Что такое полимерное покрытие? Полимерное покрытие металла
Полимерное покрытие - это уникальная возможность защитить металлические поверхности. Это самый эффективный и современный способ борьбы с коррозией, которая рано или поздно все равно появляется на металлических изделиях.
В чем суть?
Для улучшения эксплуатационных свойств металла используются полимеры, которые могут вступать в реакцию в определенных условиях. Подобные покрытия представляют собой сухие составы на основе порошка мелкой дисперсии, куда дополнительно добавляются отвердители, наполнители и пигменты. Полимерное покрытие было выбрано для повышения защитных средств металла не случайно: металлы проводят электрический ток, как следствие, заряд передается изделию, в результате чего образуется Оно притягивает частицы порошка, удерживая их на поверхности обрабатываемого изделия. Особенность полимерного покрытия - в высокой степени устойчивости к любым видам воздействия. Кроме того, оно эстетично.
Как проходит полимеризация
Цех порошковой окраски состоит из нескольких участков:
- Участка подготовки изделий: чтобы полимерное покрытие было нанесено правильно и равномерно, металлическое изделие сначала тщательно очищается от пыли, ржавчины, грязи. Целесообразно использовать эффективную и фосфатирование. Обязательный этап - обезжиривание металлической поверхности.
- Камеры напыления: в окрасочной камере выполняется непосредственно покраска. Камера термическая, она способна нагреться до температуры в 200 градусов и прогревается равномерно. Порошок начинает плавиться, за счет чего образуется ровное и гладкое покрытие по всей поверхности металла, заполняются и его поры.
- Полимеризация изделия выполняется в камере охлаждения: здесь температура постепенно падает, а полимерная пленка становится тверже. Спустя 24 часа полимерное покрытие уже готово к эксплуатации.
Технология окраски: в чем суть
Нанесение порошкового покрытия выполняется в несколько этапов. На первом обрабатываются поверхности. Очень важно, чтобы металлические изделия были тщательно очищены от загрязнений, окислов, а обезжиривание поверхности будет способствовать улучшенной сцепляемости. После подготовки выполняется этап маскировки, то есть скрываются те элементы металлического изделия, на которые не должен попасть порошковый состав.
Детали, которые должны быть обработаны, завешиваются на транспортную систему, затем отправляются в камеру покраски. После напыления на металле образуется порошковый слой. На этапе полимеризации формируется покрытие, которое представляет собой оплавление слоя краски.
В чем особенности?
Металл, обработанный полимерным покрытием, отличается надежностью и повышенной прочностью. Объясняется это тем, что образуется герметичная монолитная пленка, полностью покрывающая поверхность изделия и прочно держащаяся на нем. Благодаря полимерному покрытию металл обладает:
- высокой адгезией к поверхности;
- высокой прочностью и износоустойчивостью;
- длительным сроком эксплуатации при сохранении первоначальных свойств;
- богатой цветовой гаммой;
- быстрым производственным циклом.
Полимерное покрытие металла выполняется на основе различных материалов и красящих порошков. Выбор конкретного вещества зависит от того, для каких целей наносится покрытие, насколько важны декоративные свойства.
Полиэстер
Для полимерного покрытия металла чаще всего используется именно полиэстер. Это недорогой материал, обладающий высоким уровнем гибкости, формуемости, к тому же он может эксплуатироваться в любых климатических условиях. Лист с полимерным покрытием на основе полиэстера отличается стойкостью к ультрафиолетовому излучению и коррозии. Материал образует качественную и прочную пленку на поверхности, благодаря чему при любых условиях транспортировки стальные листы доставляются в целости.
Широко используется и матовый полиэстер: покрытие имеет совсем маленькую толщину, а поверхность металла получается матовой. Особенность данного материала - в высокой цветостойкости, хорошей стойкости к коррозии и механическому воздействию.
Пластизоль
Еще одно популярное полимерное покрытие металла - пластизоль. В составе этого декоративного материала - поливинилхлорид, пластификаторы; внешне он привлекает внимание тисненой поверхностью. Это самое дорогое покрытие, и в то же время самое стойкое к механическим повреждениям благодаря большой толщине покрытия. С другой стороны, материал не обладает высокой температурной стойкостью, а потому под воздействием солнечных лучей при высокой температуре покрытие будет портиться. За счет большой толщины стойкость к коррозии пластизоля высокая.
Популярна сталь с полимерным покрытием на основе пурала, которая отличается шелковисто-матовой структурной поверхностью. Стойкость к перепадам температуры и воздействию химических веществ делает данный состав популярным для обработки металлов.
Характеристики стали с полимерным покрытием
Особенности материалов с полимерным покрытием - в прочности, формуемости, высокой коррозийной стойкости. После обработки сталь обретает прекрасный внешний вид, которому можно придать любые цвета и оттенки. Прокат выполняется по ГОСТ, полимерное покрытие получается качественным. Окрашенный прокат может иметь одно- или двухслойное покрытие, возможны варианты, когда вещество наносится с одной или с обеих сторон. Благодаря полимерному покрытию улучшаются эксплуатационные свойства стали:
- металл с полимерным покрытием может быть переработан в готовые изделия;
- покрытие распределяется по поверхности равномерно, поэтому и степень защиты равномерная;
- отсутствие пор служит залогом хорошего уровня защитных свойств;
- сталь отличается хорошей адгезией;
- металл может сохранять защитные и декоративные свойства больше 10 лет.
С экономической точки зрения сталь оцинкованная с полимерным покрытием более выгодна: во-первых, она способствует высокой производительности и качеству, так как снижается себестоимость нанесения покрытий. Во-вторых, покупателю не нужно самому вкладывать средства в дополнительную обработку стали для защиты ее поверхности. Отметим, что антикоррозионные свойства оцинкованной стали, которая обработана полимерным покрытием, зависит от толщины слоя. Чтобы повысить срок эксплуатации стальных изделий, они дополнительно покрываются двумя слоями полимера, что делает защиту металла еще выше.
Особенности покрытия
Полимерное покрытие - это пленка, которая обладает целым комплексом уникальных эксплуатационных характеристик. Предварительно окрашенный прокат создается на основе нескольких типов полимеров. Любой материал, обработанный на основе такого метода - стальной лист или сетка с полимерным покрытием - отличается ударопрочностью, стойкостью к воздействию коррозии и высокой адгезией. Немаловажно и то, что порошковое окрашивание позволяет сделать поверхность металла любой с точки зрения цвета, в том числе и искусственно состаренной, например, под стиль антик.
Сегодня популярен такой способ окраски стального проката, как Coil Coating. Суть метода в том, что покрытие наносится на автоматизированной линии, то есть листы рулонного проката обрабатываются на линии, после чего на них валиковыми машинами наносится покрытие. Данная технология получила распространение благодаря тому, что нет потерь материалов, а сама линия более производительна, а потому и выгодна.
Как и при любых других отделочных работах, сначала требуется подготовить поверхность, после чего выполняется ее окраска. Данная технология позволяет вести качественную обработку стали, алюминия и белой жести. Таким образом, полимерное покрытие - это возможность улучшить эксплуатационные свойства металла, повысить его защитные свойства и обеспечить длительность эксплуатации.
Для создания качественной поверхности можно использовать полиуретановые материалы или эпоксидные. Такие материалы приобретают все большую популярность. Полиуретановые материалы имеют немного другие свойства, чем эпоксидные.
– это выравнивающие составы, которые выполнены из полимерных материалов. Эти материалы можно использовать на основаниях из бетона в качестве финишного покрытия. Они могут быть на основе полиуретанов или эпоксидных смол.
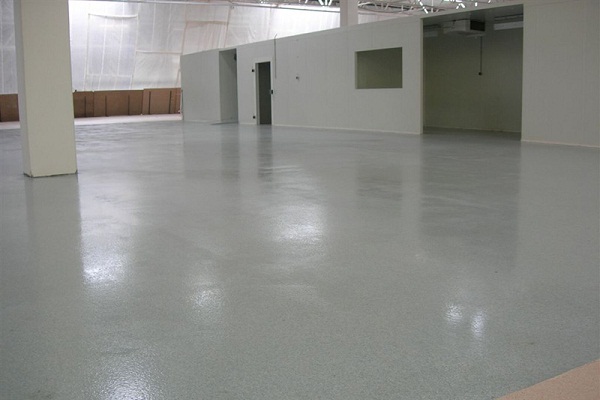
Полиуретановые полы – прочные не скользкие покрытия, при изготовлении которых требуется качественно подготовить основание.
Имеют высокую адгезию к основанию, пластичную и прочную поверхность. Благодаря таким качествам эти материалы широко применяются на различных производствах с вибрирующим оборудованием. Также на производствах, где напольные покрытия подвергаются высоким нагрузкам. На видео можно посмотреть технологию их изготовления.
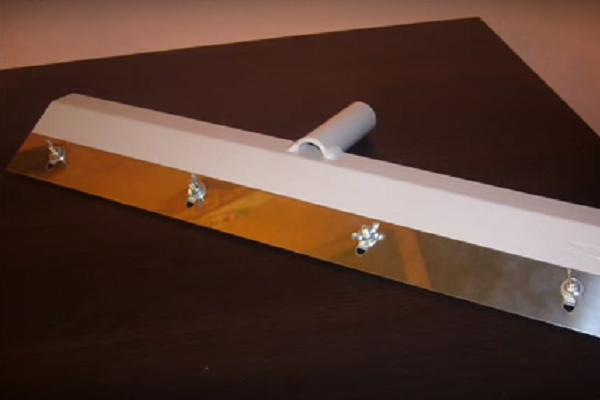
Наливные эпоксидные полы – отвердевают быстрее, и имеют большую плотность, чем полиуретановые. Из-за того что плотность этого покрытия выше, у него более низкая адгезия с основанием и высокая устойчивость к механическим нагрузкам. Широко применяются в зданиях общественного пользования и производственных помещениях. Все этапы производства есть на видео.
Преимущества
- Полимерные полы отличаются высокими показателями стойкости к абразивному износу и ударным нагрузкам.
- Эти покрытия не разрушаются под воздействием химически агрессивных веществ.
- Имеют стойкость к тепловому и ультрафиолетовому воздействию.
- Водонепроницаемость.
- Положительные гигиенические показатели.
- Просты в уборке и ремонте.
- Хорошие декоративные качества.
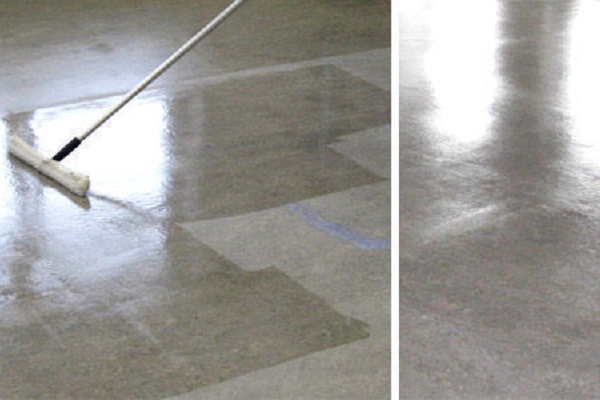
Полимерные полы с применением полиуретанов
Существует несколько способов заливки таких полов, которые позволяют наделить основу нужными эксплуатационными характеристиками. Выбор способа зависит от толщины заливаемого слоя и назначения. С помощью метода нанесения материала можно наделить основу: прочностью и обеспыливаемыми качествами, эстетичным видом или усиленной сопротивляемостью к износу.
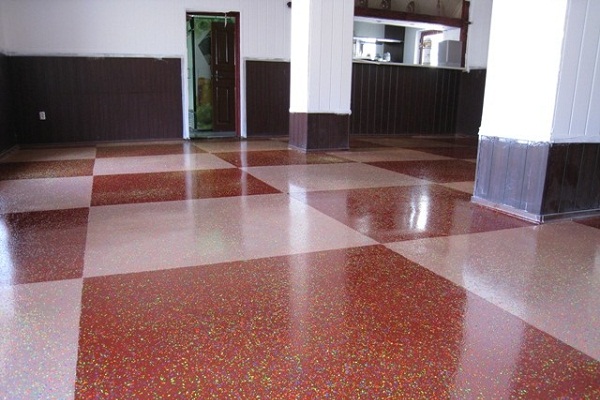
- Полимерные наливные полы, залитые способом кварценаполнения – выдерживают большие нагрузки и прослужат не менее 10 лет. Имеют стойкость к истиранию и эстетичный внешний вид. Состоят из двух слоев: грунтовочный и двухкомпонентный и двухкомпонентный материал с наполнителем из кварцевого песка.
- Тонкослойные полимерные полы – имеют толщину от 0.3 до 1 мм. Состоят из грунтовочного слоя и финишного однокомпонентного. Создают эффект обеспыливания и служит для защиты бетона от разрушений. Применяются в подсобных помещениях, так как не имеют эстетичного вида.
- Наливной способ заливки – полиуретановый пол, заливаемый толщиной от одного миллиметра и выше. Применяется на объектах для создания эстетичного покрытия, которое будет служить для защиты бетона. Не поддаются истиранию и стойко переносят механические нагрузки.
Наливной пол на эпоксидной основе
Благодаря своим положительным качеством этот материал можно встретить во многих организациях общественного пользования. Среди недостатков такого покрытия можно отметить то, что оно наносится сразу на всю площадь помещения. А также то, что после отвердевания компонентов нет возможности произвести ремонт.
При создании напольного покрытия смешивают эпоксидную смолу с отвердителем. Такой состав можно залить практически на любое основание, но рекомендуется производить заливку на подготовленную стяжку. Но перед заливкой на свежую стяжку необходимо выдержать паузу в течение месяца. Так как влажность основание не должна превышать 4%, поэтому необходимо дождаться полного высыхания стяжки. Также можно покрыть ее гидроизолирующим грунтом. Технологию проведения таких работ можно посмотреть на видео.
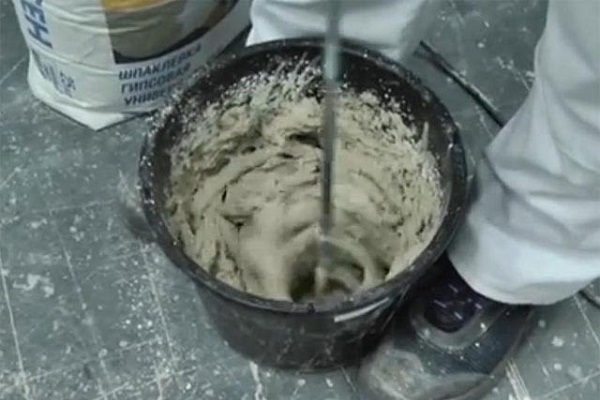
При работах на старой стяжке необходимо тщательно подготовить эту поверхность. Полностью устранить старую облицовку и неровности. Для самовыравнивающие смеси, которые тоже относятся к категории наливных.
Отличие самовыравнивающейся смеси от полимерного пола
В квартире или частном доме используют тонкослойные наливные смеси толщиной 3–5 мм, а в производственных помещениях заливают промышленные наливные полы более толстым слоем. представляет собой сыпучий состав, затворяемый водой, а полимерный состав состоит из компонентов, которые могут быть на основе эпоксидной смолы или полиуретана и вода в таких смесях не используется. Свойства таких смесей позволяют изготовить промышленные наливные полы на больших площадях. Эпоксидные или полиуретановые материалы применяются на основаниях из бетона, а самовыравнивающейся смесью можно выровнять и деревянную основу.
Как самостоятельно залить самовыравнивающуюся смесь
Для устройства такого покрытия требуется подготовить основание таким же образом, как перед тем, как залить эпоксидные полы или полимерные наливные полы. Поверхность бетона или стяжки тщательно очищают и устраняют все недочеты и дефекты. Перед заливкой необходимо покрыть поверхность бетона или стяжки грунтовкой. Этот обеспечит качественное сцепление. Для нанесения грунтовки используют валик или кисть.
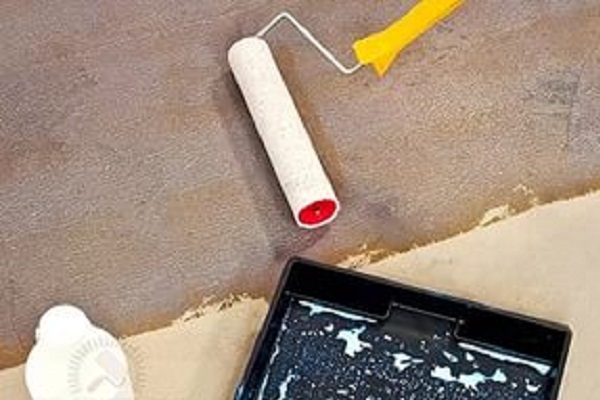
Приклеивают демпферную ленту по периметру помещения. На видео можно посмотреть, как это сделать.
Демпферная лента изготовлена из вспененного полиэтилена и предназначена компенсировать температурное расширение бетонных конструкций.
С помощью лазерного уровня нужно промерить периметр помещения и нанести метки на стены, что будут определять толщину слоя и границу, до которой требуется произвести заливку.
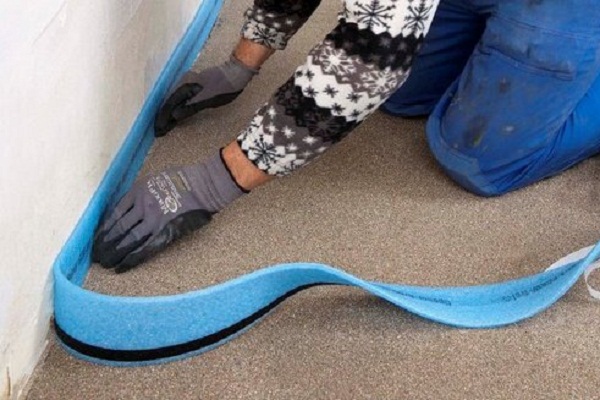
Смесь затворяют в емкости и с помощью перфоратора с венчиком производят тщательное перемешивание компонентов. Загружая компоненты в емкость, нужно соблюдать пропорции, указанные на мешке с самовыравнивающейся смесью. Перемешивание производится до полного устранения комков и получения однородной массы.
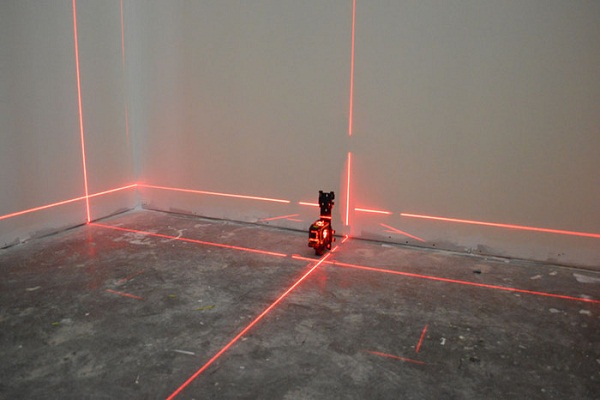
Смесь выливают из емкости на основание из бетона и выравнивают ее с помощью зубчатого шпателя. Затем для ровного распределения прокатывают зубчатым валиком. Уровень смеси должен достигать отметок, которые находятся на стене. После отвердевания состава отрезают фрагменты демпферной ленты.
Технология укладки наливных полов из полимеров
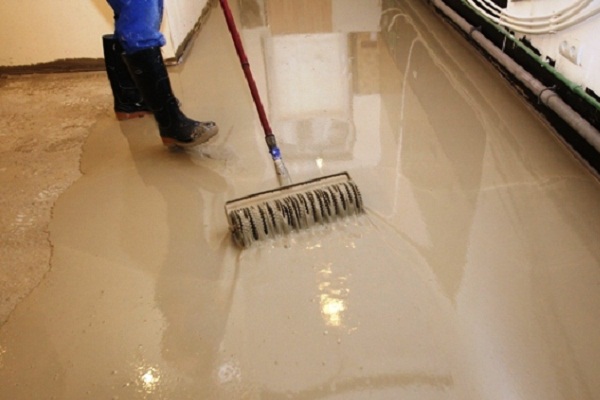
Перед тем как заливать полиуретановые или эпоксидные полы необходимо тщательно подготовить поверхность, от этого зависит качество и долговечность покрытия. Перед началом заливки необходимо полностью очистить поверхность от грязи и пыли. Несмотря на хорошую адгезию, которую обеспечивает грунтовка, не будет лишним обработать поверхность пескоструйной машинкой, которая создаст шероховатость. Если на поверхности бетона имеются демпферные швы, то для их заделки применяются специальные полиуретановые шпаклевки. Трещины замазывают и покрывают серпянкой. Затем, покрывают поверхность непрерывным слоем грунтовки.
После подготовительных этапов начинают заливать полимерные полы своими руками или нанимают специалистов. Для того чтобы равномерно распределить рабочий состав эпоксидные полы или полиуретановые получились ровными, используют ракель.
Для удаления воздушных пузырей, которые образуются при заливке, используют зубчатый валик. Этим инструментом прокатывают состав до полного устранения пузырей.
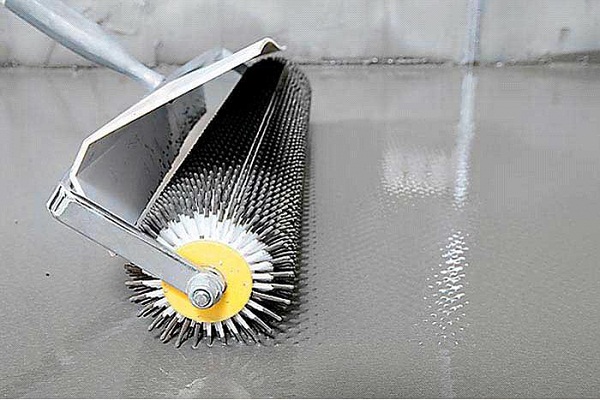
После отвердевания первого слоя наносят финишный по такому же принципу. Все этапы производства таких работ можно посмотреть на видео.
Источники фотографий: evropoll.ru
Как утверждают экологи, порой наш дом по содержанию токсичных веществ опаснее уличного смога. Действительно, если оглянуться, мы окружили себя вещами и материалами из сплошной химии, и даже не представляем, насколько они могут быть опасными. Например, знаете ли вы, какой состав наливного пола действительно безопасен?
1
Практически каждая мало-мальски революционная новинка сталкивается с человеческим страхом. "А это не опасно? Не вредно? Не страшно?" – задавались вопросами люди при виде первого поезда, затем испытанию страхом подвергся мобильный телефон, микроволновая печь… Из всех мифов и слухов могли иметь хоть какое-то основание лишь крупицы, все остальное было не более чем порождением человеческого страха.
Этому же испытанию подверглись и . Логики в человеческих рассуждениях, как правило, нет никакой, одни субъективные доводы и нерациональные поступки. Например, человек стремится обезопасить свой дом от грязной экологии и, поддавшись моде на все экологически чистое, настилает паркет. "Это ведь дерево, а не какой-то полиуре… как там его!" – гордится человек своим стремлением ко всему чистому, покрывая пол полимерным лаком.
И вряд ли его смущает, что полиуретан, который лежит в основе многих наливных полов, имеет прямую связь с полимерным же лаком , поскольку оба относятся к одной группе веществ – полимеры. Человека также не смущает тот факт, что для производства паркета было вырублено несколько деревьев, росших десятилетиями, и мода на все экологически чистое только способствует ухудшению экологии.
Попробуем все же рассуждать объективно. Итак, почему наливной пол можно считать безопасным:
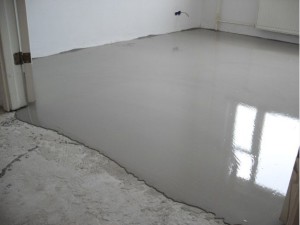
И еще одно доказательство безопасности – пришли к нам из стран Европы и США, где их используют уже около 20 лет и продолжают использовать и по сей день. У них же требования к безопасности окружающей среды еще более жесткие, чем у нас. Именно наливные составы рекомендованы для ремонта помещений, в который живут аллергетики. Так что если вы всерьез заботитесь об экологии и чистоте вашего дома, возможно, вам все же следует изменить ваше мнение?
2
Многие строители не рекомендуют поверх системы "Теплый пол". Зачастую авторы совета обходятся без пояснений, что дает повод для домыслов. Один из них говорит, что при воздействии тепла компоненты наливных составов начинают наполнять воздух в доме.
Однако по факту мы имеем дело с другим недостатком полимерных полов, да и то не всех, а только – эпоксидные смолы при нагревании трескаются, поскольку не обладают нужной эластичностью для расширения.
Полимерные же и метилметакрилатные составы не только отлично расширяются, но и обладают огромным запасом по порогам минимальной и максимальной температур. Для метилметакрилатных это значение колеблется от -70 °С до +150 °С – значения, которые вряд ли возникнут в условиях вашей квартиры или дома. Так что полимерные составы пригодны и для наливных полов, кроме эпоксидных.
Еще один недостаток – небольшой диапазон цветовых решений. Хотя с помощью полимерных пленок и красителей умелые дизайнеры могут исправить положение и внести огромное разнообразие. Впрочем, в сфере ремонта квартир их услуги пока мало востребованы – людям хватает и тех решений, что есть.
Покупая смесь, доверяйте проверенным производителям. Только весьма образованный в сфере химических наук человек сможет действительно понять, из чего состоит наливной пол, тогда как обывателю неизвестные названия покажутся набором букв. Этим могут воспользоваться производители, которые желают сэкономить на дешевых компонентах и наполнителях.
3
К недостаткам наливных покрытий можно было бы отнести и достаточно высокую цену, однако если учесть длительность эксплуатации, то цена становится скорее достоинством, чем недостатком. В любом случае, вы можете сэкономить на его обустройстве – какой бы состав наливного пола вы не выбрали, заливку вы сможете сделать своими руками.
Самое сложное в этом деле – подготовка поверхности. Она должна быть достаточно ровной, без трещин и щелей, очищенная от предыдущих материалов и покрытая грунтом. Объективно говоря, самое лучшее основание для заливки – это бетонная или цементно-песочная стяжка. Если же стяжку можно назвать ровной с большой натяжкой, то и это положение мы можем исправить за счет тех же наливных полов.
Некоторые заливают слой раствора, добавляя в него для удешевления побольше очищенного и мелкого песка. Хотя если поступить совсем по уму, то можно купить специальный состав для так называемого базового или среднего слоя. Они гораздо дешевле и менее прочны, но от них требуется только создание ровного основания. Поэтому базовый слой заливается в тех случаях, когда перепады между сторонами пола достигают от 10 до 80 мм.
Если перепад меньше, до достаточно будет и среднего состава, который может образовать слой от 7 до 50 мм. А уже поверх него достаточно будет залить финишный, тот самый, полимерный слой толщиной в 1-1,5 мм. Максимум – 3 мм, больше и не надо. Выполнять работы лучше с помощником, особенно если вы решили заливать быстросохнущие метилметакрилатные составы.
Важный нюанс – поскольку поверхность получится монолитной, ей нужно пространство для теплового расширения. То есть по периметру стен между слоем напольного покрытия и поверхностью стен должно быть несколько миллиметров пустого места. Обеспечить это очень легко – нужно лишь проложить специальную ленту из пористого материала. Раствор не сможет ее продавить вплотную к стене, зато после того, как он застынет, вы без труда сможете ее вынуть. Образовавшиеся щели следует замазать силиконовым герметиком, и можно не беспокоиться о том, что пол пойдет трещинами.
Раствор замешивают небольшими порциями, по мешку, и разливают по поверхности, начиная с дальнего угла или самой высокой точки. С помощью специального инструмента – ракеля – раствору нужно помочь распространиться по всей поверхности. Чтобы было удобно передвигаться, на обувь наденьте специальные насадки-краскоступы, которые ничем не повредят покрытию.
В зависимости от состава, ходить по поверхности покрытия можно будет через 2-7 часов, а полное застывание наступает как минимум через сутки. Во многом это зависит от температурного режима – важно, чтобы при работах температура не опускалась ниже +10 °С, а лучше была на отметке двадцати градусов.
Основное предназначение напольных покрытий, выполненных из эпоксидных композиций, - предотвращение образования пыли и защита бетонных и цементно-полимерных полов от воздействия агрессивных сред. Еще одно назначение - придание полу декоративности.
Классифицируют эпоксидные составы чаще всего по двум признакам:
- толщине наносимого слоя;
- наличию наполнителей.
Еще один способ дифференциации эпоксидных композиций - по химическому составу. Для изготовления полов применяют как чисто эпоксидные составы, так и комбинированные - эпоксидно-полиуретановые, эпоксидно-каучуковые.
На украинском рынке наибольшее распространение получила эпоксидная краска - мелкодисперсный материал, наносимый валиком тонким слоем (0,2-0,4 мм).
Фото — Полимерные полы
Большинство предлагаемых на украинском рынке эпоксидных составов имеет короткое время жизнеспособности смеси. Двухкомпонентные материалы, используемые для устройства полов, начинают полимеризоваться в своем большинстве через 15-20 мин. при нормальной температуре и влажности (в промышленной холодильной камере это время, разумеется, увеличивается).
Но есть композиции как с более длинным временем жизнеспособности, так и более коротким, например, составы, используемые для ремонта эпоксидных покрытий, у которых время схватывания может не превышать и 5 мин. По словам Николая Пукаса, президента концерна «Макротех», жизнеспособность смеси определяется тем, какой отвердитель и в каком количестве был использован. Можно изготовить смесь, которая будет пригодна к нанесению в течение 15 минут, а можно и 8 часов.
Полное отверждение происходит в зависимости от используемого отвердителя, его концентрации и условий окружающей среды (температуры окружающей среды, температуры основания). Через 9 суток происходит полная полимеризация, набирается максимальная прочность и химическая устойчивость, но нагрузку можно давать и раньше - приблизительно 70-80% полимеризации происходит за первые три дня.
Работы по нанесению эпоксидных композиций выполняются при температуре окружающей среды от +10°С (если необходимо получить высококачественное глянцевое покрытие, то температура должна быть не ниже 15°С.
Структура наливного полимерного пола
Конечно, можно добавить поверхностно-активные вещества и работать при более низкой температуре, но это приводит к ухудшению свойств), а температура основания должна быть на 2-3°С выше точки росы. Очень важна также и влажность основания. Как утверждает Елена Ганул, она должна быть не более 2-3%. Впрочем, есть и исключения - так называемые вододисперсные (водоразбавляемые) эпоксидные материалы.
Эпоксидно-каучуковые составы имеют относительное удлинение до 10%, в то время как обычный эпоксидный состав - всего 2%. Они обладают меньшей вязкостью, более высокой текучестью по сравнению с обычными эпоксидами, более высокой устойчивостью к возникновению микротрещин.
Обычный эпоксидный состав выдерживает давление на сжатие до 400 кг/кв.см, эпоксидно-каучуковые составы выдерживают на растяжение 600-700 кг/кв.см, а на сжатие - до 900 кг/кв.см, поэтому они имеют большую трещиностойкость, более эластичны. (Про стеновые мдф панели )
Самое узкое место при изготовлении полов (впрочем, не только, также и при нанесении, например, лакокрасочного покрытия) - это граница раздела, являющаяся концентратором напряжений. Для этого необходимы праймеры, которые не только улучшают адгезию к основанию, но и хорошо пропитывают основание, укрепляя его. Кроме этого, желательно чтобы п рай мер создавал гидроизоляционный эффект. Эпоксидно-каучуковые составы, по заключению НИИСП, имеют глубину проникновения в бетон до 27 мм, устраняя таким образом границу раздела материалов, по которой и возникает большинство дефектов.
Стоимость эпоксидно-каучуковых составов - приблизительно 10 долл./кг. Расход композиции при грунтовании составляет от 0,15-0,2 кг/кв.м до 0,3 кг/кв.м. Для выполнения напольного покрытия требуется приблизительно 2 кг.
Итого получается 2-2,5 кг/кв.м готового покрытия для больших нагрузок, которые могут выдержать и даже гусеничную технику. Слабые полы (склад, фармацевтическая промышленность, швейная и пр., где требуется хорошая приспособленность к уборке, отсутствие швов) требуют 0,2-0,3 кг на пропитку и 0,5 кг на финишный слой. В итоге вместе с работой квадратный метр готового покрытия может обойтись в 15 долл.
Полиуретановые композиции
Жизнеспособность двухкомпонентных материалов, как правило, невелика - при температуре 20°С приблизительно 30 минут . Полимеризация полиуретановых покрытий происходит приблизительно через 1,5-2 суток. Спустя это время допускаются пешеходные нагрузки и нанесение следующего слоя либо другого покрывного материала.
Наиболее весомое преимущество полиуретановых полов - очень высокая износостойкость, а самый крупный недостаток - слабая адгезионная прочность, его нужно хорошо прикрепить к основанию. Второй изъян - большинство полиуретанов не очень хорошо переносят щелочную среду, в том числе и имеющуюся в бетоне. (Про утепление стен пенополистиролом )
Поэтому со временем полиуретановые покрытия начинают отслаиваться. В этой связи полиуретановые покрытия требуют хорошей грунтовки. Вариантом решения этой проблемы, по мнению Николая Пукаса, может быть использование эпоксидных высокотекучих (с высокой проникающей способностью) праймеров, на которые затем наносится полиуретано- вый слой. В этом случае полиуретан хорошо «пришивается» к эпоксидному праймеру, который в свою очередь создает плавный переход бетон-полимер.
Химическая стойкость полимерных полов
Полиуретановые покрытия стойки к воздействию воды, этилового спирта (концентрация 50%), бутилового спирта, глицерина, бензина, дизельного топлива, моторного масла; 5-процентного раствора муравьиной, молочной и уксусной кислот; 10- процентного раствора фосфорной и хромовой кислот, борной кислоты (4%), 5-процентного водного раствора аммиака, формальдегида (37%), раствора каустической соды (30%). В течение короткого времени покрытия выдерживают толуол, ксилол, бензол, являются нестойкими к ацетону, бутилацетату, четыреххлористому углероду.
Пожарная безопасность
После полного отверждения полиуретанового покрытия оно по горючести относится к классам Г1 (трудногорючий), В2 (трудновоспламеняемый), РП2 (слабораспространяющий пламя), Д2 (умеренное дымообразование), 12 (умеренно опасный по токсичности продуктов горения).
Метилметакрилатные смолы
Наливные полы из метилметакрилатных смол (ММА-смолы) - относительная новинка для украинского рынка, хотя в мире их используют достаточно давно - более 50 лет. По мнению специалистов харьковской компании «Фокс».
Область использования систем на основе ММА-смол достаточно широка. Их применяют в производственных помещениях предприятий пищевой, фармацевтической, химической, легкой индустрии и пр., холодильных и морозильных камерах, лечебных учреждениях, складских помещениях, гаражах, спортивных сооружениях, офисных помещениях, торговых центрах, выставочных залах, предприятиях общественного питания и т.д. Используют их также для срочного ремонта дорожных и аэродромных покрытий.
Достоинств у систем на основе ММА-смол достаточно много:
- высокая долговечность и устойчивость к погодным условиям;
- водонепроницаемость;
- устойчивость к ультрафиолетовому воздействию;
- высокая износостойкость, низкая истираемость, устойчивость к ударным нагрузкам;
- стойкость к воздействию химикатов, горячей воды и растворяющих веществ;
- устойчивость к перепадам температур;
- ремонтопригодность;
- высокий производственный цикл - до 500 кв.м в сутки (по готовому основанию);
- ровность, нескользкость, монолитность, трещиностойкость, отсутствие пыли, удобство по уходу;
- чрезвычайно короткое время твердения. После двух часов уложенные полы полностью набирают свои механические и химические защитные свойства, что позволяет осуществлять ремонтные работы без остановки, например, производственного процесса;
- возможность укладки при очень низких температурах (до -25°С), что позволяет проводить, например, ремонтные работы в холодильных и морозильных камерах.
Ведущие изготовители систем на основе ММА-смол предлагают как правило, несколько видов систем, имеющих различное предназначение. Например, немецкая компания Silikat GmbH & Co .
KG предлагает пять видов покрытия:
- тонкослойные покрытия толщиной до 1-2 мм, гладкие или антискользкие, используемые для внутренних работ;
- самовыравнивающиеся толщиной 4-6 мм, отличающиеся антискользящими свойствами для поверхностей, эксплуатирующихся во влажных помещениях.
Основой всех композиций являются двух компонентные бесцветные ММА-смолы, не содержащие растворителей. Цветовое решение покрытия, в зависимости от требований по дизайну и прочности, достигается посредством добавления пигментов, цветных «чипсов» и цветного кварцевого песка. Покрытия наносятся послойно при помощи длинношерстного валика или металлической кельмы (шпателя).
Для ремонта сколов, выбоин и других дефектов цементосодержащих конструкций применяется ремонтный состав на основе метакрилатной смолы, обладающий высокой прочностью и очень низкой усадкой. Время твердения 30-120 минут.
Химическая стойкость
Покрытия на основе ММА-смол отличаются высокой и удовлетворительной устойчивостью к длинному перечню щелочей, кислот, воды, напитков, растворителей, чистящих средств, крови, масел, жиров. Неудовлетворительную устойчивость системы имеют к муравьиной, уксусной, азотной (концентрация 65%), серной (80%) кислотам, растворителям - бутиловому эфиру, этилацетату, метанолу, метиленхлориду, п-пропилацетату, толуолу, трихлорэтилену, ксилолу.
Требования к основанию
Основанием под покрытия могут служить бетон, цементно-песчаные стяжки, асфальт, металл, мрамор, мозаичные плитки и другие материалы, обладающие несущей способностью и плотно сцепленные с нижележащим слоем.
3D полимерный наливной пол — технология
На современном рынке строительных материалов относительно недавно появился новых тип напольного покрытия ― наливные полимерные полы. Особенностью покрытия является то, что его не укладывают, как традиционные виды материалов, а наливают. Внешне полимерный наливной пол напоминает обычный линолеум, хотя по своим характеристикам он превосходит практически любой вид линолеума.
Что такое полимерный жидкий пол?
В качестве основы для наливного состава используются деревянные, бетонные и металлические перекрытия. Толщина слоя может варьироваться в пределах от 1 до 8 мм. Все зависит от типа помещения, динамической нагрузки на покрытие и влажности.
Полимерное покрытие пола применяется практически в любых типах закрытых помещений, в том числе, в торговых центрах, ресторанах и медучреждениях, где эстетическим показателям уделяется особое внимание.
Полиуретановые составы используют в различных сферах строительства:
- бытовое. жилые помещения: санузлы, кухни, коридоры, лоджии;
- «горячие цеха»;
- паркинги, торговые площади закрытого типа, магазины, автостоянки, рестораны, складские помещения;
- пищевая отрасль;
- промышленные морозильники.
Как показано на фото, для спортивных площадок чаще всего применяют составы на основе полиуретана, которые наносят минимум в два слоя. Толщина основного слоя при этом составляет минимум 10 мм, а финишного ― 3 мм.
Виды полимерных покрытий
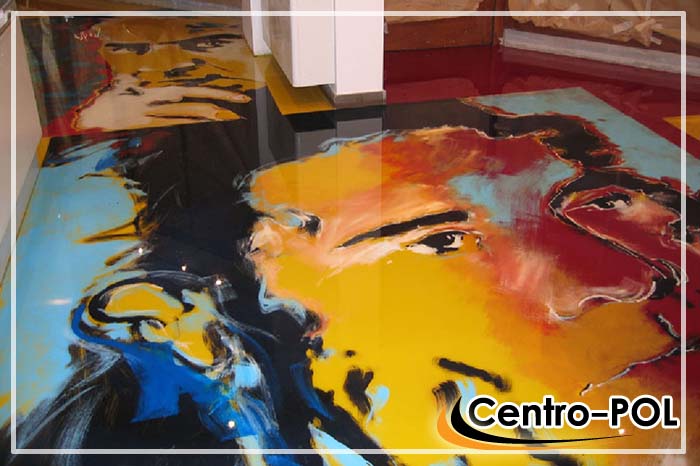
Наливной пол на полимерной основе, в зависимости от состава, может быть таких видов:
- Метилметакрилатный. Данный состав имеет целый ряд универсальных свойств. Смесь достаточно быстро застывает, при этом заливку можно делать даже в помещениях с низкой температурой. Поверхность получается очень прочной и надежной, поэтому полимерные наливные полы можно подвергать серьезным динамическим нагрузкам;
- Эпоксидный состав полимерных полов позволяет применять их в помещениях с высоким уровнем влажности. Также они обладают устойчивостью к химическому и механическому влиянию. Поэтому их нередко можно встретить в лабораториях и фармацевтических предприятиях;
- Полиуретановые смеси. Свойства полимерных полов этого типа очень разнообразны. В отличие от других материалов, полиуретан имеет хорошую эластичность и прочность, поэтому покрытие не подвержено ударной деформации. Чаще всего его используют в жилых помещениях, где поверхности нередко подвергаются механическому влиянию;
- Полиэфирные материалы отличаются низкой стоимостью, что отражается и на характеристиках самого пола. Назвать долговечным этот вид покрытия нельзя из-за низкого уровня устойчивости к механическим повреждениям;
- Цементно-акриловые смеси. Полимерные заливные полы данного вида производятся на основе сухих строительных составов. Поверхность получается достаточно прочной, к тому же покрытие не боится значительных перепадов температур.
Наливной пол из полимерного покрытия имеет не только хорошие технические параметры, но и прекрасные эстетические характеристики. Благодаря этому, их применяют в частных жилищах, офисах, торговых павильонах, магазинах.
Типы полов и сферы применения
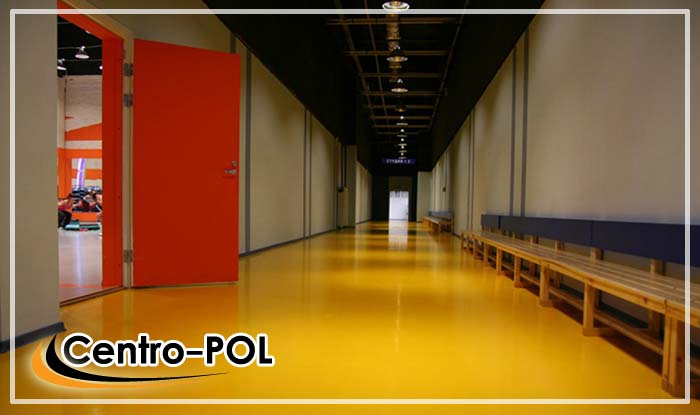
Каждая отдельная промышленная отрасль отличается своими специфическими условиями, в соответствии с которыми подходит тот или иной тип напольного покрытия. К основным разновидностям относятся:
- Декоративные. Обладают прекрасными эстетическими свойствами и широкой цветовой гаммой. Используются в выставочных залах, торговых павильонах, а также офисах. Они устойчивы к УФ излучениям, благодаря чему матовая или глянцевая поверхность не блекнет с течением времени;
- Противоскользящие. Применяются в области переработки продуктов питания, где поверхность часто подвергается влиянию жидкостей. Благодаря герметичности полов, удается избежать протекания. В жилых помещениях устанавливаются на кухнях и в санузлах;
- Гидроизоляционные. В местах сосредоточения водоотводящих желобов и сливов, это тип полимерного покрытия является самым оптимальным. Ведь он предотвращает попадание влаги под пол, вследствие чего под ним не развиваются колонии вредных микроорганизмов;
- Паропроницаемые. Незаменимы для частных домов и квартир, расположенных на первых этажах. Если у вас возникают сомнения в качестве гидроизоляции под металлическим или бетонным основанием, паропроницаемые составы подойдут для решения этой проблемы;
- Антистатические. Применяются в сфере электроники, где нежелательно накопление статического электричества, которое может повлиять на работу оборудования. Нередко они встречаются на взрывоопасных и электрохимических производствах.
Толщина напольного покрытия
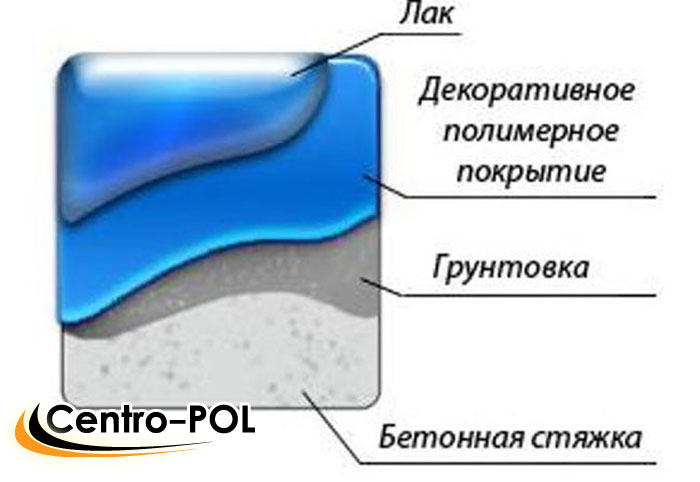
Полимерное напольное покрытие также различается по толщине образуемого слоя, которая влияет на технические характеристики материалов:
- Высокопрочные. Толщина слоя в данном случае составит не меньше 6 мм. Этот вид полов способен выдержать любую нагрузку, благодаря высокой прочности поверхности;
- Средней прочности. Толщина слоя не превышает 2-3 мм. Несмотря на то что поверхность получается достаточно тонкой, полимерные жидкие полы обладают неплохой механической устойчивостью;
- Тонкие. Как правило, используются в квартирах, где уровень нагрузок небольшой. Толщина слоя в таких покрытиях не превышает 1,5 см;
- Обеспыливающие. Такая полимерная смесь для пола наносится очень тонким слоем на бетонную или металлическую основу. Их роль ― защита основания от пыли и загрязнений за счет антистатического свойства;
- Окрашивающие. Полимер наносят только для того, чтобы окрасить поверхность. Проще говоря, его используют в качестве краски для придания поверхности нужного оттенка.
Преимущества и недостатки полимерных полов
Выяснив важные технические характеристики покрытий, стоит оценить их плюсы и минусы. И только потом следует сделать свой выбор в пользу того или иного типа пола.
Преимущества
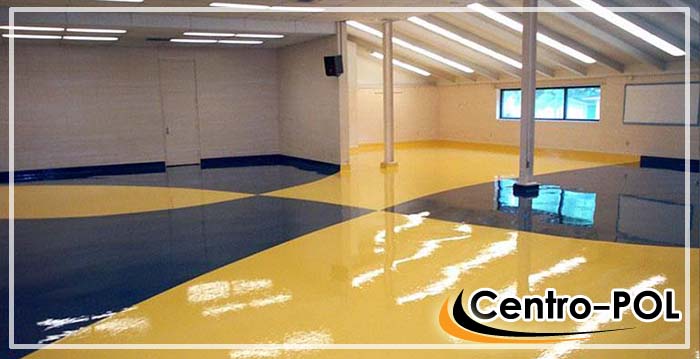
Многочисленные отзывы потребителей, применявших полимерные составы, являются положительными. Хотя это и не удивительно, ведь они имеют очень важные преимущества, к которым относятся:
- Износостойкость. Поверхность практически не истирается со временем и не трескается. На пол можно даже воздействовать абразивными веществами и с ним ничего не случится;
- Химическая пассивность. Полимерные смеси для наливного пола не вступают в реакцию с химическими реактивами;
- Монолитность. Бесшовность поверхности делает ее герметичной. Это значительно упрощает процедуры по уходу за полом. Ведь он не пропускает воду и не является благоприятной средой для размножения бактерий;
- Антистатические свойства не позволяют пыли скапливаться на поверхности;
- Жароустойчивость. Достаточно высокая температура эксплуатации полимерных полов позволяет использовать покрытие в пожароопасных условиях. Дело в том, что составы изготавливают из специальных негорючих материалов. Поэтому их нередко применяют в нефтяной промышленности.
Недостатки
Как и любой другой тип покрытия, полимерный также имеет свои недостатки, которые нужно учесть при выборе пола:
- Небольшой выбор цветов;
- Со временем поверхность может пожелтеть, если за ней не ухаживать;
- Трудоемкий процесс заливки. При несоблюдении технологического процесса, могут возникать пузырьки на покрытии. В такой ситуации придется демонтировать пол, но это сделать весьма непросто.
На видео представлены материалы, благодаря которым вы сможете оценить все преимуществ и недостатки полиуретанового пола.
Компонентный состав
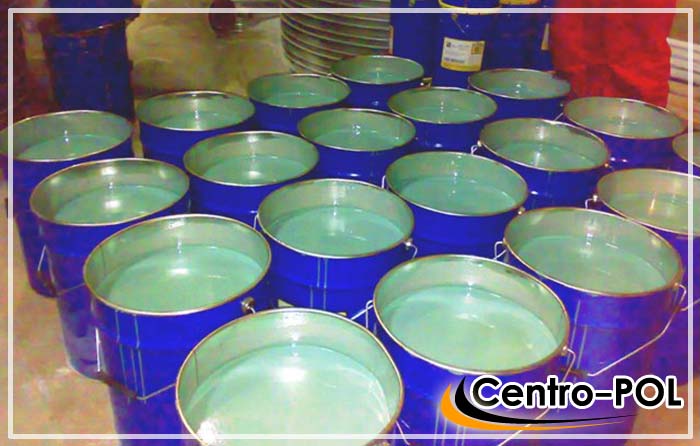
Материалы для полимерного пола могут быть одно-, двух- и трехкомпонентными. Самыми распространенными считаются двухкомпонентные смеси, состоящие из базового материала (Б) и отвердителя (Р).
Компоненты базы включают в свой состав полимерную смолу, различные пигменты, а также микронаполнители. Также, помимо базы и отвердителя, в состав смеси производители могут включать дополнительные добавки. Чаще всего это делают для улучшения характеристик покрытия или же увеличения срока хранения смесей.