divers. Cu toate acestea, conform principiului capturii, acestea pot fi împărțite în trei grupuri principale:
a) Unelte plate de pescuit care funcționează pe principiul înghesuirii unui obiect în exteriorul sau în interiorul prindetorului;
b) Unelte de pescuit cu rifle, care funcționează pe principiul tăierii unui fir pe un obiect cu înșurubarea simultană a unui prindetor pe acesta;
c) Alt instrument.
Luați în considerare câteva tipuri de instrumente de pescuit.
Țeava externă este proiectată pentru a capta țevi, tije sau alte obiecte din puț de corp sau de manșon. Este un mâner de pieptene despicat plasat în corp și fixat pe țevi. Obiectul de prins este acoperit cu o prindere, care, la intrarea în sus, mărește diametrul găurii, trecând obiectul în prindere. Când este întins, alunecarea coboară, iar dinții îi taie corpul obiectului, înfipându-l în dispozitiv de prindere.
Sulița interioară este proiectată pentru a fi coborâtă în conducta de prindere. Este format dintr-un corp pe care este fixată o placă, conectată cu o tijă și un inel mobil. Corpul este introdus în conducta de prindere, în timp ce matrița se ridică, reducând diametrul captatorului și creând condiții de intrare. Când este întins, matrița coboară, mărind diametrul corpului de captare și blocând țeava.
Depășirea operațională este destinată prinderii țevilor sau tijelor prin cuplare cu ajutorul unor arcuri plate fixate pe suprafața interioară a corpului. Când se apropie de un obiect, arcurile diverg, trecându-l în interiorul receptorului și apoi converg.
Supapa pentru prinderea tijelor este folosită pentru prinderea tijelor de ambreiaj. Este alcătuit dintr-un corp în care sunt fixate matrițele derulante cu arc. Molele se deschid, trecând pe lângă obiect și apoi converg.
O freză cu dinți interiori este folosită pentru a freza capetele superioare ale țevilor sau tijelor de urgență pentru a putea funcționa apoi ca dispozitive de prindere de siguranță. Este format dintr-un corp în care sunt tăiați dinții longitudinali.
Robinetul operațional este proiectat pentru pescuit prin filetul interior al unei țevi sau cuplaj. Este format dintr-un corp, pe care există un fir în partea sa trunchiată. Poate fi feliat pe un articol care poate fi prins și apoi prins.
Clopotul este conceput pentru a prinde țeava de filetul exterior. Clopotul este o țeavă de ramură, pe suprafața interioară a căreia este tăiat un fir de blocare. Lungimea firului este de aproximativ 35 cm.
6. Eliminarea motorinei și a emisiilor
Există două metode:
metoda presiunii echilibrate a rezervorului
Când manifestarea este eliminată prin prima metodă, presiunea de fund este menținută puțin mai mare decât presiunea de formare pe tot parcursul procesului. În acest caz, fluxul de fluid se va opri până la amortizarea completă.
Există patru moduri de a implementa această metodă:
1) metoda de ucidere continuă a puțurilor: procesul de spălare și ucidere
începe să conducă imediat pe o soluție cu o densitate necesară pentru a efectua
condiţii - R zab > R rezervor. Cu această metodă, cea mai mică
presiunea, prin urmare, este cea mai sigură. Cu toate acestea, pentru implementarea sa
este necesar să existe o aprovizionare adecvată cu agent de greutate și preparate instant
noroi de foraj.
2) Metoda de așteptare a ponderării: după depistare manifestările sunt închise
bine şi se procedează la prepararea unei soluţii de densitatea necesară şi
volumul necesar. În timp ce pregătiți soluția, păstrați presiune constantă V
țevi de foraj, care asigură o presiune constantă a rezervorului în timpul ascensiunii
pachete de fluide. Dezavantajul acestei metode este nevoia de corectare
controlul presiunii pachetului plutitor de fluid, adică, astfel încât presiunea să nu o facă
a depășit echipamentul permis și este, de asemenea, posibil să lipiți forajul
instrument, deoarece puțul rămâne fără circulație. Avantajul acestei metode
fata de precedenta este ca putem prepara o solutie a acesteia
densitatea, precum și cu această metodă, cel mai mic maxim
presiune, de când gazul nu se apropiase încă de gură și a început soluția grea
umpleți KZP, deschidem din ce în ce mai mult sufocul, prin urmare,
pachetul de gaz se întinde mai mult și pierde presiunea când se apropie de gură.
3) Metoda de ucidere în două etape a puțului. În prima etapă, este
prin spălarea fluidului din puţ pe aceeaşi soluţie pe care s-a obţinut manifestarea.
În același timp, încep să pregătească o soluție cu o densitate necesară pentru
bine uciderea. În a doua etapă a uciderii, se efectuează injecția în puț
soluție ponderată. Această metodă este mai simplă decât precedentele două, relativ
sigur, dar în timpul implementării sale se creează cele mai mari presiuni în
bine.
4) Metoda extinsă în două etape. În prima etapă cu contrapresiune
spălarea fluidului de puț de intrare se efectuează pe aceeași soluție, pe care a fost obținută manifestarea. După ce fluidul de formare este spălat, fără a opri circulația, densitatea soluției circulante este crescută la densitatea necesară și astfel formarea în curs de dezvoltare este ucisă. Această metodă este utilizată în absența recipientelor necesare pentru prepararea soluției.
metoda de ucidere pas cu pas:
Se recurge la utilizarea acestei metode atunci când, la utilizarea metodelor anterioare, apar presiuni care depășesc presiunea admisă la capul sondei.
Bibliografie
1. Korshak A.A. Shammazov A.M./Fundamentals of oil and gaz business
2. Echipamente petroliere. Director.
3. Ilsky A.L. Shmidt A.P./Mașini și mecanisme de găurit
4. Popov A.N. Spivak A.I./Tehnologia forării puțurilor de petrol și gaze
1. O scurtă istorie a dezvoltării forajului
Pe baza descoperirilor și cercetărilor arheologice, s-a stabilit că în urmă cu aproximativ 25 de mii de ani, omul primitiv a făcut găuri în ele pentru atașarea mânerelor la fabricarea diferitelor unelte. Un burghiu din silex a servit ca unealtă de lucru.
ÎN Egiptul antic găurirea rotativă (forajul) a fost folosită la construcția piramidelor în urmă cu aproximativ 6000 de ani.
Primele rapoarte ale chinezilor fântâni pentru extragerea apei si a saramurilor sunt cuprinse in lucrarile filozofului Confucius, scrise in jurul anului 600 i.Hr. Sondele au fost construite folosind foraj percutant și au atins o adâncime de 900 m. Acest lucru indică faptul că înainte de aceasta, tehnica de foraj se dezvoltase de cel puțin câteva sute de ani. Uneori, în timpul forajului, chinezii dădeau peste petrol și gaze. Deci în 221 ... 263 de ani. ANUNȚ în Sichuan, gazul era extras din puțuri cu o adâncime de aproximativ 240 m, care era folosit pentru evaporarea sării.
Dovezile documentare ale tehnicilor de foraj în China sunt rare. Cu toate acestea, judecând după pictura chineză veche, basoreliefuri, tapiserii, panouri și broderii pe mătase, această tehnică se afla într-un stadiu destul de înalt de dezvoltare.
Forarea primelor puțuri din Rusia datează din secolul al IX-lea și este asociată cu extracția de soluții comune de sare din zona Staraya Russa. Exploatarea sării a fost foarte dezvoltată în secolele XV..XVII, dovadă fiind urmele descoperite de foraje în vecinătatea orașului Solikamsk. Adâncimea lor a ajuns la 100 m, cu diametrul puțului inițial de până la 1 m.
Pereții fântânilor se prăbușeau adesea. Prin urmare, pentru fixarea lor s-au folosit fie trunchiuri de copaci goale, fie țevi țesute din scoarță de salcie. La sfârşitul secolului al XIX-lea. pereții fântânilor au început să fie fixați cu țevi de fier. Au fost îndoite din tablă și nituite. La adâncirea puțului, țevile au fost avansate după instrumentul de foraj (bit); pentru aceasta au fost realizate cu un diametru mai mic decat cele anterioare. Aceste conducte au fost numite ulterior carcasă. Designul lor a fost îmbunătățit în timp: în loc să fie nituite, au devenit fără sudură, cu capete filetate.
Primul puț din Statele Unite a fost forat pentru extracția saramură lângă orașul Charleston din Virginia de Vest în 1806. Kentucky a găsit accidental ulei.
Prima mențiune despre utilizarea forajului pentru explorarea petrolului datează din anii 30 ai secolului al XIX-lea. Pe Taman, înainte de a săpa puțuri de petrol, au efectuat recunoașteri preliminare cu un burghiu. Martorul ocular a lăsat următoarea descriere: „Când plănuiesc să sape o fântână într-un loc nou, mai întâi încearcă pământul cu un burghiu, împingându-l înăuntru și adăugând puțină apă, ca să intre mai ușor și după ce îl scot, va fi ulei, atunci în acest loc încep să sape o groapă patruunghiulară”.
În decembrie 1844, un membru al Consiliului Administrației Principale a Teritoriului Transcaucazian V.N. Semyonov a trimis un raport conducerii sale, unde a scris despre necesitatea... aprofundării unor puțuri prin intermediul unui foraj... și reexplorării petrolului și prin intermediul unui foraj între puțurile Balakhani, Baibat și Kabristan. După cum V.N. Semenov, această idee i-a fost sugerată de managerul câmpurilor de petrol și sare din Baku și Shirvan, inginer minier N.I. Voskoboynikov. În 1846, Ministerul de Finanțe a alocat fondurile necesare și au început forajele. Rezultatele forajului sunt menționate în memoriul guvernatorului Caucazului, contele Vorontșov, din 14 iulie 1848: „... s-a forat un puț în Bibi-Heybat, în care s-a găsit petrol”. Era primul puț de petrol din lume!
Cu puțin timp înainte de aceasta, în 1846, inginerul francez Fauvel a propus o metodă de curățare continuă a puțurilor - lor spălat. Esența metodei a fost că apa era pompată de la suprafața pământului prin țevi goale în fântână, ducând bucăți de rocă în sus. Această metodă a căpătat recunoaștere foarte repede, deoarece. nu a necesitat oprirea forajului.
Prima sondă de petrol din Statele Unite a fost forată în 1859. Acest lucru a fost făcut în zona Titesville, Pennsylvania de E. Drake, care a lucrat la instrucțiuni de la Seneca Oil Company. După două luni de muncă continuă, muncitorii lui E. Drake au reușit să foreze un puț de doar 22 m adâncime, dar tot a dat petrol. Până de curând, această fântână era considerată prima din lume, însă documentele constatate despre lucrarea condusă de V.N. Semenov a restabilit justiția istorică.
Multe țări atribuie nașterea industriei lor petroliere forării primului puț care a produs petrol comercial. Deci, în România, numărătoarea inversă se face din 1857, în Canada - din 1858, în Venezuela - din 1863. În Rusia, multă vreme s-a crezut că primul puț de petrol a fost forat în 1864 în Kuban de pe maluri. a fluviului. Kudako sub conducerea colonelului A.N. Novosiltsev. Prin urmare, în 1964, în țara noastră a fost sărbătorită solemn cea de-a 100-a aniversare a industriei petroliere autohtone, iar de atunci în fiecare an se sărbătorește „Ziua lucrătorului în industria petrolului și gazelor”.
Numărul puțurilor forate în câmpurile petroliere la sfârșitul secolului al XIX-lea a crescut rapid. Deci, în Baku în 1873 erau 17, în 1885 - 165, în 1890 - 356, în 1895 - 604, apoi în 1901 - 1740. În același timp, adâncimea puțurilor de petrol a crescut semnificativ. Dacă în 1872 era de 55 ... 65 m, atunci în 1883 - 105 ... 125 m, iar la sfârşitul XIX-lea V. a ajuns la 425...530 m.
La sfârşitul anilor '80. a secolului trecut lângă New Orleans (Louisiana, SUA) a fost aplicată foraj rotativ pentru ulei cu spălare a puțurilor cu soluție de argilă. În Rusia, forajul rotativ cu spălare a fost folosit pentru prima dată în apropierea orașului Grozny în 1902, iar petrolul a fost găsit la o adâncime de 345 m.
Inițial, găurirea rotativă a fost efectuată prin rotirea burghiului împreună cu întreaga garnitură de foraj direct de la suprafață. Cu toate acestea, la o adâncime mare de puțuri, greutatea acestei coloane este foarte mare. Prin urmare, în secolul al XIX-lea primele propuneri de creație motoare de fund, acestea. motoare plasate în partea inferioară a țevilor de foraj direct deasupra burghiului. Majoritatea au rămas nerealizate.
Pentru prima dată în practica mondială, un inginer sovietic (mai târziu membru corespondent al Academiei de Științe a URSS) M.A. Kapelyushnikov în 1922 a fost inventat turbodrill, care era o turbină hidraulică cu o singură treaptă cu angrenaj planetar. Turbina era antrenată de lichidul de spălare. În 1935...1939. designul turboforurului a fost îmbunătățit de un grup de oameni de știință condus de P.P. Shumilova. Turbodrillul propus de ei este o turbină în mai multe trepte fără cutie de viteze.
În 1899, a fost brevetat în Rusia Bormasina electrica, care este un motor electric conectat la o daltă și suspendat pe o frânghie. Designul modern al burghiului electric a fost dezvoltat în 1938 de inginerii sovietici A.P. Ostrovsky și N.V. Aleksandrov și deja în 1940 primul puț a fost forat cu un burghiu electric.
În 1897, în Oceanul Pacific, în zona de aproximativ. Somerland (California, SUA) a fost implementat pentru prima dată foraj marin.În țara noastră, primul puț offshore a fost forat în 1925 în Golful Ilici (lângă Baku) pe o insulă creată artificial. În 1934 N.S. Timofeev despre despre. Artem în Marea Caspică a fost efectuată forarea puțurilor,în care mai multe puţuri (uneori mai mult de 20) sunt forate dintr-un loc comun. Ulterior, această metodă a devenit utilizată pe scară largă în forajul în spații restrânse (printre mlaștini, platforme de foraj offshore etc.).
De la începutul anilor 60, pentru a studia structura profundă a Pământului, lumea a început să folosească foraj ultra-profund.
2. Conceptul de fântână
Foraj- acesta este procesul de construire a unui puț prin distrugerea pietrelor. bine numită mină de secțiune circulară, construită fără acces la ea pentru oameni, în care lungimea este de multe ori mai mare decât diametrul.
Vârful fântânii se numește gură, fund - sacrificare, suprafata laterala - pereteși spațiul delimitat de perete - sondă. Lungimea bine este distanța de la gură până la fund de-a lungul axei trunchiului și adâncime este proiecția lungimii pe axa verticală. Lungimea și adâncimea sunt numeric egale numai pentru puțurile verticale. Cu toate acestea, ele nu coincid pentru sondele deviate și deviate.
Elementele de proiectare ale puțului sunt prezentate în fig. 1. Secțiunea inițială eu se numesc fântâni direcţie. Deoarece capul sondei se află în zona de roci ușor erodate, acesta trebuie consolidat. În acest sens, direcția se efectuează după cum urmează. În primul rând, se forează o groapă - un puț până la adâncimea rocilor stabile (4 ... 8 m). Apoi, în ea este instalată o țeavă cu lungimea și diametrul necesar, iar spațiul dintre pereții gropii și țeavă este umplut cu moloz și turnat cu mortar de ciment 2.
Orez. 1. Design bine:
Secțiunile din aval ale puțului sunt cilindrice. Imediat în spatele direcției, o secțiune este forată la o adâncime de 50 până la 400 m cu un diametru de până la 900 mm. Această secțiune a puțului este fixată cu țeava de carcasa 1 (formată din țevi de oțel înșurubate), care se numește dirijor II.
Spațiul inelar al conductorului este cimentat. Cu ajutorul unui conductor se izolează roci instabile, moi și fracturate, care complică procesul de foraj.
După instalarea unui conductor, nu este întotdeauna posibil să forați o sondă până la adâncimea de proiectare din cauza trecerii unor noi orizonturi complicate sau din cauza necesității de a acoperi formațiuni productive care nu sunt planificate a fi exploatate de această sondă. În astfel de cazuri, o altă coloană este instalată și cimentată. III, numit intermediar. Dacă formațiunea productivă pentru care se intenționează a fi dezvoltat puțul este foarte adâncă, atunci numărul coloanelor intermediare poate fi mai mare de unul.
Ultimul complot IV repar fântânile coloana operațională. Este proiectat pentru a ridica petrolul și gazul de la fund la capul sondei sau pentru a injecta apă (gaz) în formațiunea productivă pentru a menține presiunea în aceasta. Pentru a evita scurgerile de petrol și gaze V orizonturile supraiacente, iar apa în formațiuni productive, spațiul dintre peretele carcasei de producție și peretele puțului este umplut cu mortar de ciment.
Pentru extragerea petrolului și a gazelor din rezervoare, se folosesc diverse metode de deschidere și echipamente de fund. În majoritatea cazurilor, în partea inferioară a firului de producție situat în formațiunea productivă, o serie de găuri 4 sunt perforate (perforate) în peretele țevilor de carcasă și al mantalei de ciment.
În roci stabile, zona de fund a puțului este echipată cu diverse filtre și nu este cimentată, sau șirul de tubaj este coborât doar până la vârful formațiunii productive, iar forarea și funcționarea acesteia se efectuează fără fixarea sondei.
Capul sondei, în funcție de destinația sa, este echipat cu fitinguri (cap de coloană, supape, cruce etc.).
La căutarea, explorarea și dezvoltarea zăcămintelor de petrol și gaze, sunt forate puțuri de referință, parametrice, structurale, de prospectare, explorare, producție, injecție, observare și alte sonde.
puţuri de referinţă sunt așezate în zone neexplorate prin foraj și servesc la studiul compoziției și vechii rocilor care le compun.
Sonde parametrice sunt așezate în zone relativ studiate pentru a clarifica structura lor geologică și potențialul petrolului și gazelor.
Sonde structurale sunt forate pentru a identifica zonele promițătoare și a le pregăti pentru foraj de explorare.
sonde de explorare forează cu scopul de a descoperi noi zăcăminte industriale de petrol și gaze.
sonde de explorare sunt forate în zone cu potențial comercial stabilit de petrol și gaze pentru a studia dimensiunea și structura zăcământului, pentru a obține datele inițiale necesare pentru calcularea rezervelor de petrol și gaze, precum și pentru proiectarea dezvoltării acestuia.
Puțuri de producție așezate în conformitate cu schema de dezvoltare a zăcământului și sunt utilizate pentru obținerea petrolului și gazelor din interiorul pământului
puţuri de injecţie se folosesc atunci când asupra formaţiunii exploatate acţionează diverşi agenţi (injecţie de apă, gaz etc.).
puţuri de observare forează pentru a controla dezvoltarea zăcămintelor (modificări de presiune, poziția contactelor apă-ulei și gazoină etc.).
În plus, în căutarea, explorarea și dezvoltarea zăcămintelor de petrol și gaze, sunt forate puțuri de cartografiere, seismice, speciale și altele.
3. Clasificarea metodelor de foraj
Clasificarea metodelor de foraj pentru petrol și gaze este prezentată în fig. 2.
După metoda impactului asupra rocilor Distingeți găurirea mecanică și cea nemecanică. În forajul mecanic, unealta de foraj afectează direct roca, distrugând-o, iar în forajul nemecanic, distrugerea are loc fără contact direct cu roca de la sursa impactului asupra acesteia. Metode nemecanice(hidraulice, termice, electrofizice) sunt în curs de dezvoltare și nu sunt utilizate în prezent pentru forarea puțurilor de petrol și gaze.
Metode mecanice găurirea se împarte în percuție și rotativă.
Orez. 2. Clasificarea metodelor de foraj de sonde pentru petrol si gaze
În timpul forajului cu impact, distrugerea rocilor se realizează cu ajutorul unui bit 1 suspendat pe o frânghie (Fig. 3). Instrumentul de foraj include, de asemenea, o tijă de șoc 2 și un dispozitiv de blocare a frânghiei 3. Este suspendat pe o frânghie 4, care este aruncată peste un bloc 5 montat pe un catarg (neprezentat în mod convențional). Mișcarea alternativă a sculei de găurit este asigurată de mașina de găurit 6.
Orez. 3. Schema de găurire cu percuție:
1 - dalta; 2 - tija de soc; 3 - blocare frânghie;
4 - sfoară; 5 - bloc; 6 - mașină de găurit.
Pe măsură ce fântâna se adâncește, frânghia se prelungește. Cilindricitatea puțului este asigurată prin rotirea bitului în timpul funcționării.
Pentru a curăța fundul de roca distrusă, instrumentul de foraj este scos periodic din puț și coborât în el. cauc, ca o găleată lungă cu o supapă în fund. Atunci când dispozitivul de evacuare este scufundat într-un amestec de lichid (format sau turnat de sus) și particule de rocă forate, supapa se deschide și dispozitivul de evacuare este umplut cu acest amestec. Când se ridică boilerul, supapa se închide și amestecul este preluat.
După finalizarea curățării fundului găurii, unealta de foraj este coborâtă din nou în puț și forarea continuă.
Pentru a evita prăbușirea pereților puțului, se coboară în ea o țeavă de tub, a cărei lungime crește pe măsură ce gaura de fund se adâncește.
În prezent, la forarea puțurilor de petrol și gaze, forajul cu impact nu este folosit în țara noastră.
Sondele de petrol și gaze sunt construite folosind foraj rotativ. Cu această metodă, rocile nu sunt zdrobite de impact, ci sunt distruse de un bit rotativ, care este supus unei sarcini axiale. Cuplul este transmis la burghie sau de la suprafața de la rotator (rotor) prin garnitura de foraj (foraj rotativ) sau de la motorul de fund (turboburghiu, burghiu electric, motor cu șurub) instalat direct deasupra burghiului.
Aceasta este o turbină hidraulică antrenată de un fluid de foraj injectat în puț. Bormasina electrica este un motor rezistent la lichide alimentat de un cablu de la suprafață. - acesta este un fel de mașină hidraulică de fund, în care se transformă energia fluxului de fluid de spălare în energie mecanică mișcare de rotație folosit mecanism cu șurub.
Prin natura distrugerii rocilor de la fund Distingeți între forarea continuă și cea cu carotă. La continuu foraj, distrugerea rocilor se efectuează pe întreaga zonă a feței. Kolinsky forajul prevede distrugerea rocilor doar de-a lungul inelului în vederea extragerii miez- o proba cilindrica de roci pe toata sau o parte din lungimea sondei. Cu ajutorul eșantionării carotelor, sunt studiate proprietățile, compoziția și structura rocilor, precum și compoziția și proprietățile fluidului care saturează roca.
Toate burghie clasificate in trei tipuri:
- bucăți de acțiune de tăiere și forfecare, distrugând roca cu lame (biți de lamă);
- bucăți de acțiune de zdrobire și forfecare, distrugând roca cu dinții amplasați pe conuri (biți de con);
- biți cu acțiune tăietoare-abrazivă, distrugând roca cu granule de diamant sau știfturi din aliaj dur, care sunt amplasate în partea de capăt a bitului (biti de diamant și aliaj dur).
4. Instalații de foraj, echipamente și unelte
Forarea puțurilor se realizează cu ajutorul instalațiilor de foraj, echipamentelor și uneltelor.
Echipamente de foraj
La fel de motoare de fund la găurire se utilizează un turboburător, un burghiu electric și un motor cu șurub, instalate direct deasupra burghiului.
(Fig. 15) este o turbină cu mai multe trepte (până la 350 de trepte), fiecare treaptă constând dintr-un stator conectat rigid la corpul turboforurului și un rotor montat pe arborele turboforurului. Fluxul de fluid, care curge în jos de la paletele statorului, curge pe paletele rotorului, dând o parte din energia sa pentru a crea cuplu, curge din nou pe paletele statorului etc. Deși fiecare treaptă a unui turboforur dezvoltă un cuplu relativ mic, datorită numărului lor mare, puterea totală pe arborele turboforurului este suficientă pentru a găuri cea mai tare rocă.
Orez. 15. Turbodrill:
a - vedere generală; b - treapta turbodrill; 1 - ax; 2 - corp; 3 - rotor; 4 - stator.
La foraj cu turbina ca fluid de lucru, se folosește un fluid de spălare, care se deplasează de la suprafața pământului de-a lungul garniturii de foraj la turboforfor. Un bit este conectat rigid la arborele turboforghiului. Se rotește independent de garnitura de foraj.
La găurire folosind un burghiu electric motorul electric este alimentat printr-un cablu fixat în interiorul țevilor de foraj. În acest caz, doar arborele motorului se rotește împreună cu burghiul, în timp ce corpul acestuia și garnitura de foraj rămân staționare.
Elemente principale motor cu șurub(Fig. 16) sunt statorul și rotorul. Statorul este realizat prin aplicarea de cauciuc special pe suprafața interioară a carcasei de oțel. Suprafața interioară a statorului are forma unei suprafețe elicoidale cu mai multe porniri. Și rotorul este fabricat din oțel sub forma unui șurub cu pornire multiplă. Numărul de linii elicoidale este cu unul mai mic decât cel al statorului.
Orez. 16. Motor cu șuruburi:
a - vedere generală; b - cavităţi formate între rotor (şurub) şi stator;
1 - sub; 2 - corpul secțiunii motorului; 3 - stator; 4 - rotor;
5 - arbore cardanic; 6 - carcasa axului; 7 - garnitură de capăt;
8 - rulment de contact unghiular cu mai multe rânduri; 9 - cauciuc radial
suport metalic; 10 - arbore ax.
Rotorul este situat în stator cu excentricitate. Datorită acestui fapt și, de asemenea, datorită diferenței dintre numărul de intrări în liniile elicoidale ale statorului și rotorului, suprafețele lor de contact formează o serie de cavități închise - încuietori între camerele de înaltă presiune de la capătul superior al rotorului și presiune redusăîn partea de jos. Ecluzele blochează curgerea liberă a fluidului prin motor și, cel mai important, este în ele în care presiunea fluidului creează un cuplu transmis bitului.
unealtă de găurit
Instrument, folosit la foraj, se împarte în de bază(biți) și auxiliar(tevi de foraj, îmbinări pentru scule, centralizatoare):
Dalte
/Unelte de găurire de bază/
Dalte există lame, con, diamant și carbură.
Biți de lamă(Fig. 17) sunt disponibile în trei tipuri: cu două lame, cu trei lame și cu mai multe lame. Sub acțiunea încărcăturii pe fund, lamele lor se taie în stâncă și, sub influența unui cuplu, o ciobesc. În corpul burghiului există găuri prin care fluidul din garnitura de foraj este direcționat spre fundul sondei cu o viteză de cel puțin 80 m/s. Biții de lamă sunt utilizați la găurirea în roci moi, foarte plastice, cu viteze circumferențiale limitate (de obicei, la găurirea rotativă).
Orez. 17. Dalta cu vâsle:
1 - cap cu filet de legătură; 2 - corp; 3 - lama;
4 - orificiu de spălare; 5 - acoperire din aliaj dur;
6 - muchie de tăiere.
Biți cu role(Fig. 18) sunt disponibile cu una, două, trei, patru și chiar șase freze. Cu toate acestea, cele mai utilizate biți tricon. Când bitul se rotește, frezele, rostogolindu-se de-a lungul fundului, efectuează o mișcare de rotație complexă cu alunecare. În același timp, dinții tăietorilor lovesc piatra, o zdrobesc și o ciobesc. Biții cu role sunt utilizați cu succes la forarea rotativă a rocilor cu o mare varietate de proprietăți fizice și mecanice. Sunt realizate din oțeluri de înaltă calitate cu tratament chimico-termic ulterior al celor mai critice și piese de uzură, iar dinții înșiși sunt din aliaj dur.
Orez. 18. Bit de con:
1 - corp cu cap filetat;
2 - laba cu sprijin; 3 - con.
biți de diamant(Fig. 19) constau dintr-un corp de oțel și un cap purtător de diamante din sarcină de carbură sub formă de pulbere. Partea centrală a bitului este o suprafață concavă în formă de con cu canale pentru lichidul de spălare, iar zona periferică este o suprafață sferică, transformându-se într-una cilindrică pe laterale.
Orez. 19. Dalta cu diamante:
1 - corp; 2 - matrice; 3 - boabe de diamant.
Există trei tipuri de bucăți de diamant: elicoidale, radiale și în trepte. În spirală diamant biți, partea de lucru are spirale echipate cu diamante și găuri de spălare. Biți de acest tip sunt proiectați pentru găurirea cu turbină a rocilor cu abrazive redusă și mediu abrazivă. Diamantul radial biții au o suprafață de lucru sub formă de proeminențe radiale sub formă de sector, echipate cu diamante; între ele sunt amplasate canale de spălare. Biți de acest tip sunt proiectați pentru găurirea rocilor slab abrazive de duritate medie și rocilor dure atât cu metode de foraj rotativ, cât și cu turbină. Diamant în trepte biți au o suprafață de lucru de formă în trepte. Ele sunt utilizate atât pentru metodele de foraj rotativ, cât și pentru cele cu turbină, atunci când se antrenează roci moi și medii cu abrazive redusă.
Utilizarea biților de diamant asigură viteze mari de foraj, reducând curbura puțurilor. Absența rulmenților și rezistența ridicată la uzură a diamantelor măresc durata de viață a acestora până la 200...250 de ore de funcționare continuă. Acest lucru reduce numărul de călătorii. Un bit de diamant poate găuri până la 15...20 de bucăți conice.
Dălți din carbură diferă de cele diamantate prin faptul că în loc de diamante sunt întărite cu aliaje superdure.
Țevi de foraj, încuietori, centralizatoare etc.
/Unelte auxiliare de foraj/
Forajțevile sunt proiectate pentru a transmite rotația burghiului (în timpul forării rotative) și pentru a percepe momentul reactiv al motorului la forarea cu motoare de fund, pentru a crea o sarcină asupra burghiului, pentru a furniza fluid de foraj la fundul puțului pentru a-l curăța de forat. scufundați și răciți bitul, ridicați bitul uzat din puț și coborâți-l nou etc.
Țevile de foraj se caracterizează printr-o grosime crescută a peretelui și, de regulă, au fire conice pe ambele părți. Țevile sunt interconectate cu ajutorul încuietorilor de foraj (Fig. 20). Pentru a asigura rezistența conexiunilor filetate, capetele țevilor sunt îngroșate. Conform metodei de fabricație, țevile pot fi solide (Fig. 21) și cu capete de legătură sudate (Fig. 22). Pentru țevile pline, îngroșarea capetelor poate fi asigurată prin răsturnare spre interior sau spre exterior.
Orez. 20. Blocare foraj:
a - mamelon de blocare; b - ambreiaj de blocare
Orez. 21. Țevi de foraj cu capete de legătură sudate
Orez. 22. Găuriți țevi cu capete răsturnate:
a - aterizare în interior; b - aterizare afară.
Pentru găurirea adâncă se folosesc țevi de foraj din oțel și aliaje ușor cu diametre nominale de 60, 73, 89,102,114,127 și 140 mm. Grosimea peretelui țevilor este de la 7 la 11 mm, iar lungimea lor este de 6, 8 și 11,5 m.
Împreună cu utilizarea obișnuită gulere de foraj(UBT). Scopul lor este de a crea o greutate pe burghiu și de a crește stabilitatea părții inferioare a garniturii de foraj.
Țeavă de plumb conceput pentru a transfera rotația de la rotor la garnitura de foraj (foraj rotativ) și pentru a transfera momentul reactiv de la garnitura de foraj la rotor (la găurirea cu un motor de foraj). Acest tub are de obicei secțiune pătrată și trece printr-o gaură pătrată din rotor. La un capăt, Kelly este conectat la pivot, iar la celălalt capăt, la o țeavă de foraj rotundă convențională.
Lungimea fețelor Kelly determină intervalul posibil de forare a sondei fără extensia sculei. Cu o lungime mică a conductei de conducere, numărul de prelungiri și timpul petrecut pentru forarea puțului crește, iar cu o lungime mare, transportul lor devine mai dificil.
Găuriți încuietori concepute pentru conectarea conductelor. Încuietoarea constă dintr-un niplu de blocare (Fig. 20 a) și un manșon de blocare (Fig. 20 b).
Un sistem continuu cu mai multe legături de unelte și echipamente situat sub pivot (kelly, țevi de foraj cu încuietori, motor de fund și bit) se numește sfoară de foraj. Elementele sale auxiliare sunt sub-uri pentru diverse scopuri, protectori, centralizatori, stabilizatori, calibratori, amortizoare near-bit.
Subs sunt folosite pentru conectarea elementelor din garnitura de foraj cu fire de diferite profile, cu aceleași capete filetate (filet mamelon-niplu, filet de cuplare-cuplaj), pentru conectarea unui motor de foraj etc. În funcție de scopul lor, sub-urile sunt împărțite în sub-uri de tranziție, de cuplare și mamelon.
protectori conceput pentru a proteja țevile de foraj și încuietorile de conectare de uzura suprafeței, iar șirul de carcasă - de ștergere la mutarea țevilor de foraj în ea. În mod obișnuit, se folosesc dispozitive de protecție strânse, care sunt un inel de cauciuc purtat pe șirul de foraj deasupra închizătorului. Diametrul exterior al protectorului depășește diametrul încuietorului.
Centralizatoare folosit pentru a preveni curbura trunchiului la forarea unui puţ. Elementele laterale ale centralizatorului ating pereții puțului, asigurând alinierea garniturii de foraj cu acesta. Centralizatoarele sunt amplasate în șirul țevilor de foraj în locurile cotului așteptat. Prezența centralizatoarelor permite utilizarea unor sarcini axiale mai mari pe burghiu.
Stabilizatoare- acestea sunt elemente de centrare-suport pentru menținerea alinierii rigide a garniturii de foraj în sondă peste unele dintre cele mai critice secțiuni. Ele diferă de centralizatoare prin lungime mai mare.
Calibrator- un fel de unealtă de tăiat stâncă pentru prelucrarea pereților puțului și menținerea diametrului nominal al trunchiului acesteia în cazul uzurii bitului. În garnitura de foraj, calibratorul este plasat direct deasupra burghiului. Acționează simultan ca un centralizator și îmbunătățește condițiile de funcționare ale bitului.
Bit amortizor(amortizor de foraj) este instalat în garnitura de foraj între burghie și gulerele de foraj pentru a amortiza vibrațiile de înaltă frecvență care apar atunci când burghiul funcționează la fundul puțului. Reducerea sarcinilor de vibrație duce la o creștere a duratei de viață a garniturii și burghiului. Există două tipuri de dispozitive de amortizare: amortizoare cu acțiune mecanică, incluzând elemente elastice (arcuri din oțel, inele și bile de cauciuc) și amortizoare de vibrații cu acțiune hidraulică sau hidromecanică.
Exemplu de dispunere a șirului de foraj
În fig. 23.
Orez. 23. Dispunerea șirului de foraj:
1 - portbagaj pivotant; 2 - fir stânga cu opt fire; 3 - sub pivotant; 4 - filet de blocare stânga; 5 - sub tija superioară (PShV); 6 - conducta de conducere; 7 - fir dreapta cu opt fire; 8 - sub tija inferioară (PShN); 9 - filet de blocare dreapta; 10 - safety sub (PBP); 11 - filet de blocare; 12 - ambreiaj de blocare; 13 - fir în opt puncte; 14 - teava de foraj 6 m lungime; 15 - cuplaj; 16 - mamelon de blocare; 17 - inel de siguranta; 18 - țevi de foraj cu greutate (DC); 19 - sub două prize (PBM); 20 - centralizator; 21 - adaptor sub; 22 - guler de foraj aproape de burghie; 23 - dalta
5. Ciclul de construcție a puțurilor
Ciclul de construcție a puțurilor include:
- munca pregatitoare;
- instalarea turnului și a echipamentelor;
- pregătire pentru foraj;
- procesul de foraj;
- fixarea puțului cu țevi de tub și chituirea acestuia;
- deschiderea formării și testarea afluxului de petrol și gaze.
Pe parcursul munca pregatitoare ei aleg un loc pentru o instalație de foraj, amenajează un drum de acces, dă jos alimentarea cu energie, alimentarea cu apă și sistemele de comunicații. Dacă terenul este neuniform, atunci este planificat un site.
Instalare turn si echipamente este produsă în conformitate cu schema de plasare a acestora adoptată pentru aceste condiții specifice. Ei încearcă să plaseze echipamentul în așa fel încât să asigure siguranța în exploatare, ușurința întreținerii, costul redus de construcție și munca de instalareși compactitatea în aranjarea tuturor elementelor instalației de foraj.
În cazul general (Fig. 24), un rotor 3 este situat în centrul instalației de foraj 1, iar lângă acesta este situat un troliu 2. și un amestecător de lut 17. Pe partea opusă a troliului există un rafturi de scule mici 14, rafturi 5 pentru așezarea țevilor de foraj 4, poduri de primire 12, o platformă pentru biți uzați 7 și o platformă de scule de pescuit 10 (este folosită pentru eliminarea accidentelor). în plus, în jurul instalaţiei de foraj sunt amplasate o cabină de utilitate 8, o platformă de scule 6, un sistem de curăţare 15 pentru fluidul de foraj uzat şi containere de rezervă 16 pentru depozitarea fluidului de foraj, substanţe chimice şi apă.
Orez. 24. Schema tipica plasarea echipamentului,
scule, piese de schimb și materiale la instalația de foraj:
1 - instalație de foraj; 2 - troliu; 3 - rotor; 4 - tevi de foraj;
5 - rafturi; 6 - platformă de scule; 7 - locul de cheltuit
biți; 8 - cabina utilitare; 9 - amplasament fermă de argilă; 10 - loc de joaca
unealtă de pescuit; 11 - platforma pentru combustibili si lubrifianti;
12 - pasarele de primire; 13 - banc de lucru lăcătuș; 14 - suport ușor pentru scule;
15 - sistem de curatare; 16 - containere de rezervă; 17 - mixer de lut;
18 - motorizare; 19 - pompe
Există următoarele metode de montare a instalațiilor de foraj: unitate cu unitate, bloc mic și bloc mare.
Cu metoda unitară, instalația de foraj este asamblată din unități separate, pentru livrarea cărora se utilizează transportul rutier, feroviar sau aerian.
Cu metoda blocurilor mici, instalația de foraj este asamblată din 16...20 blocuri mici. Fiecare dintre ele este o bază pe care sunt montate una sau mai multe unități ale instalației.
Prin metoda blocului mare, instalația este asamblată din 2...4 blocuri, fiecare dintre ele combinând mai multe unități și unități ale instalației de foraj.
Metodele bloc oferă rate ridicate de instalare a instalațiilor de foraj și calitatea lucrărilor de instalare. Dimensiunile blocurilor depind de metoda, condițiile și distanța de transport al acestora.
După aceea, un bloc de călătorie cu un bloc de coroană, un pivot și o țeavă de conducere sunt montate succesiv, iar un furtun de presiune este atașat la pivot. În continuare, se verifică centrarea turnului: centrul acestuia trebuie să coincidă cu centrul rotorului.
Pregătirea pentru foraj include un dispozitiv de direcție I (Fig. 1) și o rulare de probă a instalației de foraj.
Orez. 1. Design bine:
1 - conducte de carcasa; 2 - piatră de ciment; 3 - strat;
4 - perforare în carcasa din piatră de ciment;
I - direcție; II - dirijor; III - coloană intermediară;
IV - șir de producție.
Scopul direcției este descris mai sus. Capătul său superior este conectat la un sistem de tratare conceput pentru a îndepărta deșeurile din fluidul de foraj care vine din puț și apoi să-l alimenteze rezervoarele de primire ale pompelor de noroi.
Apoi se forează o gaură pentru țeava principală și se coboară țevile de carcasă în ea.
Instalația de foraj este echipată cu burghie, țevi de foraj, unelte manuale și auxiliare, combustibili și lubrifianți, o sursă de apă, argilă și substanțe chimice. În plus, nu departe de platformă există o cameră pentru odihnă și masă, un uscător pentru salopete și o cameră pentru analiza fluidelor de foraj.
În timpul forării de testare, se verifică performanța tuturor elementelor și componentelor instalației de foraj.
Proces de forajîncepeți prin a înșuruba dalta la tubul pătrat principal. Prin rotirea rotorului, rotația este transmisă bitului prin conducta de conducere.
În timpul forajului, unealta de foraj este coborâtă în mod continuu (avansat), astfel încât o parte din greutatea părții sale inferioare este transferată la burghiu pentru a asigura spargerea eficientă a rocii.
În timpul forajului, puțul este adâncit treptat. După ce Kelly a intrat totul în puț, este necesar să construiți șirul țevii de foraj. Extinderea se realizează după cum urmează. Mai întâi opriți spălatul. Apoi, unealta de foraj este ridicată din puț, astfel încât Kelly să iasă complet din rotor. Folosind o prindere pneumatică cu pană, unealta este atârnată de rotor. Apoi, țeava principală este deșurubată din garnitura de foraj și, împreună cu pivotul, este coborâtă în groapă - un puț ușor înclinat de 15 ... 16 m adâncime, situat în colțul instalației de foraj. După aceea, cârligul este deconectat de la pivot, o altă țeavă pregătită în prealabil este atârnată pe cârlig, este conectată la garnitura de foraj suspendată pe rotor, șirul este scos din rotor, coborât în puț și agățat din nou pe rotorul. Cârligul de ridicare este conectat din nou la pivot și ridicat cu țeava de conducere din orificiu. Kelly este conectat la garnitura de foraj, acesta din urmă este scos din rotor, pompa de noroi este pornită și burghiul este adus cu atenție în jos. După aceea, forarea continuă.
La găurire, burghiul se uzează treptat și devine necesară înlocuirea lui. Pentru a face acest lucru, unealta de foraj, ca și în cazul extensiei, este ridicată la o înălțime egală cu lungimea kellyului, suspendată pe rotor, kellyul este deconectat de la șir și coborât cu un pivot în groapă. Apoi coarda de foraj este ridicată la o înălțime egală cu lungimea suportului de foraj, șnurul este atârnat pe rotor, suportul este deconectat de la coardă, iar capătul său inferior este instalat pe o platformă specială - un sfeșnic, iar partea superioară. capătul este plasat pe un suport special numit deget. În această secvență, toate lumânările sunt ridicate din fântână. După aceea, bitul este înlocuit și începe coborârea instrumentului de găurit. Acest proces se efectuează în ordinea inversă ridicării instrumentului de foraj din puț.
Fixarea puțului cu țevi de tubaj și chituirea acestuia realizat conform schemei prezentate în fig. 1. Scopul astupării inelelor șirurilor de carcasă este de a izola formațiunile productive.
Deși formațiunile productive fuseseră deja expuse în timpul procesului de foraj, ele au fost izolate cu tuburi de tub și obturare, astfel încât pătrunderea petrolului și a gazelor în puț să nu interfereze cu forarea ulterioară. După terminarea forajului pentru a asigura fluxul de ulei și straturile productive de gaze sunt deschise din nou metoda perforarii. După care fântâna este în curs de dezvoltare acestea. provoacă un aflux de petrol și gaze în el. De ce reduceți presiunea fluidului de foraj pe fund într-unul dintre următoarele moduri:
- înroșirea- inlocuirea fluidului de foraj care umple sonda dupa forare cu un lichid mai usor - apa sau ulei;
- pistonare(swabing) - scăderea nivelului de lichid din puț prin coborârea în tub și ridicarea unui piston special (tampoane) pe un cablu de oțel. Pistonul are o supapă care se deschide în timpul coborârii și permite fluidului să umple tubulatura prin el. La ridicare, supapa se închide și întreaga coloană de lichid de deasupra pistonului este adusă la suprafață.
Metodele utilizate anterior de reducere a presiunii fluidului de foraj pe fund, împingere cu gaz comprimat și aerare (saturarea soluției cu gaz) au fost acum abandonate din motive de siguranță.
Astfel, dezvoltarea unui puț, în funcție de condițiile specifice, poate dura de la câteva ore până la câteva luni.
După apariția petrolului și gazelor, puțul este acceptat de către operatori, iar derrick-ul este mutat câțiva metri pentru a foraj următorul puț al tamponului sau târât pe următorul tampon.
6. Spălarea puțurilor
Spălarea puțurilor este una dintre cele mai critice operațiuni efectuate în timpul forajului. Inițial, scopul spălării a fost limitat la curățarea găurii de fund de particulele de butași și îndepărtarea acestora din puț, precum și la răcirea bitului. Cu toate acestea, pe măsură ce industria de foraj s-a dezvoltat, funcțiile fluidului de foraj s-au extins. Acum, aceasta include:
- îndepărtarea particulelor de butași din puț;
- transmisie de putere la un turboburător sau un motor cu șurub;
- prevenirea pătrunderii petrolului, gazelor și apei în puț;
- menținerea particulelor de rocă forată în suspensie atunci când circulația este oprită;
- răcirea și lubrifierea pieselor de frecare a bițurilor;
- reducerea frecării țevilor de foraj față de pereții puțului;
- prevenirea prăbușirii rocilor de pe pereții fântânii;
- scăderea permeabilității pereților puțului din cauza formării crustei.
În consecință, fluidele de foraj trebuie să satisfacă o serie de cerințe:
- îndeplinește funcțiile atribuite;
- să nu aibă un efect dăunător asupra sculei de foraj și a motoarelor de fund (coroziune, uzură abrazivă etc.);
- ușor de pompat și curățat de nămol și gaz;
- să fie în siguranță pentru personalul de service și pentru mediu;
- să fie convenabil pentru pregătire și curățare;
- să fie disponibile, ieftin și reutilizabil.
- Purificarea fluidelor de foraj
Tipuri de fluide de foraj
Tipuri de fluide de foraj
În forajul rotativ al puțurilor de petrol și gaze, următoarele fluide sunt utilizate ca fluide de spălare:
agenți pe bază de apă ( apa industriala, nămoluri naturale de foraj, nămoluri argiloase și non-argiloase);
agenți pe bază de hidrocarburi;
agenţi de emulsionare;
agenţi gazoşi şi aeraţi.
apa tehnica- cel mai accesibil si ieftin lichid de spalare. Având o vâscozitate scăzută, este ușor de pompat, îndepărtează bine tăieturile de pe fundul puțului și răcește bitul mai bine decât alte lichide. Cu toate acestea, reține prost tăieturile (mai ales atunci când circulația este oprită), nu formează o crustă întărită pe peretele puțului, este bine absorbită de formațiunile de joasă presiune, provoacă umflarea rocilor de argilă și înrăutățește permeabilitatea rezervoarelor de petrol și gaze.
noroi natural de foraj numită suspensie apoasă formată într-o sondă ca urmare a dispersării tăierilor de rocă forate pe apă.
Principalul avantaj al utilizării fluidelor naturale de foraj este reducerea semnificativă a nevoii de materiale de import pentru prepararea și prelucrarea acestora, ceea ce duce la soluții mai ieftine. Cu toate acestea, calitatea și proprietățile lor depind de compoziția mineralogică și de natura argilelor care sunt forate, de metoda și modul de foraj și de tipul instrumentului de tăiat roca. Adesea ele conțin un conținut ridicat de particule abrazive. Prin urmare, fluidele naturale de foraj sunt utilizate în cazurile în care condițiile geologice și stratigrafice nu necesită fluid de foraj de înaltă calitate.
Fluide de foraj de argilă cel mai utilizat la forarea puţurilor. Pentru foraj prezintă cel mai mare interes trei grupe de minerale argiloase: bentonită (montmorillonit, beidellit, nontroit, saponit etc.), caolin (caolinit, haloysit, nakrit etc.) și hidromicacee (illit, braviazit etc.). Montmorillonitul și alte minerale bentonite au cele mai bune calități în ceea ce privește pregătirea fluidului de foraj. Deci, din 1 tonă de argilă bentonită se pot obține aproximativ 15 m 3 de soluție de argilă de înaltă calitate, în timp ce din argilă de calitate medie - 4 ... 8 m 3, iar din argile de calitate scăzută - mai puțin de 3 m 3 .
Soluțiile de argilă argilă pereții puțului, formând o crustă densă subțire, care împiedică pătrunderea filtratului în formațiuni. Densitatea și vâscozitatea lor sunt astfel încât noroiurile țin tăieturile de foraj chiar și în repaus, împiedicând-o să se așeze pe fundul găurii în timpul pauzelor de spălare. Soluțiile de argilă ponderate, care creează o contrapresiune mare asupra formațiunilor, împiedică pătrunderea apelor de formare, petrolului și gazelor în puț și curgerea deschisă în timpul forajului. Cu toate acestea, din aceleași motive, este dificil să se separe particulele de rocă în sistemul de circulație a fluidului de foraj.
Se mai folosesc și alte fluide de foraj pe bază de apă: argilos (pentru forarea straturilor superioare ale rocilor deteriorate și fracturate), salin (când se forează în straturi groase de roci purtătoare de sare), inhibat (tratat cu substanțe chimice pentru a preveni umflarea forajului). roci şi îmbogăţirea excesivă a soluţiei cu fază solidă) şi etc.
LA non-argilă includ fluidele de foraj preparate fără utilizarea argilei. Fluid de foraj pentru solide condensate fără argilă preparate pe bază de apă. Faza dispersată în ea se obține chimic, ca urmare a interacțiunii ionilor de magneziu în soluție cu NaOH alcalin sau Ca (OH) 2. Reactie chimica conduce la formarea de particule microscopice de hidroxid de magneziu Mg(OH) 2 în soluție. Soluția capătă o consistență asemănătoare gelului și, după tratamentul chimic, se transformă într-un sistem stabil la sedimentare. O astfel de soluție își păstrează proprietățile structurale și mecanice cu orice mineralizare. Prin urmare, este utilizat în cazurile în care este necesar să se asigure o stabilitate ridicată a pereților puțului, dar este dificil de controlat și reglat salinitatea soluției.
Un alt tip de fluide de foraj non-argilă sunt soluții de biopolimeri. Biopolimerii se obțin prin expunerea anumitor tulpini bacteriene la polizaharide. Proprietățile nămolurilor biopolimerice sunt la fel de ușor de controlat ca cele ale celor mai bune nămoluri de foraj bentonite. Cu toate acestea, unele dintre ele au efect de floculare asupra butașilor, prevenind astfel formarea unei suspensii. În plus, soluțiile de biopolimeri sunt stabile termic. Utilizarea lor este împiedicată de costul lor relativ ridicat.
Fluide de foraj pe bază de petrol sunt un sistem multicomponent în care mediul de dispersie (purtător) este petrol sau produse petroliere lichide (de obicei motorină), iar faza dispersată (în suspensie) este bitum oxidat, asfalt sau argilă tratată special (bentonită hidrofobizată).
Fluidele de foraj pe bază de petrol nu afectează în mod negativ proprietățile rezervoarelor de petrol și gaze, au un efect de lubrifiere: atunci când sunt utilizate, consumul de energie pentru rotația în gol a garniturii de foraj în forajul de sondă este redus și uzura țevilor și burților de foraj este redusă. redus. Cu toate acestea, costul pregătirii unor astfel de fluide de foraj este destul de mare, sunt inflamabile și greu de îndepărtat din instrumente și echipamente.
Fluidele de foraj pe bază de petrol sunt folosite pentru a crește eficiența forajului în roci de rezervor și pentru a menține recuperarea petrolului și gazelor acestora la nivelul inițial, precum și pentru forarea puțurilor în condiții dificile la forarea pachetelor groase de argile gonflabile și săruri solubile.
La fluide de foraj în emulsie mediul de dispersie este o emulsie apă-în-ulei, iar faza dispersată este argilă. Un fluid de foraj preparat pe baza unei emulsie apă-în-ulei se numește emulsie inversă sau emulsie inversă. Faza lichidă a unei astfel de soluții este formată din 60 ... 70% ulei sau produse petroliere, restul este apă. Cu toate acestea, conținutul de apă din emulsia inversată poate fi crescut la 80% sau mai mult dacă în ea se introduc emulgatori speciali.
Fluidele de foraj în emulsie sunt utilizate la forarea în depozite de argilă și straturile de sare. Au proprietăți de lubrifiere bune și ajută la prevenirea lipirii sculelor în puț.
Esență foraj de gaz constă în faptul că aerul comprimat, gazele naturale sau gazele de eșapament ale motoarelor cu ardere internă sunt folosite pentru curățarea fundului, transportul butașilor la suprafață și, de asemenea, pentru răcirea biților. Utilizarea agenților gazoși face posibilă obținerea unui efect economic mare: viteza mecanică crește (de 10...12 ori) și pătrunderea pe bit (de 10 ori sau mai mult). Datorită vitezei mari ale fluxului ascendent în inel, îndepărtarea particulelor de rocă forată este accelerată. Utilizarea agenților gazoși facilitează observațiile hidrogeologice în foraje. În plus, factorul de recuperare a petrolului și gazelor din formațiune crește.
Fluide de foraj aerate sunt amestecuri de bule de aer cu lichide de spălare (apă, emulsii de ulei etc.) într-un raport de până la 30:1. Pentru a crește stabilitatea soluțiilor aerate, în compoziția lor se introduc reactivi - surfactanți și agenți de spumă.
Fluidele de foraj aerate au aceleași proprietăți ca și fluidele din care sunt preparate (pentru fluidele de argilă - formează o turtă de argilă, au vâscozitate și efort de forfecare și păstrează permeabilitatea naturală a zonei de formare a fundului găurii atunci când este deschisă). În același timp, un mare avantaj al fluidelor aerate este posibilitatea utilizării lor în condiții dificile de foraj, cu pierderi catastrofale de fluide de foraj, și deschiderea formațiunilor productive cu presiune scăzută.
Parametrii de bază ai fluidelor de foraj
Principalii parametri ai fluidelor de foraj sunt densitatea, vâscozitatea, indicele de filtrare, efortul de forfecare static, stabilitatea, nămolul zilnic, conținutul de nisip, pH-ul.
Densitate fluidele de spălare pot fi diferite: pentru noroiurile pe bază de ulei este de 890...980 kg/m3, pentru noroiurile cu conținut scăzut de argilă - 1050...1060 kg/m3, pentru noroiurile de foraj ponderate - până la 2200 kg/m3 și mai mult.
Alegerea fluidului de foraj trebuie să asigure că presiunea hidrostatică a coloanei într-un puț de până la 1200 m adâncime depășește presiunea de formare cu 10...15%, iar pentru sondele mai adânci de 1200 m - cu 5...10 %.
Viscozitate caracterizează proprietatea soluției de a rezista mișcării acesteia.
Rata de filtrare- capacitatea soluției în anumite condiții de a da apă rocilor poroase. Cu cât mai multă apă liberă în soluție și cu atât mai puține particule de argilă, cu atât mai multă apă pătrunde în formațiune.
Efort de forfecare statică caracterizează forța care trebuie aplicată pentru a scoate soluția din repaus.
Stabilitate caracterizează capacitatea unei soluții de a menține particulele în suspensie. Este determinată de diferența de densitate dintre jumătățile inferioare și superioare ale volumului unei probe după decantare timp de 24 de ore.Pentru soluțiile obișnuite, valoarea sa nu trebuie să fie mai mare de 0,02 g/cm 3, iar pentru soluțiile ponderate, 0,06 g/ cm 3 .
Namol zilnic- cantitatea de apă eliberată pe zi din soluție în timpul depozitării acesteia nemișcate. Pentru soluții foarte stabile, valoarea nămolului zilnic ar trebui să fie egală cu zero.
Valoare pH pH-ul caracterizează alcalinitatea fluidului de foraj. La pH > 7 solutia este alcalina, la pH = 7 este neutra, la pH< 7 - кислый.
Tratarea chimică a fluidelor de foraj
Tratarea chimică a unui fluid de foraj constă în introducerea anumitor substanțe chimice în acesta pentru a-i îmbunătăți proprietățile fără a modifica semnificativ densitatea.
Ca urmare a tratamentului chimic, se obțin următoarele rezultate pozitive:
- îmbunătățirea stabilității fluidului de foraj;
- reducerea capacității sale de filtrare, reducerea grosimii și a lipicinței tortului pe peretele puțului;
- reglarea vâscozității soluției în direcția creșterii sau scăderii acesteia;
- conferindu-i proprietati deosebite (rezistenta la caldura, rezistenta la sare etc.).
În fluidele de foraj cu argilă se introduc aditivi de lubrifiere și antispumante. Datorită aditivilor de lubrifiere, condițiile de lucru ale garniturii de foraj și ale sculei de tăiere a rocii din puț sunt îmbunătățite. Antispumante previne formarea spumei atunci când faza gazoasă este eliberată din lichidul de spălare.
Pregătirea fluidului de foraj
Pregătirea fluidului de foraj este prepararea unui fluid de foraj cu proprietățile necesare ca urmare a prelucrării materiilor prime și a interacțiunii componentelor.
Organizarea muncii și tehnologia de pregătire a fluidului de foraj depind de formularea acestuia, de starea materiilor prime și a echipamentului tehnic. Considerați-le folosind exemplul preparării unei soluții de argilă.
O astfel de soluție se prepară fie central la fabrica de argilă, fie direct la instalația de foraj. Alimentare centralizată cu fluid de foraj este recomandabil pentru forarea pe termen lung a câmpurilor mari și amplasarea apropiată a instalațiilor de foraj, atunci când pentru forarea puțurilor sunt necesare fluide de foraj cu parametri aceiași sau similari. În acest caz, materiile prime sunt utilizate mai integral și mai economic, este necesară mai puțină energie în comparație cu pregătirea noroiului la instalațiile de foraj, costul noroiului este mai mic, personalul de foraj este scutit de munca grea și consumatoare de timp.
Cel mai economic centralizat prepararea fluidului de foraj prin metoda jet jet direct în groapa de lut, situată în apropierea unui grup mare de instalații de foraj. Dacă nu există astfel de condiții, atunci uzina de argilă este situată în centrul zonei care se forează, iar argila bulgăre este livrată din carieră prin transport rutier, feroviar sau pe apă. La fabricile de argilă în mixere hidraulice cu un volum de 20 ... 60 m 3, se prepară 400 ... 1000 m 3 de soluție de argilă pe zi. Se livrează la instalațiile de foraj prin conducte, în camioane cisterne sau pe nave speciale.
Cu o dispersie mare a instalațiilor de foraj, dificultatea de a le livra soluția finită (teren mlăștinos sau accidentat, condiții de iarnă etc.), necesitatea unor soluții cu parametri diferiți, este recomandabil să se pregătească soluții de argilă. direct pe platformă. Pentru a face acest lucru, instalațiile de foraj sunt în prezent echipate cu o unitate pentru pregătirea noroiului de foraj din materiale pulverulente.
Pulberile de argilă sunt preparate în fabrici speciale din argile de înaltă calitate prin uscare și măcinare ulterioară în mori cu bile. În același timp, conținutul de umiditate al argilelor bulgăre nu este redus sub 6%, iar particulele de argilă nu au voie să se sintereze. Instalațiile de pulbere de argilă sunt construite pe depozite de argile de înaltă calitate sau direct la locurile de consum.
Unitatea de preparare a fluidului de foraj din materiale pulverulente este formată din două buncăre cu un volum total de 42 m 3 din sistemul de alimentare cu pulbere de argilă și un mixer hidraulic (Fig. 25). Când apa este furnizată cu viteză mare prin conducta 10 din camera de amestecare 2, se creează un vid și pulberea de argilă intră în ea din pâlnia 1 a mixerului hidraulic. Amestecul rezultat intră în rezervorul 6, de unde este trimis în rezervoare de rezervă sau de primire pentru finisarea finală a soluției. Capacitatea mixerelor hidraulice ajunge la 80 m 3 de soluție pe oră.
Orez. 25. Mixer hidraulic MG:
1 - buncăr conic (pâlnie); 2 - camera de amestecare; 3 - trapa;
4 - capac recipient; 5 - conducta de scurgere; 6 - capacitate;
7 - cadru sudat (sanie); 8 - tocator (pantof);
9 - montaj; 10 - conductă de alimentare cu fluid
Purificarea fluidelor de foraj
Noroi de foraj gata prin furtunul de presiune atașat la partea fixă a pivotului, acesta este pompat în garnitura de foraj prin pompe de foraj. După ce a trecut prin țevile de foraj, trece cu viteză mare prin găurile din burghiu până la fundul puțului, captează particule de rocă și apoi se ridică între pereții sondei și țevile de foraj. Nu este fezabil din punct de vedere economic să refuzi reutilizarea acestuia și nu poate fi folosit din nou fără curățare, deoarece. în caz contrar, apare uzura abrazivă intensă a echipamentelor și a sculelor de foraj, scade capacitatea de reținere a fluidului de foraj și scade posibilitatea de a efectua noi fragmente mari de rocă.
De asemenea, este necesară trecerea soluțiilor de argilă nou preparate prin sistemul de curățare, deoarece pot conține bulgări de argilă nesuflate, substanțe chimice nereacționate și alte materiale.
Curățare cu lichid de spălare Se efectuează atât datorită precipitării naturale a particulelor de rocă în jgheaburi și rezervoare, cât și forțat în dispozitive mecanice (ecre vibratoare, hidrocicloane etc.). Fluidul de foraj uzat (Fig. 14) de la capul sondei 1 printr-un sistem de jgheaburi 2 intră în sita vibrantă 3, situată la o grilă înclinată și vibratoare. Pentru curățarea ulterioară, fluidul de foraj este pompat prin 4 hidrocicloane cu ajutorul unei pompe de șlam 7, în care este posibilă separarea particulelor de rocă de până la 10 ... 20 de microni. Curățarea finală a soluției din cele mai mici particule de rocă în suspensie se realizează în rezervorul 6 cu ajutorul unor reactivi chimici, sub acțiunea cărora particule foarte mici par să se lipească, după care precipită.
Orez. 14. Sistem de circulație a noroiului:
1 - cap de sondă; 2 - jgheab; 3 - sita vibranta; 4 - hidrociclon;
5 - unitate de preparare fluid de foraj; 6 - capacitate; 7 - pompă de șlam;
8 - rezervor de primire; 9 - pompa de foraj; 10 - conducta de refulare.
La decantarea în rezervoarele 6 și 8, eliberarea gazelor dizolvate din soluție are loc simultan.
Fluidul de foraj curățat este introdus din nou în puț de către pompa 9 prin conducta de injecție 10. După cum este necesar, o cantitate suplimentară de soluție proaspăt preparată din blocul 5 este introdusă în sistem.
7. Complicații în timpul forajului
În procesul de forare a unui puț, sunt posibile diverse tipuri de complicații, în special: prăbușirea rocilor, absorbția fluidului de spălare, pătrunderi de petrol, gaz și apă, accidente, curbura puțurilor.
alunecări de stânci
alunecări de stânci apar din cauza instabilității lor (fracturare, tendință de umflare sub influența apei). Trasaturi caracteristice colapsurile sunt:
- o creștere semnificativă a presiunii la refulare a pompelor de foraj;
- o creștere bruscă a vâscozității fluidului de spălare;
- îndepărtarea prin aceasta a unui număr mare de fragmente de roci prăbușite etc.
Absorbția fluidelor
Absorbția fluidelor- un fenomen în care fluidul injectat în puț este parțial sau complet absorbit de formațiune. Acest lucru se întâmplă de obicei la trecerea unor formațiuni cu porozitate și permeabilitate ridicate, când presiunea de formare este mai mică decât presiunea coloanei de fluid de foraj din puț.
Intensitatea absorbției poate fi de la slabă la catastrofală, când eliberarea lichidului la suprafață se oprește complet.
Următoarele metode sunt utilizate pentru a preveni absorbția:
- clătirea cu lichide ușoare;
- eliminarea absorbției prin blocarea canalelor care absorb lichidul (datorită adăugării de umpluturi inerte la acesta - azbest, mică, coji de orez, turbă măcinată, rumeguș, celofan; turnarea amestecurilor cu priză rapidă etc.);
- creșterea proprietăților structurale și mecanice ale lichidului de spălare (prin adăugare de sticlă lichidă, sare de masă, var etc.).
Spectacole de petrol, gaz și apă
Spectacole pe gaz, petrol și apă apar la forarea sondelor prin formațiuni cu o presiune relativ mare care depășește presiunea fluidului de foraj. Sub acțiunea presiunii apei, are loc revărsarea sau țâșnirea acesteia, iar sub acțiunea presiunii petrolului sau gazelor apar țâșniri continue sau emisii periodice.
Măsurile pentru evitarea pătrunderilor de gaz, ulei și apă includ:
- alegerea corectă a densității lichidului de spălare;
- prevenirea scăderii nivelului acestuia în timpul ridicării garniturii de foraj și în timpul absorbției lichidului.
Clemele instrumentului de foraj
Clemele instrumentului de foraj apar din următoarele motive:
- formarea unei cruste groase și lipicioase pe pereții puțului, de care se lipește instrumentul de foraj atunci când nu se mișcă;
- blocarea sculei de foraj în părțile înguste ale sondei sau în cazul curburii ascuțite a sondei, în cazul prăbușirilor de roci instabile, în cazul tasării rocii forate în caz de încetare a circulației.
Eliminarea lipirii este o operațiune complexă și care necesită timp. Prin urmare, este necesar să luați toate măsurile posibile pentru a le evita.
accidente
accidente, care apar în timpul forajului pot fi împărțite în patru grupe:
- accidente cu biți (deșurubarea burghiei la coborârea sculei din cauza fixării insuficiente a acesteia, spargerea burghiei ca urmare a suprasarcinii etc.);
- accidente cu țevi de foraj și încuietori (ruperea țevii de-a lungul corpului; decoperirea fileturilor țevilor, încuietorilor și sub-urilor etc.);
- accidente cu motoare de fund (deșurubare; ruperea unui arbore sau carcasă etc.);
- accidente cu șirurile de tubaj (strivirea acestora; distrugerea racordurilor filetate; căderea unor tronsoane individuale de țevi în puț etc.).
Pentru a elimina accidentele, special unelte de pescuit(Fig. 26): alunecare, sonerie, robinet, router magnetic, păianjen și altele. Cu toate acestea, cel mai bine este să preveniți accidentele respectând cu strictețe regulile de funcționare a echipamentului, efectuând detectarea, prevenirea și înlocuirea defectelor acestuia în timp util.
Orez. 26. Instrumente de pescuit:
a - aluneca; b - clopot; c - robinet; g - freza magnetica; d - păianjen
Curbura bine
La forarea puțurilor verticale în mod rotativ, spontan curbura bine, acestea. abaterea trunchiului lor de la verticală. Curbura puțurilor verticale implică o serie de probleme: încălcarea rețelei planificate pentru dezvoltarea zăcămintelor de petrol și gaze, uzură crescută a țevilor de foraj, deteriorarea calității lucrărilor de izolare, imposibilitatea utilizării pompelor cu tije în timpul funcționării puțului etc. .
Cauzele curburii puțului sunt factori geologici, tehnici și tehnologici. Geologice - includ prezența unor straturi cu scufundare abruptă în secțiunea puțului; schimbarea frecventă a rocilor de diferite durități; prezența în stâncile prin care trece fântâna, crăpă și caverne. Factorii tehnici care contribuie la curbura sondelor sunt nepotrivirea axei instalației de foraj cu centrul rotorului și axa sondei; poziția înclinată a mesei rotorului; utilizarea țevilor de foraj curbate etc. Factorii tehnologici care provoacă curbura puțurilor includ crearea unor sarcini axiale excesiv de mari pe bit; discrepanța între tipul de bit, cantitatea și calitatea fluidului de foraj și natura rocilor care sunt trecute.
În conformitate cu factorii de mai sus, se iau măsuri pentru a preveni curbura puțurilor. În condiții geologice dificile, se utilizează un aspect special al fundului șirului de foraj, inclusiv calibratori și centralizatori. În plus, aveți nevoie de:
- instalarea echipamentelor se realizează în conformitate cu specificațiile tehnice;
- alegeți tipul de bit în funcție de tipul de roci;
- reduce WOB etc.
8. Puțuri deviate
Puțurile pentru care proiectul prevede o anumită abatere a găurii de jos de la verticală, iar sonda de sondă este efectuată de-a lungul unei traiectorii predeterminate, se numesc îndreptată oblic.
Fântânile înclinate sunt forate atunci când straturile productive se află sub apele mărilor, lacurilor, râurilor, sub teritorii. aşezări, instalații industriale, în zonele umede, precum și pentru a reduce costul construcției instalațiilor de foraj.
Tipurile de profile dezvoltate în prezent pentru puțurile direcționale sunt împărțite în două grupe: profile de tip convențional (reprezentând o linie curbă situată într-un plan vertical) și profile de tip spațial (sub formă de curbe spațiale).
Tipurile de profile ale puțurilor direcționale de tip obișnuit sunt prezentate în fig. 27. Profilul de tip A este format din trei secțiuni: verticală 1, secțiune a pantei sondei 2 și secțiune rectilinie înclinată 3. Se recomandă utilizarea la forarea puțurilor de mică adâncime în câmpuri cu un singur strat, dacă se preconizează o deplasare mare a fundului de foraj. .
Orez. 27. Tipuri de profile de puțuri direcționale:
1 - secțiune înclinată; 2 - secțiunea setului a unghiului de înclinare a trunchiului;
3 - secțiune înclinată rectilinie; 4 - sectiune pentru reducerea unghiului de inclinare al trunchiului
Profilul de tip B se deosebește de cel anterior prin aceea că în locul unei secțiuni înclinate rectilinie, are o secțiune 4 de scădere naturală a unghiului de înclinare. Acest profil este recomandat pentru utilizare la adâncimi mari de puțuri.
Tipul de profil B este format din cinci secțiuni: verticală 1, secțiunea de creștere a unghiului sondei 2, secțiunea înclinată rectilinie 3, secțiunea de scădere a unghiului de înclinare 4 și din nou - verticală 1. Se recomandă utilizarea la forarea puţurilor adânci care intersectează mai multe formaţiuni productive.
Profilul de tip G diferă de cel anterior prin faptul că secțiunile 3 și 4 sunt înlocuite cu secțiuni spontan scăderea unghiului de înclinare 4. Acest profil este recomandat pentru forarea puțurilor adânci în care sunt posibile abateri în partea inferioară a sondei.
Profilul de tip D constă dintr-o secțiune verticală 1 și o secțiune a unghiului setat al trunchiului 2. Se caracterizează printr-o lungime mare a celei de-a doua secțiuni. Profilul este recomandat, dacă este necesar, pentru a menține un unghi dat de intrare în rezervor și a-l deschide la putere maximă.
După cum se poate observa din fig. 27, toate tipurile de profile au o secțiune verticală la început. Adâncimea sa ar trebui să fie de cel puțin 40 ... 50 m. Sfârșitul secțiunii verticale este cronometrat la roci stabile, unde puteți obține un unghi zenit de 5 ... 6 grade într-un singur zbor.
Pentru a devia puțul de la verticală, se folosesc dispozitive speciale de deviere: o țeavă de foraj curbată, un sub curbat, un niplu excentric și deflectoare de diferite tipuri.
În ultimii ani, puțurile verticale și înclinate cu terminații lungi orizontale au devenit mai răspândite. Acest lucru se face pentru a crește suprafața prin care pătrunde petrolul în puț și, în consecință, pentru a crește debitul. În același timp, a devenit posibilă extragerea petrolului la scară industrială, care anterior era considerat nerecuperabil, din cauza putere redusăși permeabilitate scăzută a rezervorului. În plus, capătul orizontal al puțurilor este situat în formațiunea deasupra apei de fund, ceea ce permite prelungirea perioadei de funcționare uscată.
9. Fântâni super adânci
Prima sondă de petrol americană a produs petrol de la o adâncime de aproximativ 20 m. În Rusia, primele puțuri de petrol au avut o adâncime mai mică de 100 m. Foarte repede, adâncimea lor a ajuns la câteva sute de metri. Până la sfârșitul anilor 60 în URSS, adâncimea medie a puțurilor pentru producția de petrol și gaze era de 1710 m. Cel mai adânc zăcământ de petrol din țara noastră a fost descoperit în regiunea Groznîi, la o adâncime de 5300 m, și s-a obținut gaz industrial. în depresiunea Caspică de la o adâncime de 5370 m.
Cel mai adânc rezervor de gaze din Europa din câmpul Magossa (nordul Italiei) se află la o adâncime de 6100 m. Cea mai mare adâncime din lume de la care se realizează producția comercială de gaze este de 7460 m (Texas, SUA).
Tendința generală a producției de petrol și gaze din orizonturi din ce în ce mai profunde poate fi ilustrată prin următoarele cifre. Chiar și în urmă cu 20 de ani, principala producție de petrol (66%) se desfășura din cele mai tinere roci cenozoice. Din rocile mezozoice mai vechi s-a extras 19% din petrol, iar din cele mai vechi roci paleozoice - 15%. Acum situația s-a schimbat: rocile mezozoice au devenit principalii furnizori de petrol, urmate de rocile paleozoice.
Astfel, una dintre sarcinile forării puțurilor de mare adâncime este căutarea orizonturilor purtătoare de petrol și gaze la adâncimi mari. Doar forajele ultraprofunde pot pune capăt disputei dintre susținătorii ipotezelor organice și anorganice ale originii petrolului. În cele din urmă, forarea ultra-profundă este necesară pentru un studiu mai detaliat al interiorului pământului. Într-adevăr, astăzi știm de multe ori mai multe despre spațiul îndepărtat decât despre ceea ce se află sub noi, la câteva zeci de kilometri distanță.
Forarea puțurilor ultra adânci este asociată cu mari dificultăți. Presiunea și temperatura cresc odată cu adâncimea. Deci, la o adâncime de 7000 m, chiar presiune hidrostatica egal cu 70 MPa, 8000 m -80 MPa etc. Și în rezervor poate fi de două ori mai mult. Cum să păstrezi acest „geniu” în „sticlă”? Sunt necesare pompe de înaltă presiune pentru a furniza fluidul de spălare. Cum ar trebui să fie acest lichid dacă temperatura la fundul găurii ajunge la 250 °C? Cum să rotiți un șir de mai mulți kilometri de țevi de foraj? Cum să folosiți țevi de foraj, dacă țevi din oțel suportă greutatea lor până la o adâncime de 10 km?
Unele dintre întrebări au primit deja răspuns. Pentru forarea puțurilor ultra adânci, se folosește un fluid de foraj ponderat, astfel încât să „astupe” puțul cu propria greutate. Sondele ultra adânci sunt forate folosind motoare de fund, iar țevile de foraj sunt realizate din aliaj de aluminiu ușor și durabil.
Era forajelor adânci a început în 1961 odată cu implementarea proiectului american Mohol. Fântâna a fost așezată pe fundul Oceanului Pacific, lângă insula Guadelupe, sub un strat de apă de patru kilometri. S-a presupus că fântâna, după ce a trecut de 150 m de roci de fund liber și 5,5 km de roci subiacente solide, se va plonja în manta - următorul strat al planetei noastre după crustă. Cu toate acestea, forajul s-a oprit după primii 36 de metri. Motivul a fost că după extragerea primului miez, gura binelui deja început nu a putut fi găsită, în ciuda utilizării celor mai moderne instrumente de căutare.
În 1968, a fost făcut un al doilea atac asupra mantalei de la o navă de foraj special echipată (Fig. 28). Cu toate acestea, în 1975, când straturile bazaltice superioare ale fundului oceanului au fost expuse, forajul a fost oprit din cauza dificultăților tehnice.
Orez. 28. Vedere generală a navei de foraj:
1 - navă; 2 - macara de marfă; 3 - elicopter
zonă; 4 - instalație de foraj
Ulterior, pe uscat au fost forate sonde ultra-adânci. În 1970, puțul 1-SL-5407 a fost forat în Louisiana cu o adâncime de 7803 m.
O reprezentare vizuală a unei puțuri ultra-adânci moderne și a echipamentelor sale poate fi obținută prin exemplul uneia dintre cele mai adânci puțuri din lume. 1-Beiden, forat în statul Okhlacoma. Adâncimea sondei este de 9159 m. Forajul a început în 1970 și a durat 1,5 ani. Înălțimea instalației de foraj este de 43,3 m, capacitatea de ridicare este de 908 tone, puterea instalației de tragere este de 2000 kW, iar fiecare dintre cele două pompe de noroi este de 1000 kW. Capacitatea totală a sistemului de circulație la sol pentru noroi 840 m\ Capul sondei este echipat cu supape anti-explozie proiectate pentru o presiune de 105,5 MPa.
Din punct de vedere structural, puțul constă dintr-o direcție de puț cu un diametru de 0,9 m până la o adâncime de 18 m, un conductor cu un diametru de 0,5 m până la o adâncime de 1466 m, țevi de tubulare până la o adâncime de 7130 m și șiruri de producție. În total, aproximativ 2200 de tone de țevi de carcasă de oțel, 1705 de tone de ciment și 150 de biți de diamant au fost folosite pentru sondă. Costul total al forării sondei a fost de 6 milioane de dolari.
La începutul anului 1975, în URSS existau zece puțuri, a căror adâncime depășea 6 km. Acestea includ Aral-Sorskaya în câmpia Caspică cu o adâncime de 6,8 km, Biikzhalskaya în Azerbaidjan cu o adâncime de 6,7 km, Sinevidnaya (7,0 km) și Shevchenkovskaya (7,52 km) în vestul Ucrainei, Burunnaya (7,5 km) în Caucazul de Nord , etc. Cea mai adâncă fântână din lume, fântâna Kola, a trecut linia de 12 km.
10. Foraj de sondă în larg
În prezent, ponderea petrolului extras din câmpurile offshore este de aproximativ 30 % din toată producția mondială și chiar mai mult gaz. Cum ajung oamenii la această bogăție?
Cea mai simplă soluție este să aruncați grămezi în apă puțin adâncă, să instalați o platformă pe ele, iar pe ea sunt deja amplasate o instalație de foraj și echipamentele necesare.
O altă modalitate este de a „extinde” coasta umplând apa de mică adâncime cu pământ. Așadar, în 1926, golful Bibi-Heybat din regiunea Baku a fost umplut și în locul său a fost creat un câmp petrolier.
După descoperirea unor zăcăminte mari de petrol și gaze în Marea Nordului în urmă cu mai bine de jumătate de secol, a luat naștere un proiect îndrăzneț de drenare a acesteia. Faptul este că adâncimea medie a majorității Mării Nordului abia depășește 70 m, iar unele secțiuni ale fundului sunt acoperite cu doar un strat de apă de patruzeci de metri. Prin urmare, autorii proiectului au considerat oportun, cu ajutorul a două baraje - peste Canalul Mânecii, în regiunea Dover, precum și între Danemarca și Scoția (cu o lungime de peste 700 km) - să se taie o secțiune uriașă a Nordului. Măriți și pompați apa de acolo. Din fericire, acest proiect a rămas doar pe hârtie.
În 1949, prima sondă de petrol din URSS a fost forată în larg, în Marea Caspică, la 40 km de coastă. Astfel a început crearea unui oraș pe grămezi de oțel, numit „Oil Rocks”. Cu toate acestea, construirea unor pasaje supraterane care se întind pe mulți kilometri de coastă este foarte costisitoare. În plus, construcția lor este posibilă numai în ape puțin adânci.
Când forați puțuri de petrol și gaze în mări și oceane adânci, este dificil din punct de vedere tehnic și neprofitabil din punct de vedere economic să folosiți platforme staționare. Pentru acest caz, au fost create instalații de foraj plutitoare care sunt capabile să schimbe zonele de foraj în mod independent sau cu ajutorul remorcherelor.
Există platforme de foraj cu cric, platforme de foraj semi-submersibile și platforme de foraj de tip gravitațional.
Platformă de foraj cu cric(Fig. 29) este un ponton plutitor 1 cu un decupaj, deasupra căruia se află o instalație de foraj. Pontonul are o formă de trei, patru sau poligonală. Adăpostește echipamente de foraj și auxiliare, o cabină cu mai multe etaje cu cabine pentru echipaj și muncitori, o centrală electrică și depozite. Coloanele de sprijin multimetru 2 sunt instalate la colțurile platformei.
Orez. 29. Platformă de foraj cu cric în poziție de transport:
1 - ponton plutitor; 2 - suport de ridicare; 3 - instalație de foraj;
4 - macara rotativă (de marfă); 5 - compartiment de locuit; 6 - heliport;
7 - portal ridicat; 8 - puntea principală
În punctul de foraj, cu ajutorul cricurilor hidraulice, coloanele sunt coborâte, ajung la fund, se sprijină pe pământ și se adâncesc în el, iar platforma se ridică deasupra suprafeței apei. După ce forarea este finalizată într-un loc, platforma este transferată în altul.
Fiabilitatea instalării platformelor de foraj cu cric depinde de rezistența solului care formează fundul la locul de foraj.
Platforme de foraj semisubmersibile(Fig. 30) sunt utilizate la adâncimi de 300 ... 600 m, unde platformele de ridicare nu sunt aplicabile. Ele nu se odihnesc pe fundul mării, ci plutesc deasupra locului de foraj pe pontoane uriașe. Astfel de platforme sunt împiedicate să se deplaseze prin ancore care cântăresc 15 tone sau mai mult. Corzile de oțel le conectează la trolii automate care limitează deplasările orizontale în raport cu punctul de foraj.
Orez. 30 Platformă de foraj semi-submersibilă:
1 - ponton submersibil; 2 - coloana de stabilizare; 3 - partea superioară a corpului;
4 - instalație de foraj; 5 - macara de marfă; 6 - heliport.
Primele platforme semi-submersibile nu au fost autopropulsate și au fost livrate în zona de lucru cu ajutorul remorcherelor. Ulterior, platformele au fost echipate cu elice acţionate de motoare electrice cu o capacitate totală de 4,5 mii kW.
Dezavantajul platformelor semi-submersibile este posibilitatea deplasării lor în raport cu punctul de foraj sub influența valurilor.
sunt mai stabile platforme de foraj de tip gravitaţional. Sunt echipate cu puternice bază de ciment odihnindu-se pe fundul mării. Această bază găzduiește nu numai coloane de ghidare pentru foraj, ci și celule-rezervoare pentru stocarea petrolului produs și a motorinei utilizate ca purtător de energie, precum și numeroase conducte. Elementele de bază sunt livrate la locul de instalare sub formă de blocuri mari.
Fundul mării de la locul platformelor gravitaționale trebuie pregătit cu grijă. Chiar și o pantă ușoară a fundului amenință să transforme instalația de foraj în Turnul înclinat din Pisa, iar prezența proeminențelor pe fund poate provoca o despicare a bazei. Prin urmare, înainte de a seta forajul „la punct”, toate pietrele proeminente sunt îndepărtate, iar fisurile și depresiunile din partea de jos sunt sigilate cu beton.
Toate tipurile de platforme de foraj trebuie să reziste la presiunea valurilor de până la 30 m înălțime, deși astfel de valuri apar o dată la 100 de ani.
Trimiteți-vă munca bună în baza de cunoștințe este simplu. Utilizați formularul de mai jos
Studenții, studenții absolvenți, tinerii oameni de știință care folosesc baza de cunoștințe în studiile și munca lor vă vor fi foarte recunoscători.
postat pe http://www.allbest.ru/
EDUCATIE PROFESIONALA
Yu.V. VADETKY
FORAGE DE POTEI SI GAZ
Manual
admis
Ministerul Educației al Federației Ruse
ca manual pentru instituţiile de învăţământ
educație profesională inițială
Moscova
ACADEMA
2009
UDC 622.23/.24 BBK33.131 V12
Autorul își exprimă profunda recunoștință
Artă. Cercetător al SA „VNIIOENG” V.A. Ershova
pentru ajutor în pregătirea manuscrisului pentru publicare
Revizor --
Cercetător șef al Institutului de Probleme Petrolului și Gazelor din cadrul Academiei Ruse de Științe V. I. Igrevskiy
Vadetsky Yu. V.
B12 Forarea sondelor de petrol și gaze: un manual pentru început. prof. educație / Yuri Vyacheslavovich Vadetsky. - M.: Centrul editorial „Academia”, 2003. - 352p. ISBN 5-7695-1119-2
Manualul oferă informații scurte despre geologia generală și a câmpurilor petroliere. Sunt descrise principiile de dezvoltare a zăcămintelor de petrol și gaze, precum și metodele de exploatare a sondelor de petrol și gaze. Sunt date date despre instalațiile de foraj și metodele de construcție a acestora.
Pentru elevii școlilor primare profesionale.
UDC 622.23/.24 BBK33.131
© Vadetsky Yu.V., 2003
© Centrul educațional și editorial „Academy”, 2003 ISBN 5-7695-1119-2
© Design. Centrul editorial „Academia”, 2003
Introducere
Capitolul 1 Rezumat al geologiei generale și petroliere
1.1. Concepte de bază despre structura și compoziția scoarței terestre
1.2. Pliere și tipuri de pliuri
1.3. Principalele proprietăți fizice și mecanice ale rocilor care afectează procesul de distrugere a acestora în timpul construcției puțurilor
1.4. Formarea bazinului de ulei și ulei
1.5. Căutarea, explorarea și dezvoltarea zăcămintelor
Capitolul 2 Informații generale despre sondele de foraj și echipamentele utilizate pentru acest proces
2.1. Conceptul de foraj, clasificarea și scopul puțurilor
2.2. Schema tehnologică de forare puțuri în mod rotativ
2.3. Ciclul de construcție a puțurilor. Echilibrul timpului calendaristic și conceptul de viteză de foraj
2.4. Instalații de foraj adânc
2.5. Instalații de foraj și echipamente pentru coborârea și recuperarea garniturii de foraj
2.6. Echipamente și instrumente de foraj puțuri
2.7. Măsuri generale de protecție a naturii și a mediului în timpul construcției puțurilor
2.8. Scheme de amplasare a instalațiilor și echipamentelor terestre
2.9. Lucrări pregătitoare pentru forarea unui puț
Capitolul 3 Instrument pentru spargerea stâncii
3.1. Scopul și clasificarea sculelor de tăiat roci
3.2. Biți cu palete pentru găurirea continuă a găurii inferioare
3.3. Biți conici pentru găurire continuă în fundul găurii
3.4. Biți de diamant și bucăți întărite cu inserții de diamant policristalin sintetic
3.5. Coji pentru foraj cu carote (receptoare pentru carote) și capete de foraj pentru acestea
3.6. Dalte pentru scopuri speciale
Capitolul 4 Snur de foraj
4.1. Dispoziții generale
4.2. Proiectarea elementelor garniturii de foraj
4.3. Condițiile de funcționare ale șirurilor de foraj
4.4. Finalizarea și funcționarea șirului de foraj
Capitolul 5 Tehnologia de spălare a puțurilor și fluide de foraj
5.1. Dispoziții generale
5.2. Fluide de foraj pe bază de apă
5.3. Utilizarea apei ca fluid de spălare
5.4. Fluide de foraj pe bază de petrol (rno)
5.5. Forarea puțurilor cu curățarea găurii de fund cu aer sau gaz. Lichide de spălare aerate și spumă
5.6. Echipamente pentru prepararea si purificarea fluidelor de foraj
5.7. Selectarea tipului de fluid de foraj
5.8. Forme de organizare a agriculturii argilei
Capitolul 6 Complicații în procesul de forare a puțurilor
6.1. Dispoziții generale
6.2. Complicații care provoacă încălcarea integrității pereților puțului
6.3. Prevenirea și controlul pierderilor
6.4. Prevenirea și controlul manifestărilor de gaze, petrol și apă
6.5. Caracteristicile puțurilor de foraj în condiții de agresiune cu hidrogen sulfurat
6.6. Complicații la forarea puțurilor în permafrost
Capitolul 7 Modul foraj
7.1. Dispoziții generale
7.2. Influența parametrilor modului de foraj asupra indicatorilor cantitativi și calitativi ai forajului
7.3. Alegerea metodei de foraj
7.4. Caracteristici ale modului de foraj rotativ
7.5. Caracteristicile modului de foraj cu turbină
7.6. Particularitățile modului de găurire cu motoare cu șurub (deplasare) în fundul puțului
7.7. Caracteristici ale modului de găurire cu burghie electrice
7.8. Caracteristici ale modului de găurire cu biți de diamant
7.9. Control asupra parametrilor modului de foraj
7.10. Alimentare cu scule
Capitolul 8 Abaterea puțurilor și forarea puțurilor deviate
8.1. Lupta împotriva curburii puțurilor verticale
8.2. Forarea puţurilor direcţionale
8.3. Foraj cu grup de puțuri
8.4. Forarea puțurilor multilaterale (multilaterale), ramificate orizontal și orizontal
Capitolul 9 Deschiderea și testarea orizonturilor productive (straturi) în procesul de forare puțuri
9.1. Deschiderea orizonturilor productive (straturi)
9.2. Eșantionarea și testarea orizonturilor productive (straturi) în timpul forajului
Capitolul 10
10.1. Dispoziții generale
10.2. Bine design
10.3. Carcasa
10.4. Dispozitive și accesorii pentru echiparea șirurilor de carcasă
10.5. Trecerea șirului de tubaj în puț
10.6. Cimentarea bine
10.7. Materiale și echipamente de cimentare pentru cimentarea puțurilor
10.8. Lucrări pregătitoare și proces de cimentare
10.9. Lucrare finala si verificarea rezultatelor cimentarii
Capitolul 11 Dezvoltarea și testarea puțurilor
11.1. Deschiderea orizonturilor productive (straturi) după rularea și cimentarea firului de producție
11.2. Dezvoltarea și testarea orizonturilor productive (straturi) după rularea și cimentarea firului de producție
Capitolul 12 Accidente de foraj
12.1. Tipuri de accidente, cauzele acestora și măsuri de prevenire
12.2. Eliminare blocată
12.4. Organizarea muncii în caz de accident
Capitolul 13 Particularitățile forajului în larg
13.1. Dispoziții generale
13.2. Echipament submarin pentru capul puțului
13.3. Câteva caracteristici ale forării puțurilor de petrol și gaze offshore
13.4. Serviciu offshore
Bibliografie
INTRODUCERE
Forarea sondelor de petrol sau gaze este un proces complex și, în unele cazuri, periculos. Forarea sondelor de petrol sau gaze poate fi realizată cu succes numai cu respectarea obligatorie a unui număr de reguli și reglementări. Există o mulțime de astfel de reguli și reglementări și toate sunt prezentate în acest manual, dar printre această varietate se numără principalele (sunt doar șapte) care ar trebui reținute și trebuie respectate. Implementarea lor garantează succesul.
Principalele prevederi care garantează forarea cu succes a puțului.
1. Toți membrii echipei de foraj, în special forătorii, trebuie să cunoască bine ordinea de lucru geologică și tehnică (GTO), caracteristicile forajului în zonă, secțiunea geologică (intervalele) sondei. O atenție deosebită trebuie acordată intervalelor în care sunt posibile complicații. La apropierea unor astfel de intervale se iau măsurile de precauție necesare.
2. Echipa echipajului de foraj, în special veriga sa principală - ceasul, trebuie să fie prietenoasă și lipită. Dacă un ceas include o persoană care, din anumite motive, nu este compatibilă cu restul echipei, este mai bine să-l transferați la alt ceas, brigadă.
Procesul de foraj nu este intotdeauna calm si inofensiv, sunt posibile situatii extreme (accidente, emisii de gaze, incendii etc.), in care se cere indemanare, calm, curaj si dedicare din partea echipajului de foraj (ceas). În aceste condiții, relația dintre membrii echipei poate juca un rol decisiv.
3. Toți membrii echipajului de foraj, în special forătorii, trebuie să fie profesioniști în domeniul lor. Profesionalismul în foraj se realizează prin formare continuă și dezvoltare profesională.
4. Procesul de foraj este în mare măsură conservator. Constă într-o succesiune de operații, adesea repetate, care sunt efectuate în mod necesar într-o anumită ordine. Abaterea de la această regulă duce în cele mai multe cazuri la complicații sau accidente. În acest sens, un ceas de foraj poate fi comparat cu un echipaj de aeronavă, când cea mai mică abatere de la reguli duce la dezastru.
5. Toți membrii echipei sunt obligați să respecte disciplina în procesul de construcție a puțului. Cea mai mică slăbiciune, apariția la locul de muncă în stare de ebrietate sau după o zi furtunoasă petrecută cu o zi înainte este plină de consecințe grave. Pierderea sau lipsa de vigilență duce adesea la accidente, inclusiv mortale. Fiecare abatere de la normele general acceptate nu trebuie să treacă neobservată.
6. Fiecare membru al echipajului de foraj trebuie să respecte cu strictețe regulile de siguranță, să poată acorda primul ajutor victimei, să-și cunoască atribuțiile în caz de degajare de gaze, incendiu și alte situații extreme. Sarcina maistrului de foraj este de a efectua în mod constant exerciții și de a aduce acțiunile membrilor echipajului de foraj în aceste situații la automatitate deplină.
7. Fiecare membru al echipajului de foraj trebuie să facă numai ceea ce îi este prescris prin fișa postului. Toate celelalte acțiuni sunt efectuate numai la ordinul maistrului de foraj (foraj).
Informatie scurta din istoria dezvoltării echipamentelor și tehnologiei operațiunilor de foraj. Este greu de stabilit în ce mileniu î.Hr. a început omul să folosească uleiul, dar este evident că acest lucru s-a întâmplat în vremuri foarte străvechi. La început, uleiul a fost folosit ca remediu împotriva unei mari varietăți de boli: lepră, inflamație a ochilor etc. În antichitate, uleiul era de mare importanță și ca material de iluminat.
Sub sistemul slave, aria de aplicare a uleiului și a bitumului natural sa extins semnificativ. Au fost deja folosite nu numai ca remediu și material de iluminat, ci și în scopuri de construcție. La construirea pereților, bitumul a fost utilizat pe scară largă amestecat cu cărămizi și pietricele coapte. Extinderea domeniului de aplicare al petrolului în epoca sistemului de sclavi a determinat o îmbunătățire a tehnologiei de extracție a acestuia. Metoda folosită anterior de colectare a petrolului în locurile unde a ajuns la suprafața pământului nu mai putea satisface nevoile pentru acesta. A apărut o metodă de extracție a petrolului în groapă (sau săpat). Kopanki erau gropi de mică adâncime (până la 2 m adâncime), în care era introdus vaci pentru a proteja pereții de prăbușire. În partea de jos a copancăi, uleiul s-a acumulat, curgându-se prin sol. Uleiul de la excavatoare a fost scos periodic, pe măsură ce s-a acumulat.
Marile descoperiri geografice și înflorirea relațiilor comerciale sub sistemul feudal au contribuit semnificativ la creșterea unui număr de industrii, inclusiv a petrolului. Cererea crescută de petrol a condus la dezvoltarea de noi tehnici de extracție a acestuia. Vechea metodă (săpat) de groapă nu mai putea satisface nevoile noii societăți pentru petrol. A apărut o metodă de extracție a petrolului de puț, care era mai perfectă și mai profitabilă decât cea de groapă (săpat), deoarece permitea exploatarea straturilor productive mai adânci și creșterea producției de petrol.
Abolirea iobăgiei a înlăturat obstacolele în calea dezvoltării industriale a Rusiei iobage feudale. În această perioadă, rolul industriei petroliere în dezvoltarea industrială generală a țării a crescut semnificativ. Uzinele, fabricile, transportul feroviar și pe apă aveau nevoie de combustibil, în primul rând cărbune și petrol. Metoda puţului nu mai putea satisface nevoile societăţii cu o nouă structură economică şi politică. Era nevoie de o metodă mai bună pentru a distruge rocile și, odată cu ea, o nouă modalitate de a ridica petrolul la suprafața pământului. Forarea puțurilor a fost o astfel de metodă.
Se crede că Edwin Drake a forat primul puț de petrol comercial în 1859 în Pennsylvania (SUA). Aproximativ în același timp, a început forarea puțurilor în Rusia. Primele sonde de petrol au fost forate folosind o metodă manuală ineficientă cu tije rotative. Curând au trecut la forarea puțurilor de petrol folosind o metodă manuală de percuție cu tije, care a fost folosită de mult timp la forarea puțurilor pentru saramură și apă.
Metoda de găurire pe tije de fier cu ajutorul unei unealte cu cădere liberă (tijă de percuție) este utilizată pe scară largă în câmpurile petroliere din Azerbaidjan. Metoda de foraj cu frânghie de percuție a devenit larg răspândită în regiunea petrolieră Grozny.
Trecerea de la metoda manuală de forare a puțurilor la cea mecanică a condus la necesitatea abordării unui număr de probleme de mecanizare a operațiunilor de foraj. O contribuție majoră la această lucrare au avut-o inginerii minieri ruși G. D. Romanovsky (1825-1906) și S. G. Voislav (1850-1904). Pe măsură ce adâncimea puțurilor de petrol a crescut, care a ajuns la aproximativ 300 m până în 1900, deficiențele metodei de foraj cu percuție au devenit din ce în ce mai vizibile.
Forarea rezervoarelor de petrol de adâncime a necesitat îmbunătățirea tehnicilor de forare a puțurilor. Când burghie cu percuție în 1 min. făcute de la 26 la 40 de căderi și la fiecare 2 ore a fost necesară ridicarea instrumentului de foraj pentru a curăța fundul de rocă forată. Pereții fântânii au fost distruși, așa că au trebuit fixați cu 12 ... 14 coloane. Cheltuit pe el o cantitate mare metal - mai mult de 0,5 tone pe metru de penetrare. Rata de penetrare în timpul forajului cu percuție a fost neglijabilă. În vremurile pre-revoluționare, în forajul cu tije, nu era mai mult de 34,6 m / st.-lună (metru pe mașină-lună) cu o adâncime medie a puțului de 300 ... 400 m, iar în Grozny a ajuns la 90 m / st.-lună cu o adâncime medie a sondei de 600 m. Metoda percuției a fost înlocuită cu foraj rotativ, în urma căreia aceste neajunsuri au fost eliminate. În timpul forajului rotativ, atât forarea puțurilor, cât și îndepărtarea rocii forate la suprafață cu ajutorul fluidului de foraj se efectuează simultan (îndepărtarea rocii forate cu un flux de apă circulant a fost inventată în 1848 de inginerul francez Fovelle). Din 1901, când găurirea rotativă a fost folosită pentru prima dată în SUA cu spălarea găurii de fund printr-un flux de fluid circulant, a început o perioadă de dezvoltare și îmbunătățire a metodei de foraj rotativ. În Rusia, primul puț cu o adâncime de 345 m a fost forat folosind o metodă rotativă în 1902 în regiunea Grozny.
Una dintre cele mai dificile probleme care au apărut la forarea puțurilor, în special prin metoda rotativă, a fost problema etanșării spațiului inelar dintre țevile de tub și pereții puțului. Această problemă a fost rezolvată de inginerul rus A. A. Bogushevsky, care în 1906 a patentat o metodă de pompare a nămolului de ciment în șirul de carcasă, cu deplasarea ulterioară a acestuia prin partea de jos (pantof) a șirului de carcasă în inel. Metoda lui Bogushevsky a fost răspândită rapid nu numai în Rusia, ci și în străinătate. Totuși, acest lucru nu l-a împiedicat pe inginerul american Perkins în 1918 să obțină un brevet pentru o metodă de cimentare a puțurilor care repetă invenția inginerului A.A. Boguşevski.
Odată cu soluționarea cu succes a problemelor practice ale tehnologiei de foraj, oamenii de știință și inginerii țării noastre au acordat multă atenție dezvoltării teoriei. Un rol major în dezvoltarea tehnologiei petroliere l-a jucat Jurnalul de minerit, publicat din 1825. Jurnalul a publicat lucrările celor mai mari specialiști în domeniul petrolului din acea vreme: G.D. Romanovsky, S. Gulishambarov, A. Vasiliev, N.A. Sokolovsky, I. A. Timpul și altele Din 1899, revista „Oil Business” a început să fie publicată la Baku.
În 1904-1911. a fost publicată o lucrare clasică în patru volume a unuia dintre cei mai mari ingineri minieri ruși I. N. Glushkov „Ghid pentru forarea puțurilor”, care pentru o lungă perioadă de timp carte de masă toți petroliștii.
În timpul Primului Război Mondial și ulterior război civil Industria petrolieră rusă era în declin. Refacerea industriei petroliere a început imediat după eliberarea regiunilor petroliere de sub intervenţionişti şi albi.
Din 1924, reconstrucția tehnică a forajului puțului a început în industria petrolului din URSS. Cele mai importante moduri ale acestei reconstrucții au fost următoarele:
înlocuirea găuririi cu percuție cu rotație;
utilizați în loc de energie electrică cu abur - cea mai ieftină.
În anii planurilor cincinale de dinainte de război, industria petrolului și gazelor s-a dezvoltat într-un ritm accelerat. Din 1928 până în 1940, producția de petrol a crescut de la 11.625 mii tone la 31.121 mii tone, iar forarea puțurilor pentru petrol și gaze de la 362 mii metri la 1947 mii metri.
În anii Marelui Războiul Patriotic forătorii de petrol au arătat exemple de eroism în munca lor, organizând explorarea și producția de petrol și gaze în regiunile de est ale țării în condiții dificile de război. Această perioadă se caracterizează printr-o creștere a ponderii contorizării în forajele de explorare de la 23% din totalul contorizării în 1940 la 42% în 1945, iar ponderea regiunilor estice în totalul contorului în URSS a crescut de la 21,8% în 1940 la 52,5% în 1944 și 45% în 1945
Dezvoltarea forării puțurilor de petrol și gaze în URSS a fost determinată în mare măsură de motorul hidraulic de fund, turboforama, inventat în 1923 de M. A. Kapelyushnikov, S. M. Volokh și N. A. Korneev.
În 1923, primul puț din lume a fost forat în Azerbaidjan folosind un turboforator cu o singură treaptă, numit turboforinator Kapelyushnikov. Turboforatoarele Kapelyushnikov nu au găsit o aplicație largă, deoarece cu o turbină cu o singură treaptă, lichidul curgea prin paletele sale cu o viteză de 50 ... 70 m / s. O astfel de viteză mare de mișcare a fluidului care transportă particulele abrazive ale formațiunilor forate a condus la acționarea extrem de rapidă a palelor turbinei. În plus, turboforinatorul Kapelyushnikov avea o putere foarte scăzută și o eficiență scăzută (29 ... 30%). Puterea turboforatoarelor lui Kapelyushnikov a fost de numai 3,5...11,0 kW.
În 1934, un grup de ingineri condus de P.P. Shumilov a propus un nou turboforator, care era fundamental diferit de turboforinatorul Kapelyushnikov. Acesta prevedea o turbină special concepută în mai multe trepte, numărul de trepte în care a ajuns la 100 ... 150 buc. Acest lucru a făcut posibilă creșterea puterii turboburătorului și reducerea vitezei de rotație a turbinei la 8,3 ... 11,7 rotații / s, eliminând astfel necesitatea unei cutii de viteze.
Primele experimente de foraj cu un turboforator în mai multe etape, efectuate în 1935-1936, au confirmat toate avantajele noului design. Lucrările ulterioare privind crearea unui turboforator pentru forarea puțurilor au fost efectuate în principal de-a lungul liniei de îmbunătățire a designului. Această lucrare s-a încheiat în 1939-1940. crearea unui turboforator de tip industrial.
Din 1944, metoda de foraj cu turbine a fost utilizată pe scară largă în majoritatea regiunilor petroliere. În anii postbelici, forarea cu turbine a devenit unul dintre principalele tipuri de foraj în Uniunea Sovietică.
Designul turboforatoarelor este în mod constant îmbunătățit. Sunt dezvoltate noi tipuri de motoare hidraulice de fund. Deci, în a doua jumătate a anilor ’60. a fost dezvoltat un motor cu șurub (de deplasare) în fond de gaură, care este utilizat pe scară largă în prezent.
În 1937-1938. Un grup de ingineri condus de A.P. Ostrovsky a dezvoltat proiectarea unui motor nehidraulic pentru fundul de groapă - un burghiu electric. În 1940, au fost efectuate primele teste în câmpurile petroliere din Azerbaidjan, care au arătat oportunitatea utilizării sale la forarea puțurilor. În viitor, designul burghiului electric a fost îmbunătățit semnificativ, ceea ce a făcut posibilă utilizarea cu succes în unele regiuni ale țării.
Anii postbelici au fost marcați de o creștere semnificativă a pătrunderii, îmbunătățirea proiectării uneltelor echipamentelor de foraj, creșterea puterii de antrenare a instalațiilor de foraj, îmbunătățirea în continuare a tehnologiei de forare a puțurilor etc.
În ciuda faptului că în prezent în țara noastră mai mult de 90% din volumul total de foraj este realizat cu motoare de foraj, posibilitățile potențiale de foraj rotativ sunt departe de a fi epuizate, după cum o dovedește experiența străină.
Timp de un secol și jumătate, omenirea a forat puțuri pentru petrol și gaze. Adâncimea maximă a puțului a fost atinsă - mai mult de 12.000 m (Federația Rusă, putul Kola superadânc). Acest lucru mărturisește dificultățile tehnice enorme cu care trebuie să le înfrunți pe măsură ce mergi mai adânc în măruntaiele Pământului. Tehnica și tehnologia de foraj descrise în acest manual vor face posibilă atingerea adâncimii de 15.000 ... 16.000 m, ceea ce se va face în următoarele decenii.
Terminologie. Studiind acest manual, cititorul va întâlni o serie de concepte (termeni) care se întâlnesc doar în producția de foraj de sondă. Nu există atât de multe astfel de concepte, dar trebuie să le cunoașteți și, cel mai important, să le înțelegeți sensul. Principalii acestor termeni sunt prezentați mai jos.
Forajul este procesul de formare a unei mine care lucrează, în principal cu secțiune transversală circulară, prin distrugerea rocilor în principal cu o unealtă de foraj (mai rar prin metode termice, hidroerozive, explozive și alte metode) cu îndepărtarea produselor de distrugere.
Puț (petrol, gaz, apă etc.) - o structură, predominant de secțiune transversală circulară, formată prin forare și prindere și caracterizată printr-o suprafață relativ mică secțiuni transversale comparativ cu dimensiunea suprafeței laterale și cu o poziție predeterminată în spațiu.
Instrument de foraj - denumirea generală a mecanismelor și dispozitivelor utilizate în forarea puțurilor și eliminarea accidentelor care au loc în puțuri.
Metoda de forare cu impact -- o metodă de construcție a puțului prin distrugerea rocilor din cauza impactului unui instrument de tăiere a rocii pe fundul (partea de jos) a puțului.
Metoda rotativă de foraj este o metodă de construire a puțurilor prin distrugerea rocilor prin rotirea unei unealte de tăiere a rocii apăsată pe fund (daltă, bit).
Fluidul de foraj (fluid de spălare) este denumirea tehnologică pentru un sistem complex dispersat multicomponent de suspensie și fluide aerate utilizate în puțurile de spălare în timpul forajului.
Conducte de tubaj - conducte concepute pentru tubularea sondei, precum și izolarea orizonturilor productive în timpul funcționării unui rezervor (orizont) de petrol (gaz).
Carcasă - un șir format din țevi de carcasă înșurubate secvențial (sudate).
Spațiu inelar - spațiul dintre pereții puțului (șir de tubaj) și pereții exteriori ai șirului de țevi de foraj, format în timpul forajului.
Foraj exploratoriu - foraj de sonde în scopul explorării zăcămintelor de petrol (gaze). Face parte dintr-un set de lucrări care permite evaluarea valorii comerciale a unui zăcământ de petrol (gaze) identificat în etapa de explorare și pregătirea lui pentru dezvoltare.
Foraj operațional - foraj de puțuri în scopul dezvoltării unui zăcământ de petrol (gaze).
Turbodrill este un motor hidraulic de foraj conceput pentru forarea puțurilor în diferite condiții geologice.
Metoda de foraj cu turbine - forarea puțurilor cu ajutorul turboforajelor.
Un burghiu electric este o mașină de găurit condusă de energie electrică și care conferă mișcare de rotație unei scule de tăiat roci.
Cimentarea (astuparea) unui puț este injectarea unei suspensii de ciment în spațiul inelar dintre pereții puțului și șirul de tubaj.
Coarda de foraj este un arbore tubular în trepte care conectează burghiul (uneltă de tăiat roci) cu echipamentul de suprafață (instalație de foraj) atunci când se forează un puț.
Stand de foraj -- parte a garniturii de foraj, dintr-o bucată în timpul operațiunilor de declanșare; constă din două, trei sau patru țevi de foraj înșurubate împreună.
O instalație de foraj este un set de mașini și mecanisme concepute pentru forarea și tubularea puțurilor.
O instalație de foraj este o structură instalată deasupra unei găuri de foraj pentru coborârea și ridicarea sculelor de foraj, a motoarelor de foraj și a țevilor de carcasă.
Drawworks -- un mecanism conceput să coboare și să ridice șirul țevii de foraj, să alimenteze burghiul în fundul puțului, să coboare carcasa, să transfere puterea rotorului.
Sistem de rulare (polispast) al instalațiilor de foraj - o serie de mecanisme (bloc coroană, bloc de călătorie, cârlig sau bloc de cârlig) care transformă mișcarea de rotație a tamburului troliului în mișcare de translație (verticală) a cârligului.
Rotor - un mecanism conceput pentru a transmite rotația șirului de foraj în timpul forajului, pentru a-l menține pe greutate în timpul operațiunilor de declanșare și a lucrărilor auxiliare.
Un pivot este un mecanism care rotește un șir de foraj suspendat pe un cârlig și alimentează fluidul de foraj prin acesta.
Pompa de noroi este o mașină hidraulică pentru pomparea lichidului de spălare într-o gaură de foraj.
Platformă de foraj -- instalație de foraj în zone de apă în scopul explorării sau exploatării resurselor minerale de sub fundul mării.
Acționarea puterii instalației de foraj este un set de mașini și mecanisme concepute pentru a converti energia electrică sau energia combustibilului în energie mecanică.
Sita vibrantă (sită vibrantă) - un mecanism pentru curățarea fluidului de foraj (fluid de spălare) de butași și alte impurități mecanice.
Reactivi chimici - diverși substanțe chimice concepute pentru a controla proprietățile fluidelor de foraj (fluid de spălare).
Un kelly este o conductă, de obicei de secțiune pătrată, care este montată deasupra garniturii de foraj și transmite rotația de la rotor la acesta.
Kelly Pit - O fântână de mică adâncime construită în apropierea rotorului și proiectată să coboare Kelly în timpul încorporarii țevii de foraj în perioadele fără foraj.
Burghiu conic -- un mecanism constând din conuri sferice sau cilindrice montate pe lagăre de rulare sau alunecare (sau combinații ale acestora) pe toroane ale secțiunilor burghiului.
Burghiu cu lame - un corp cu un fir de legătură, la care sunt sudate trei sau mai multe lame.
Țevile de foraj sunt partea principală a garniturii de foraj. Țevile de foraj sunt realizate fără sudură, din oțeluri carbon sau aliate.
Încuietori de foraj (încuietori pentru țevi de foraj) - un element de legătură al țevilor de foraj pentru înșurubarea lor într-o coloană. Articulația de foraj este formată dintr-un niplu și un manșon fixat la capetele țevii de foraj.
Colierele de foraj (DC) sunt țevi concepute pentru a crea o sarcină pe unealta de tăiere a rocii și pentru a crește rigiditatea părții inferioare a garniturii de foraj.
Indicatorul de masă (greutate) este un dispozitiv prin care se determină sarcina axială pe burghiu în timpul procesului de găurire. Acest dispozitiv determină și sarcina care acționează asupra cârligului sistemului de deplasare.
Cei de mai sus sunt doar termenii principali utilizați pe scară largă în forarea sondelor de petrol și gaze. Un specialist de orice nivel implicat în forarea sondelor de petrol și gaze ar trebui să cunoască fluent această terminologie.
CAPITOLUL 1 REZUMAT DE GEOLOGIE GENERALĂ ŞI PETROLIERĂ
1.1 Concepte de bază despre structura și compoziția scoarței terestre
Pământul este format din învelișuri concentrice (geosferă): exteriorul sau scoarța terestră, intermediarul sau mantaua și miezul. Granița dintre scoarța terestră și manta este suprafața lui Mohorovichich, care se află la o adâncime de 30 ... 70 km pe continent și 5 ... 10 km sub fundul oceanului. Limita dintre manta si nucleu este situata la o adancime de 2900 km. Miezul, cu o rază de 3400 km, este situat în centrul Pământului. Se presupune că miezul este format în principal din fier și nichel. Densitatea materiei din ea este de 6 ... 11 g / cm 3, iar presiunea în centrul Pământului este de 4263000 kg / cm 2.
Scoarța terestră nu a fost pe deplin explorată. Se crede că nivelul său inferior este stratul de bazalt. Un covor de bazalt gros este un așternut pe care se sprijină un strat de granit, acoperit cu o acoperire de roci sedimentare. Cu toate acestea, scoarța terestră nu are peste tot o structură cu trei niveluri. De exemplu, fundul oceanului este alcătuit dintr-un strat de bazalt și un strat foarte subțire de roci sedimentare. Și în unele locuri, granitele ies direct la suprafață.
Scoarța terestră este compusă dintr-o varietate de roci, formate din minerale. După origine, rocile sunt împărțite în trei grupe principale: magmatice, sedimentare și metamorfice.
Rocile magmatice se formează din magmă Magma este substanța Pământului, care se află în stare topită. când se solidifică la o anumită adâncime (roci adânci sau intruzive) sau când este turnată la suprafață sub formă de lavă (roci turnate sau efuzive). Majoritatea acestor roci au o structură cristalină; ele se află în scoarța terestră, de regulă, nu în straturi, ci sub formă de corpuri de formă neregulată.
Rocile sedimentare se formează din produsele distrugerii rocilor preexistente depuse în bazine de apă sau pe suprafața terenului sub formă de precipitații mecanice și chimice; această grupă include și rocile sedimentare formate din deșeurile organismelor (sedimente organice). Rocile sedimentare, de regulă, apar în scoarța terestră sub formă de straturi.
Rocile metamorfice sunt formate din roci magmatice sau sedimentare care au suferit presiuni și temperaturi ridicate în intestinele scoarței terestre. Aceste roci diferă în cele mai multe cazuri prin stratificare și structura cristalină.
În scoarța terestră, rocile magmatice ocupă 95%. Toate rocile sedimentare și metamorfice reprezintă doar 5%. Cu toate acestea, suntem interesați de rocile sedimentare, deoarece zăcămintele de petrol și gaze sunt limitate la acestea din urmă. foraj de câmp petrolier
1.2 Pliere și tipuri de pliuri
Rocile sedimentare au fost inițial depuse în straturi orizontale numite strate. În viitor, ca urmare a construcției montane, i.e. sub presiunea forțelor laterale și verticale care zdrobesc straturile orizontale, s-au format pliuri. Uneori au fost rupturi ale straturilor, cele mai în vârstă înaintând pe cele mai tinere și chiar ieșind la suprafață. Formarea pliurilor, spargerilor și a altor terenuri denivelate, fenomenele vulcanice, cutremure și alte manifestări ale vieții interne a Pământului se numesc mișcări tectonice.
Există multe fenomene fizice care ar putea provoca mișcarea tectonice. Mobilitatea binecunoscută a substanțelor din intestinele Pământului la o adâncime de aproximativ 800 ... 1000 km ar trebui considerată un fapt stabilit. Motivele pentru aceasta sunt o varietate de procese fizice și chimice care au loc pe Pământ. Aceste procese ar trebui luate în considerare în interrelație, ținând cont de dezvoltarea lor istorică.
Luați în considerare mai multe forme de pliuri ale scoarței terestre. Pliurile care se umflă în sus se numesc anticlinale, iar pliurile care se umflă în jos se numesc sinclinale. Partea cea mai ridicată a anticlinalului se numește dom, părțile laterale sunt numite aripi (Fig. 1.1, a).
Dacă apare o defecțiune cu formarea unei fisuri, de-a lungul căreia straturile se mișcă în direcții verticale și oblice unul față de celălalt (Fig. 1.1, b), și în același timp o parte a pliului coboară, în timp ce cealaltă rămâne în în același loc, atunci se formează o falie. Dacă o parte a pliului se ridică și se suprapune oarecum pe cealaltă, atunci se formează o eroare inversă.
Principalele elemente care caracterizează așternutul sunt: dip, dip, dip și strike.
Căderea straturilor este înclinarea straturilor scoarței terestre spre orizont. Cel mai mare unghi (a) format de suprafața rezervorului cu un plan orizontal se numește unghiul de scufundare al rezervorului (Fig. 1.1, c). O linie situată în planul rezervorului și perpendiculară pe direcția înclinării acestuia se numește lovitura rezervorului.
Suprafața superioară a rezervorului (limita cu rezervorul de deasupra) se numește acoperiș, cea inferioară este talpa. Distanța dintre partea de sus și de jos se numește grosimea formațiunii.
1.3 Principalele proprietăți fizice și mecanice ale rocilor care afectează procesul de distrugere a acestora în timpul construcției puțului
Principalele proprietăți fizice și mecanice ale rocilor care afectează procesul de distrugere a acestora în timpul construcției puțului sunt elasticitatea și plasticitatea, duritatea, abrazibilitatea și continuitatea.
Proprietățile elastice ale rocilor. Toate rocile aflate sub influența sarcinilor externe suferă deformații care dispar după îndepărtarea sarcinii sau rămân. Prima dintre ele se numește deformații elastice, iar a doua - plastică. Majoritatea mineralelor care formează roci sunt corpuri elastice fragile, adică se supun legii lui Hooke și se descompun atunci când tensiunile ating limita elastică. La o simplă întindere sau compresie a unui corp elastic, alungirea sau compresia relativă este proporțională cu solicitarea normală:
unde E este modulul lui Young; e - deformare.
Rocile sunt corpuri elastice fragile și respectă legea lui Hooke numai în cazul aplicării unei sarcini dinamice. Proprietățile elastice ale rocilor se caracterizează prin modulul de elasticitate (modulul Young) E și raportul lui Poisson p, (d = e x / e i unde e x este deformația transversală; J y este deformația longitudinală). Modulul elastic al rocilor depinde de compoziția mineralogică a acestora, de tipul de încărcare și de mărimea sarcinii aplicate, de structura, textura și adâncimea rocilor, de compoziția și structura substanței de cimentare în rocile clastice, de gradul de umiditate, de nisip. și conținutul de carbonat al rocilor.
Raportul lui Poisson pentru majoritatea rocilor și mineralelor este în intervalul 0,2 ... 0,4 și numai pentru cuarț este anormal de scăzut - aproximativ 0,07, ceea ce se datorează particularităților structurii rețelei sale cristaline.
Proprietățile plastice ale rocilor (plasticitatea). Distrugerea unor roci este precedată de deformarea plastică, care începe atunci când solicitarea din rocă depășește limita elastică. Plasticitatea depinde de compoziția mineralogică a rocilor și scade odată cu creșterea conținutului de cuarț, feldspat și alte minerale. Argilele și rocile care conțin săruri au proprietăți plastice ridicate. În anumite condiții, unele roci sunt supuse furajului. Fluajul se manifestă printr-o creștere constantă a deformării la o solicitare constantă. Fluaj semnificativ este caracteristic pentru argile, șisturi argiloase, roci de sare, noroi și unele soiuri de calcare.
Duritatea rocilor. Duritatea rocii este înțeleasă ca fiind capacitatea sa de a rezista pătrunderii (introducerii) în ea a unei scule de tăiere a rocii.
În geologie, scara de duritate minerală Mohs este utilizată pe scară largă, conform căreia duritatea condiționată a mineralelor este determinată de metoda de zgâriere. Această scară se bazează pe duritatea mineralelor găsite cel mai des în rocă, iar celor mai puțin dure dintre ele li se atribuie numere mai mici:
1 - talc;
2 - gips sau sare gema;
3 - spatar calcaros sau calcit;
4 - spat fluor;
5 - apatită;
6 - feldspat;
7 - cuarț;
8 - topaz;
9 - corindon; 10 este un diamant.
Pe baza a numeroase studii, L. A. Shreiner a propus o clasificare a rocilor care diferă de scala de duritate Mohs prin faptul că ține cont cel mai pe deplin de principalele proprietăți fizice și mecanice ale rocilor care afectează procesul de foraj (Tabelul 1.1).
Grupa I include roci care nu dau fractură generală fragilă (nisipuri slab cimentate, lut, rocă calcaroasă, marne, argile cu interstraturi frecvente de gresii, marne etc.). Grupa II cuprinde roci elastic-plastice (șisturi, calcare dolomitice, anhidrite puternice, dolomite, conglomerate pe ciment silicios, roci cuarț-carbonatice etc.). Grupa III include roci elastice-cascante, mai ales magmatice și metamorfice.
De regulă, în funcție de duritatea rocilor implicate în formarea zăcămintelor de petrol, acestea aparțin primelor opt categorii.
Tabelul 1.1
Clasificarea rocii Schreiner
Abrazivitatea rocilor. Abrazivitatea rocii este înțeleasă ca capacitatea sa de a uza unealta de tăiere a rocii în contact cu aceasta în procesul de interacțiune a acestora. Abrazivitatea rocilor se manifesta in procesul de uzura abraziva (in principal mecanica) si este caracteristica acesteia. Prin urmare, indicatorii de abraziune pot fi considerați indicatori ai proprietăților mecanice ale rocilor.
Abrazivitatea unei roci, ca orice alt indicator al proprietăților mecanice, reflectă comportamentul acesteia în condiții specifice de încercare sau de lucru. Conceptul de capacitate abrazivă este strâns legat de conceptul de frecare externă și uzură. Proprietățile abrazive ale rocilor nu au fost suficient studiate. Frecarea este afectată semnificativ de mediu. Coeficientul de frecare împotriva rocii, a cărei suprafață este umezită cu soluție de argilă, este mai mic decât același coeficient de frecare împotriva rocii umezite cu apă și este semnificativ mai mic decât coeficientul de frecare împotriva rocii uscate.
Dintre roci, gresiile și siltstones de cuarț și feldspat (roci cimentate cu granule clastice variind ca mărime de la 0,01 la 0,1 mm) au cea mai mare abraziune. Au fost elaborate mai multe clasificări pentru abrazivitatea rocilor.
Continuitatea rocilor. Acest concept a fost propus pentru a evalua starea structurală a rocilor și capacitatea acestora de a transmite impacturi în interiorul rocii, de exemplu, presiunea unui mediu lichid sau gazos extern. Gradul de adecvare pentru un astfel de impact este determinat de tulburările intrastructurale din rocă (fisuri, pori, suprafețe de contact liber de boabe etc.).
1.4 Formarea uleiului și acumularea de ulei
Teoria originii petrolului este de mare importanță, deoarece face posibilă căutarea în mod rezonabil a zăcămintelor de petrol și gaze. În prezent, există două teorii: organică și anorganică.
Teoria originii organice a uleiului se bazează pe următoarele.
După moartea unui organism animal sau vegetal, începe procesul de descompunere a acestuia. Dacă apare cu acces liber al oxigenului, atunci marea majoritate a carbonului organismelor vegetale și animale revine în atmosferă sub formă de dioxid de carbon, iar uleiul conține 86% carbon. În acest caz, doar o mică parte din reziduurile organice intră în condiții favorabile pentru conservarea lor.
Dacă nu există oxigen, descompunerea are loc datorită activității vitale a bacteriilor - microorganisme care pot trăi fără oxigen. Rolul acestor bacterii se reduce la extracția oxigenului și formarea de compuși organici stabili (materia de pornire pentru formarea uleiului).
Zonele cele mai favorabile pentru acumularea sursă de material organic pentru petrol sunt estuarele (golurile), lagunele (lacuri legate de mare printr-o strâmtoare îngustă), estuarele (gurile adânci în formă de pâlnie ale râurilor care se varsă în mare).
Teoria originii anorganice a uleiului este următoarea.
Petrolul provine din mantaua Pământului, unde s-a înțeles cu alte componente în timpul formării planetei dintr-un nor de gaz și praf și materie detritică. Eliberarea și acumularea inițială de hidrocarburi petroliere este asociată cu procese din partea superioară a mantalei Pământului, care sunt cauza mișcărilor tectonice. Mișcarea petrolului din zonele de acumulare a acestuia în regiunea subcrustală în capcane - depozite situate în orizonturile superioare ale scoarței terestre, are loc de-a lungul cavităților părților superioare ale falilor adânci, care traversează straturile de bazalt, granit și sedimentare. a scoarţei terestre.
Teoriile existente despre originea petrolului se bazează pe presupunerea că petrolul din stratul părinte migrează (este stors) din stratul părinte din cauza creșterii presiunii rocilor în depozitele de rocă din apropiere, cu permeabilitate mai mare și umplute cu apă. În același timp, petrolul și gazul deplasează apa și se adună în partea cea mai ridicată a structurii sau în zonele închise de depozite impermeabile, care opresc mișcarea ulterioară a lichidului, formând un rezervor de petrol.
Un rezervor de petrol este un rezervor compus din roci cu permeabilitate suficientă și umplut cu ulei. Petrolul, gazul și apa sunt în rezervoare sub presiune ridicată. Rocile aflate deasupra orizontului productiv pun presiune asupra acestui strat cu masa lor. Înainte de deschiderea orizontului productiv, presiunea din acesta pe toată suprafața este uniformă, în momentul deschiderii acestuia, acest echilibru este perturbat și, dacă presiunea asupra rezervorului din straturile de deasupra depășește presiunea din coloana de lichid. umplerea fântânii începe curgerea.
Nivelurile fluidelor din puțuri pot fi statice sau dinamice. Nivelul static caracterizează presiunea rezervorului. Dinamic este nivelul lichidului, care se stabilește în puț atunci când lichidul este adăugat sau pompat. Acest nivel caracterizează presiunea din fundul puțului în timpul funcționării acestuia.
1.5 Căutarea, explorarea și dezvoltarea zăcămintelor
Prospectarea și explorarea reprezintă un set de lucrări pentru descoperirea zăcămintelor minerale și evaluarea adecvării acestora pentru dezvoltarea industrială.
Principalele probleme în explorarea zăcămintelor minerale sunt următoarele:
determinarea formei şi volumului părţii industriale a zăcământului. În funcție de mărimea părții studiate a zăcământului, se calculează anumite rezerve minerale;
stabilirea caracteristicilor calitative ale unui mineral în strânsă legătură cu cerințele tehnice pentru materiile prime;
identificarea factorilor naturali care determină condițiile de funcționare (compoziția și relația rocilor care înconjoară depozitul, unghiurile de scufundare ale rocilor, udarea zăcământului, duritatea și fracturarea rocilor etc.).
Dezvoltarea unui zăcământ de petrol înseamnă controlul procesului de deplasare a lichidului sau gazului din rezervor către fundul puțurilor de producție. Un sistem rațional de dezvoltare a unui zăcământ de petrol este acela în care acesta este forat cu numărul minim admis de puțuri, care asigură rate ridicate de recuperare a petrolului din rezervor, recuperare finală ridicată a petrolului, investiții minime de capital pe tonă de rezerve recuperabile și costul minim al petrolului.
Grosimea straturilor productive ale câmpurilor petroliere poate varia de la câteva zeci la sute și mii de metri. Depozitele multistrat sunt dezvoltate conform sistemului de jos în sus, când straturile sunt puse în producție secvenţial, începând de la orizontul inferior spre cel superior. Orizontul de la care începe dezvoltarea se numește referință sau de bază. Un astfel de sistem permite, în timpul forajului până la orizontul de bază, prin selectarea solurilor și aplicarea metodelor geofizice, studierea tuturor formațiunilor petroliere supraiacente și, în același timp, pregătirea acestora pentru dezvoltare. Contribuie la reducerea numărului de sonde de explorare în câmp și la scăderea procentului de sonde de producție nereușite, întrucât puțurile în care nu s-a obținut petrol la orizontul de bază pot fi returnate în formațiunile supraiacente. Toate acestea reduc valoarea costurilor de capital pentru forarea sondelor operaționale și în special de explorare.
Straturile de deasupra sunt puse în funcțiune după epuizarea completă a orizontului de referință. Pentru a reduce acest decalaj și, în consecință, a asigura producția maximă de petrol într-un timp scurt, se lucrează pentru a opera simultan mai multe orizonturi. Un rol important în îmbunătățirea eficienței dezvoltării zăcământului petrolier l-a jucat utilizarea pe scară largă a stimulării artificiale a rezervoarelor în scopul menținerii sau refacerii energiei rezervorului. Pentru a face acest lucru, gazul (aerul) este pompat în părțile înalte ale rezervorului sub presiunea gazului și modurile de gaz ale zăcămintei sau apă în zonele acvifere în modul condus de apă.
Să ne oprim asupra metodelor de exploatare a puțurilor de petrol.
Procesul de ridicare a petrolului sau gazului de pe fundul sondei la suprafața de zi poate apărea atât datorită energiei naturale a lichidului și gazului care vine pe fund, cât și datorită energiei introduse în puț de la suprafața zilei. Dacă petrolul și gazele sunt furnizate la suprafața zilei din cauza energiei naturale sau a inundațiilor, atunci operația se numește curgere. Dacă puțul nu curge deloc sau debitul său este insuficient, se folosește pomparea mecanică a petrolului din puț. Acest lucru se realizează prin funcționarea compresorului sau a pompei. În timpul funcționării compresorului, în puț se injectează gaz sau aer comprimat, care intră în sabotul țevilor de ridicare coborâte în puț, se amestecă cu ulei și aduce acest amestec la suprafață. Operare de pompare Se folosește de obicei în puțuri cu un debit mic.
Întrebări de control
1. Care sunt principalele roci ale scoarței terestre?
2. Ce roci se numesc sedimentare?
3. Enumeraţi principalele forme ale pliurilor scoarţei terestre.
4. Care este duritatea și abrazibilitatea rocilor?
5. Care este esența teoriilor despre originea organică și anorganică a uleiului?
6. Ce forțe fac ca petrolul să se deplaseze din rezervor în puțuri?
7. Care sunt principalele întrebări ridicate în timpul explorării?
8. Ce sistem de dezvoltare se numește rațional?
9. Descrieți modul în care sunt exploatate puțurile de petrol.
CAPITOLUL 2 INFORMAȚII GENERALE DESPRE FORAREA FUTURILOR ȘI ECHIPAMENTELE UTILIZATE PENTRU IMPLEMENTAREA ACEST PROCES
2.1 Conceptul de foraj, clasificarea și scopul puțurilor
Fântâna este creată prin distrugerea secvențială a rocilor și extragerea lor la suprafață. Începutul fântânii se numește gura, fundul fântânii se numește fund. Diametrul puțului este în intervalul 59... 1000 mm. În timpul forajelor convenționale, întreaga masă a rocii este distrusă. La foraj cu selecția unei coloane interne de rocă (miez), doar spațiul inelar din apropierea pereților puțului este distrus, iar miezul este extras în stare intactă pentru a studia structura geologică a zăcământului.
Scopul puțurilor poate fi diferit. Toate sondele forate în scopul cercetării regionale, prospectării, explorării și dezvoltării zăcămintelor sau zăcămintelor de petrol și gaze sunt împărțite în următoarele categorii.
1. Se forează sonde de referință pentru a studia structura geologică și condițiile hidrogeologice ale regiunilor mari, pentru a determina modelele generale de distribuție a complexelor de sedimente favorabile acumulării de petrol și gaze, în vederea selectării celor mai promițătoare zone de explorare geologică pentru petrol și gaze. .
2. Se forează sonde parametrice pentru studiul structurii geologice adânci și evaluarea comparativă a potențialului de petrol și gaze ale posibilelor zone de acumulare de petrol și gaze, pentru a identifica zonele cele mai promițătoare pentru lucrări geologice detaliate, precum și pentru a obține informațiile necesare despre situația geologică. și caracteristicile geofizice ale secțiunii de sedimente pentru a clarifica rezultatele studiilor seismice și ale altor studii geofizice .
3. Sondele structurale sunt forate pentru identificarea și pregătirea pentru prospectarea și forajul exploratoriu a zonelor promițătoare (pliuri anticlinale, zone de screening, înghețare etc.). Conform datelor obținute în urma forării puțurilor structurale, se determină elementele de apariție a straturilor (tectonică, stratigrafie și litologie) în diferite puncte și se întocmesc profile ale acestei zone.
4. Sondele de explorare se forează în zonele pregătite prin prospectare geologică (studiu geologic, foraj structural, studii geofizice și geochimice sau o combinație a acestor metode) în vederea stabilirii conținutului de petrol și gaze.
5. Sondele de explorare sunt forate în zone cu conținut comercial stabilit de petrol și gaze pentru a delimita câmpul, a calcula rezervele și a-l pregăti pentru dezvoltare.
6. Se forează puțuri de producție pentru dezvoltarea și exploatarea zăcămintelor de petrol și gaze. Această categorie include evaluarea (pentru evaluarea rezervoarelor de orizonturi productive), producerea (producția), injectarea (pentru injectarea apei, aerului sau gazelor în orizonturile productive în scopul menținerii presiunii rezervorului și extinderii perioadei de curgere naturală) și observarea (control, piezometric). ) puţuri. În aceeași categorie sunt incluse puțurile concepute pentru stimularea termică a rezervorului în timpul dezvoltării depunerilor cu uleiuri cu vâscozitate ridicată.
7. Se forează puțuri speciale pentru evacuarea apelor industriale, eliminarea fântânilor deschise de petrol și gaze, pregătirea structurilor pentru depozitele subterane de gaze și injectarea gazelor în acestea, explorarea și producerea apelor industriale.
Forarea puțurilor este folosită nu numai în industria petrolului și gazelor. De asemenea, se forează puțuri în scopul explorării și extragerii altor minerale, aprovizionării cu apă pentru așezări, stingerea incendiilor subterane, gazificarea cărbunelui, ventilarea minelor, înghețarea solului în timpul scufundării minei, investigarea solului la locul construcției propuse a diferitelor structuri industriale si civile etc.
2.2 Schema tehnologică a forării puțurilor în mod rotativ
Metodele de foraj pot fi clasificate în funcție de natura impactului asupra rocilor: mecanice, termice, fizico-chimice, electrospark etc. Numai metodele asociate cu impactul mecanic asupra rocilor sunt utilizate pe scară largă; restul nu au părăsit stadiul de dezvoltare experimentală.
Găurirea mecanică se realizează prin metode de percuție, rotație și percuție-rotație (aceasta din urmă metodă are până acum o utilizare foarte limitată). Forarea cu impact a sondelor de petrol și gaze, încă obișnuită în multe țări, nu a fost folosită în zăcămintele de petrol și gaze de câteva decenii Federația Rusă. La forarea puțurilor de petrol și gaze în Rusia, se folosește doar forajul rotativ. Cu această metodă de foraj, puțul este, parcă, forat cu un bit care se rotește continuu. Particulele de rocă forate în timpul procesului de foraj sunt aduse la suprafață printr-un jet de fluid de foraj care circulă continuu sau cu aer sau gaz injectat în puț. În funcție de locația motorului, găurirea rotativă este împărțită în găurire rotativă - motorul este situat la suprafață și rotește burghiul în partea de jos folosind o garnitură de foraj și găurirea cu un motor de foraj (burghiu hidraulic sau electric) - motorul este mutat în fundul puțului și este instalat deasupra dalții.
Procesul de foraj constă în următoarele operații: declanșare (coborârea țevilor de foraj cu un burghiu în puț până la fund și ridicarea țevilor de foraj cu un burghiu uzat din puț) și prelucrarea burghiului la fund (distrugerea rocii de către pic). Aceste operațiuni sunt întrerupte periodic pentru a trece conductele de tubaj în puț pentru a proteja pereții sondei de prăbușiri și pentru a separa orizonturile de petrol (gaz) și apă. În același timp, în timpul forării sondei se efectuează o serie de lucrări auxiliare: prelevarea de probe de miez, pregătirea fluidului de spălare (nămol de foraj), exploatare, măsurarea curburii, dezvoltarea sondei pentru a provoca afluxul de petrol (gaz) în sondă etc. În cazul unui accident sau complicație (defalcare țevi de foraj, scule de lipire etc.) este nevoie de lucrări suplimentare (de urgență). Pentru a efectua operațiunile de mai sus în procesul de forare a unui puț, se folosește o instalație de foraj (Fig. 2.1).
Țeava cea mai de sus din șirul de foraj nu este rotundă, ci pătrată (poate fi și hexagonală sau canelată). Se numește Kelly. Conducta de conducere trece prin orificiul mesei rotunde - rotorul, iar la forarea puțului, pe măsură ce gaura de fund se adâncește, coboară.
Rotorul este plasat în centrul instalației de foraj. Țevile de foraj și Kelly sunt goale în interior. Conducta de conducere este conectată la pivotul cu capătul său superior. Partea inferioară a pivotului, conectată la kelly, se poate roti cu șirul de foraj, în timp ce partea superioară este întotdeauna staționară.
Un furtun flexibil este conectat la orificiul (gâtul) părții fixe a pivotului, prin care, în timpul forării, fluidul de spălare este pompat în puț cu ajutorul pompelor de foraj. Acesta din urmă, după ce a trecut Kelly și întreaga garnitură de foraj, intră în burghie și se repezi prin găurile din acesta până la fundul puțului (când forează cu un motor hidraulic, fluidul de spălare intră mai întâi în el, antrenând arborele motorului în rotație. , și apoi în bit). Ieșind din găurile din burghie, fluidul spălă fundul găurii, preia particulele de rocă forate și împreună cu acestea se ridică prin spațiul inelar dintre pereții sondei și țevile de foraj, unde merge la admisia pompei, fiind anterior. curățat de particule de rocă forate pe drum.
...Documente similare
manual, adăugat la 12.02.2010
Studiul proceselor tehnologice de foraj de puțuri de petrol și gaze pe exemplul NGDU "Almetyevneft". Caracteristicile geologice și fizice ale obiectelor, dezvoltarea câmpurilor petroliere. Metode de creștere a productivității puțurilor. Ingineria sigurantei.
raport de practică, adăugat la 20.03.2012
Metode primare, secundare și terțiare de dezvoltare a zăcămintelor de petrol și gaze, esența și caracteristicile acestora. Ei bine și tipurile sale. Foraj direct (orizontal). Deviația artificială a puțurilor. Forarea sondelor pentru petrol si gaze.
lucrare de termen, adăugată 18.12.2014
O scurtă istorie a dezvoltării afacerii cu petrol și gaze. Conceptul și scopul puțurilor. Caracteristicile geologice și de câmp ale straturilor productive. Fundamentele dezvoltării zăcămintelor de petrol și gaze și exploatarea acestora. Luarea în considerare a metodelor de recuperare îmbunătățită a uleiului.
raport de practică, adăugat la 23.09.2014
Tehnologia forării puțurilor de petrol și gaze. Modele de distrugere a rocilor. Capete de burghiu. Snur de foraj, elementele sale. Înroșirea bine. Motoare cu turbine și șuruburi în fundul gropii. Particularitățile forajului puțurilor la echilibrul „formarea puțurilor”.
prezentare, adaugat 18.10.2016
Studiul principalelor metode de forare a puțurilor de petrol și gaze: motoare rotative, hidraulice de foraj și forare cu burghie electrice. Caracteristicile cauzelor și consecințelor curburii puțurilor verticale, curbura naturală a axei puțurilor.
lucrare de termen, adăugată 15.09.2011
Criterii de alocare a facilităţilor operaţionale. Sisteme de dezvoltare a câmpurilor petroliere. Amplasarea puțurilor peste zona depozitului. Revizuirea metodelor de creștere a productivității puțurilor. curent şi revizuire fântâni. Colectarea si prepararea petrolului, gazelor, apei.
raport de practică, adăugat la 30.05.2013
Esența procesului de foraj, scopul și tipurile de foraje. Reguli pentru proiectarea, instalarea și exploatarea instalațiilor de foraj pentru forarea puțurilor de petrol și gaze. Importanța respectării instrucțiunilor de siguranță la efectuarea operațiunilor de foraj.
lucrare de control, adaugat 02.08.2013
Proiectarea structurii sondelor de petrol: calculul adâncimii de coborâre a conductorului și parametrii profilului trunchiului. Selectarea echipamentelor pentru cap de sondă, moduri de foraj, soluții de cimentare și biți. Echipamente tehnologice de carcasă și corzi de producție.
teză, adăugată 19.06.2011
Informații generale despre obiectul industrial. Condițiile geografice și economice și structura geologică a zăcământului. Organizarea si producerea operatiilor de foraj. Metode de creștere a productivității puțurilor. Întreținere și revizie puțuri de petrol și gaze.